Quality Control: A Key Driver for Excellence in Industrial Manufacturing
For Plant Managers, ensuring consistent quality is pivotal to operational success, customer satisfaction, and long-term profitability. However, achieving and maintaining high-quality standards across complex manufacturing processes requires robust systems and integration. This is where tools like PlanetTogether Advanced Planning and Scheduling (APS) and enterprise systems like SAP, Oracle, Microsoft Dynamics, Kinaxis, and Aveva come into play.
The Role of Quality Control in Industrial Manufacturing
Quality control involves a series of measures and protocols designed to ensure that products meet predefined standards. For industrial manufacturers, QC impacts:
Customer Satisfaction: High-quality products build trust and foster long-term customer relationships.
Operational Efficiency: Reducing defects minimizes waste, rework, and delays.
Regulatory Compliance: Meeting industry standards is critical to avoid penalties and ensure market access.
Brand Reputation: Consistently delivering quality products enhances brand image and competitive positioning.
Despite its importance, quality control often faces challenges due to siloed systems, manual processes, and limited visibility into production workflows.
The Challenges of Quality Control in Complex Manufacturing Environments
Plant Managers in industrial facilities often contend with challenges such as:
Data Silos: Disconnected systems make it difficult to gather and analyze QC data in real time.
Manual Processes: Paper-based inspections and manual record-keeping are prone to errors.
Dynamic Production Schedules: Rapid changes in schedules can disrupt QC processes, leading to oversights.
Lack of Predictive Insights: Traditional QC methods are reactive, identifying defects after they occur rather than preventing them.
Addressing these challenges requires an integrated approach that combines advanced planning, real-time monitoring, and automated workflows.
Integrating PlanetTogether APS with ERP Systems for Enhanced Quality Control
By integrating PlanetTogether with enterprise systems such as SAP, Oracle, Microsoft Dynamics, Kinaxis, or Aveva, industrial manufacturing facilities can achieve a new level of efficiency and accuracy in quality control. Here’s how:
Real-Time Data Synchronization
Integration enables real-time synchronization of production schedules, inventory levels, and QC parameters across systems. For example:
SAP and PlanetTogether can share production orders and quality specifications to ensure QC processes align with manufacturing schedules.
Oracle ERP’s robust data management combined with PlanetTogether’s scheduling capabilities provides a unified view of quality metrics.
Automated Workflows
Integrating these systems automates key QC tasks, such as:
Triggering inspections at specific production stages.
Recording and analyzing defect data.
Generating reports for compliance and audits.
For instance, a defect identified during an inspection can automatically update schedules in PlanetTogether and trigger corrective actions in Microsoft Dynamics.
Enhanced Traceability
Traceability is crucial in industrial manufacturing, especially for regulated industries. Integration ensures that every product batch is tracked from raw materials to finished goods. Kinaxis’ supply chain orchestration, combined with PlanetTogether’s scheduling, provides end-to-end visibility, enabling swift responses to quality issues.
Predictive Quality Management
Leveraging predictive analytics, systems like Aveva’s Insight can detect potential quality issues before they escalate. When integrated with PlanetTogether, these insights can dynamically adjust schedules to prevent defects, ensuring seamless production.
Improved Decision-Making
Unified dashboards combining data from ERP systems and PlanetTogether give Plant Managers actionable insights. For example:
Identifying bottlenecks impacting quality.
Evaluating supplier performance based on defect rates.
Optimizing maintenance schedules to reduce equipment-related defects.
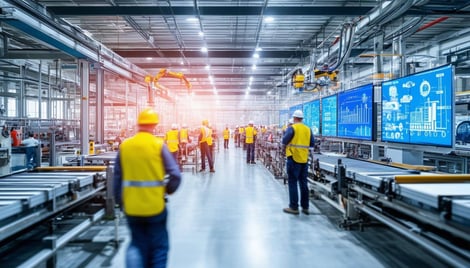
Best Practices for Implementing Integrated QC Systems
To maximize the benefits of integration, Plant Managers should follow these best practices:
Define Clear Objectives: Identify specific QC challenges and set measurable goals.
Ensure Data Accuracy: Clean and accurate data is essential for effective integration.
Engage Stakeholders: Involve QC teams, IT personnel, and production staff in the implementation process.
Invest in Training: Ensure users are proficient in both PlanetTogether and the integrated ERP system.
Monitor and Optimize: Continuously evaluate system performance and make necessary adjustments.
For Plant Managers in industrial manufacturing, quality control is not just about meeting standards; it’s about driving operational excellence and customer satisfaction. Integrating PlanetTogether with ERP systems like SAP, Oracle, Microsoft Dynamics, Kinaxis, or Aveva provides the tools needed to overcome QC challenges and achieve these objectives.
With real-time data, automated workflows, enhanced traceability, and predictive insights, integrated systems transform quality control from a reactive process to a proactive strategy. By adopting these solutions, Plant Managers can ensure that their facilities not only meet today’s quality standards but are also prepared for the challenges of tomorrow.
Are you ready to take your manufacturing operations to the next level? Contact us today to learn more about how PlanetTogether can help you achieve your goals and drive success in your industry.
Topics: Industrial Manufacturing, PlanetTogether Software, Real-Time Data Synchronization, Integrating PlanetTogether, Enhanced Traceability, Improved Decision-Making Agility, Automated Workflows, Predictive Quality Management
LEAVE A COMMENT