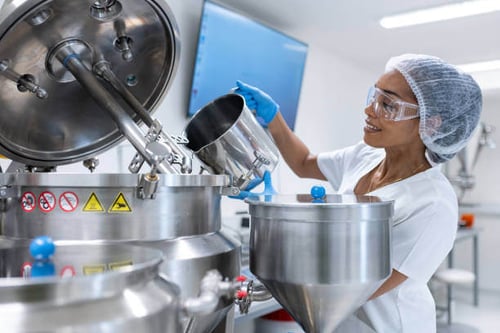
Quality by Design: Enhancing Pharmaceutical Manufacturing through PlanetTogether and SAP Integration
Pharmaceutical manufacturing is a high-stakes industry where product quality is not just a compliance requirement but a crucial factor for patient safety and operational efficiency. In response to regulatory expectations and market demands, Quality by Design (QbD) has emerged as a best practice, ensuring that quality is built into products from the outset rather than being tested in at the end of the production process.
For Plant Managers in pharmaceutical manufacturing, adopting QbD principles means integrating advanced digital solutions that enhance process control, predictive analytics, and real-time monitoring. One such solution is the integration of PlanetTogether Advanced Planning and Scheduling (APS) with enterprise resource planning (ERP) systems like SAP. This powerful combination provides a data-driven approach to process optimization, enabling consistent product quality and compliance with stringent industry regulations.
Understanding Quality by Design in Pharmaceutical Manufacturing
Quality by Design is an FDA-endorsed methodology emphasizing systematic process development with a thorough understanding of how various factors affect product quality. Rather than relying on retrospective quality checks, QbD focuses on designing quality into manufacturing processes. Key components include:
Critical Quality Attributes (CQAs): Identifying the attributes that impact product efficacy and safety.
Critical Process Parameters (CPPs): Defining process variables that influence CQAs.
Design of Experiments (DoE): Using statistical models to determine optimal process settings.
Control Strategy: Implementing real-time monitoring to maintain process consistency.
Risk Management: Assessing and mitigating risks proactively to prevent defects.
By integrating QbD with digital solutions like PlanetTogether APS and SAP ERP, pharmaceutical manufacturers can transform these principles into actionable, real-time workflows that drive efficiency and reliability.
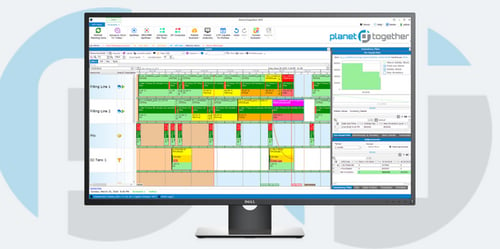
The Role of Digital Integration in QbD Implementation
Digital transformation is redefining pharmaceutical manufacturing, and integrating PlanetTogether APS with SAP enables companies to apply QbD principles in an automated, scalable manner. Here’s how this integration supports QbD:
Enhanced Process Visibility and Control
Integrating PlanetTogether APS with SAP provides real-time visibility into manufacturing operations, ensuring that CQAs and CPPs are consistently monitored. This allows Plant Managers to make data-driven decisions, reducing variability and improving batch-to-batch consistency.
For instance, by linking APS scheduling with SAP’s Material Requirements Planning (MRP), manufacturers can ensure that raw materials meet quality standards before production begins, reducing risks of deviations.
Predictive Analytics for Quality Assurance
Advanced analytics within PlanetTogether APS can predict potential quality issues by analyzing historical production data and identifying patterns that lead to defects. When integrated with SAP’s Quality Management (QM) module, this predictive capability helps in early detection and correction of deviations, significantly reducing waste and compliance risks.
Automated Compliance and Documentation
Pharmaceutical manufacturing is heavily regulated, requiring meticulous documentation for compliance with FDA, EMA, and other global regulatory bodies. The integration of PlanetTogether APS with SAP automates the documentation process, capturing real-time data from production lines and ensuring seamless record-keeping for audits and regulatory submissions.
With digital batch records and automated quality reports, Plant Managers can eliminate manual errors, ensuring traceability and transparency across production processes.
Optimized Scheduling for Continuous Quality Improvement
Scheduling plays a crucial role in maintaining consistent quality, especially for complex pharmaceutical processes such as granulation, tablet compression, and lyophilization. By leveraging PlanetTogether APS, manufacturers can create optimized production schedules that align with quality control checkpoints and reduce variability.
Through SAP integration, these schedules can be dynamically adjusted based on material availability, machine performance, and real-time quality metrics, ensuring production runs meet QbD specifications without unnecessary delays or rework.
Risk-Based Approach to Process Improvement
QbD emphasizes proactive risk management, and the integration of PlanetTogether APS with SAP facilitates risk-based decision-making by providing comprehensive risk assessments and mitigation strategies.
For example, if a supplier’s material quality starts to decline, SAP can trigger alerts, prompting production planners to adjust schedules in PlanetTogether APS to accommodate alternative suppliers or additional quality checks before production.
For Plant Managers in pharmaceutical manufacturing, implementing Quality by Design is no longer an option—it is a requisite for ensuring compliance, reducing waste, and delivering consistent, high-quality products. The integration of PlanetTogether APS with SAP provides a robust digital framework to drive QbD principles into daily operations, offering enhanced process visibility, predictive analytics, automated compliance, optimized scheduling, and proactive risk management.
By leveraging this integration, pharmaceutical manufacturers can shift from reactive quality control to proactive quality assurance, ensuring their products meet the highest standards while improving operational efficiency. Investing in QbD through digital transformation is the key to staying competitive in an increasingly complex and regulated industry.
Are you ready to take your manufacturing operations to the next level? Contact us today to learn more about how PlanetTogether can help you achieve your goals and drive success in your industry.
LEAVE A COMMENT