Quality Control Integration in Production Planning
In the dynamic landscape of food and beverage manufacturing, where consumer demands constantly evolve and regulatory standards tighten, ensuring product quality is non-negotiable. Quality control is not just about meeting regulatory requirements but also about safeguarding brand reputation and consumer trust.
However, achieving and maintaining high-quality standards while optimizing production efficiency poses a significant challenge for manufacturers. This is where the integration of quality control into production planning becomes indispensable.
In this blog, we look into the pivotal role of quality control integration in production planning for food and beverage manufacturing facilities. We will explore how this integration streamlines operations, enhances product quality, and maximizes overall efficiency, with a focus on the integration between PlanetTogether, a leading production planning software, and prominent ERP, SCM, and MES systems like SAP, Oracle, Microsoft, Kinaxis, and Aveva.
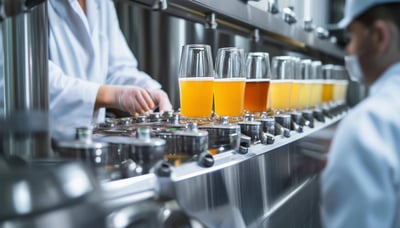
Understanding the Significance of Quality Control Integration
Quality control integration in production planning involves embedding quality checks and measures seamlessly into the production process. Traditionally, quality control has been viewed as a post-production activity, where products undergo inspection after they are manufactured. However, this reactive approach is not conducive to modern manufacturing demands, where agility and proactive measures are paramount.
By integrating quality control into production planning, manufacturers can detect and address potential quality issues in real-time, minimizing the risk of defective products reaching consumers. This proactive approach not only reduces costs associated with recalls and rework but also enhances customer satisfaction and brand loyalty.
-May-08-2024-04-36-12-8483-PM.png?width=300&height=48&name=logo%20(2)-May-08-2024-04-36-12-8483-PM.png)

The Role of Production Planning Software in Quality Control Integration
Production planning software, such as PlanetTogether, serves as the backbone of manufacturing operations, facilitating efficient resource allocation, scheduling, and capacity planning. When integrated with ERP, SCM, and MES systems, these platforms become even more powerful, enabling seamless data flow across the entire manufacturing ecosystem.
In the context of quality control integration, production planning software plays a crucial role in orchestrating quality checks at every stage of the production process. By incorporating quality control parameters into production schedules and workflows, manufacturers can ensure that each batch meets the desired quality standards without disrupting production efficiency.
Streamlining Operations with ERP Integration
Enterprise Resource Planning (ERP) systems serve as the nerve center of manufacturing operations, integrating various business processes and functions into a unified platform. When integrated with production planning software like PlanetTogether, ERP systems enable real-time visibility into inventory levels, production schedules, and quality control metrics.
For food and beverage manufacturers, integrating PlanetTogether with ERP systems such as SAP, Oracle, or Microsoft Dynamics allows for seamless communication between production planning and other business functions. Quality control parameters can be embedded directly into production orders and work instructions, ensuring that quality standards are upheld throughout the manufacturing process.
Enhancing Supply Chain Collaboration with SCM Integration
Supply Chain Management (SCM) systems play a pivotal role in optimizing the flow of materials, information, and finances across the entire supply chain. By integrating SCM systems with production planning software, manufacturers can synchronize production schedules with supplier deliveries, demand forecasts, and inventory levels.
In the context of quality control integration, SCM systems enable manufacturers to collaborate closely with suppliers to ensure the quality of raw materials and ingredients. Real-time visibility into supplier performance metrics and quality certifications allows manufacturers to make informed decisions and mitigate quality risks upstream in the supply chain.
Empowering Real-Time Decision Making with MES Integration
Manufacturing Execution Systems (MES) bridge the gap between planning and execution, providing real-time visibility and control over shop floor operations. When integrated with production planning software like PlanetTogether, MES systems enable seamless data exchange between production scheduling and shop floor execution.
In the realm of quality control integration, MES systems facilitate real-time monitoring of production processes and quality metrics. By capturing data from sensors, IoT devices, and manual inspections, MES systems provide actionable insights into product quality and process performance, empowering manufacturers to make timely adjustments and interventions.
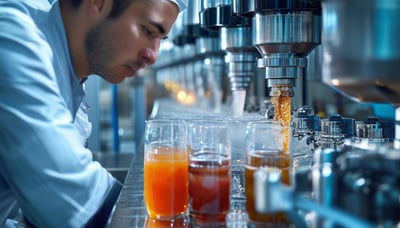
Leveraging Advanced Analytics for Continuous Improvement
In addition to integrating quality control into production planning, manufacturers can leverage advanced analytics to drive continuous improvement initiatives. By analyzing historical production data, quality control metrics, and process parameters, manufacturers can identify trends, patterns, and root causes of quality issues.
Production planning software, when integrated with advanced analytics tools, enables manufacturers to gain deeper insights into the factors influencing product quality and production efficiency. Predictive analytics algorithms can forecast quality risks and recommend preventive measures, while prescriptive analytics models can optimize production schedules to maximize both quality and efficiency.
Quality control integration in production planning is essential for food and beverage manufacturers seeking to achieve excellence in product quality, efficiency, and customer satisfaction. By embedding quality checks and measures seamlessly into the production process, manufacturers can proactively identify and address quality issues, minimizing the risk of defects and recalls.
The integration of production planning software like PlanetTogether with ERP, SCM, and MES systems amplifies the benefits of quality control integration, enabling real-time visibility, collaboration, and decision-making across the entire manufacturing ecosystem. By leveraging advanced analytics and continuous improvement initiatives, manufacturers can drive operational excellence and stay ahead in today's competitive market landscape.
In an era where consumer expectations are higher than ever and regulatory scrutiny is increasingly stringent, quality control integration is not just a strategic imperative but a competitive advantage. By investing in the right technology and partnerships, food and beverage manufacturers can build a foundation for sustained growth, innovation, and leadership in the industry.
Are you ready to take your manufacturing operations to the next level? Contact us today to learn more about how PlanetTogether and integrated scheduling solutions can help you achieve your sustainability goals and drive success in the food and beverage industry.