Optimal Efficiency in Food and Beverage Manufacturing
In the intricate dance of food and beverage manufacturing, the methods of production play a crucial role in determining efficiency, responsiveness, and ultimately, success. At the heart of this debate lies the choice between two predominant manufacturing strategies: Pull and Push.

In this blog, we look deep into the nuances of Pull vs. Push manufacturing in the context of the food and beverage industry, exploring how modern technologies like PlanetTogether and integrated ERP, SCM, and MES systems can elevate operational excellence.
Understanding Pull and Push Manufacturing
Push Manufacturing
Push manufacturing, often associated with traditional mass production models, operates on forecasts and predetermined schedules. In this approach, production is initiated based on anticipated demand, with goods pushed through the supply chain irrespective of real-time market demand.
Pull Manufacturing
On the flip side, Pull manufacturing operates in response to actual demand signals. Instead of relying solely on forecasts, production is triggered by customer orders or consumption data, ensuring that goods are produced as and when needed.
The Debate: Efficiency vs. Responsiveness
The choice between Push and Pull manufacturing often boils down to the age-old debate of efficiency versus responsiveness. Push strategies excel in optimizing production efficiency, leveraging economies of scale and batch processing to drive down costs. However, they fall short when it comes to adapting to fluctuating demand patterns and minimizing inventory holding costs.
On the other hand, Pull strategies prioritize responsiveness, enabling manufacturers to align production closely with real-time demand signals. By producing only what is needed when it is needed, Pull systems minimize inventory levels, reduce lead times, and enhance customer satisfaction. However, they may sacrifice some efficiency gains achieved through economies of scale.
Finding the Balance: The Role of Technology
The key to success lies in striking the right balance between Push and Pull manufacturing. This is where advanced technologies like PlanetTogether and integrated ERP, SCM, and MES systems come into play.
PlanetTogether: Optimizing Production Planning and Scheduling
PlanetTogether stands at the forefront of production planning and scheduling software, empowering manufacturers to optimize their operations with precision and agility. By leveraging advanced algorithms and real-time data insights, PlanetTogether enables plant managers to streamline production workflows, minimize downtime, and maximize resource utilization.
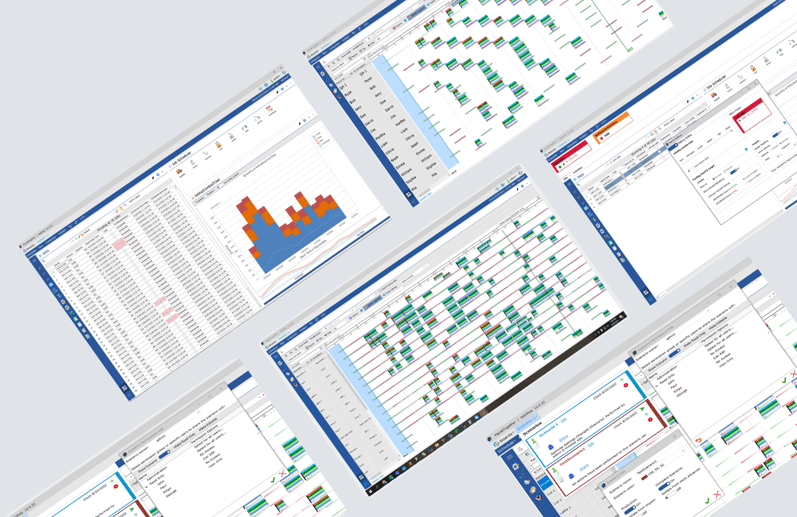
Integration with ERP, SCM, and MES Systems
The true power of PlanetTogether lies in its seamless integration with other essential systems like ERP, SCM, and MES. Whether it's SAP, Oracle, Microsoft Dynamics, Kinaxis, Aveva, or any other ERP system, PlanetTogether can synchronize data across the entire supply chain, ensuring a unified and transparent flow of information.
Benefits of Integration:
Real-Time Visibility: By integrating PlanetTogether with ERP systems, plant managers gain real-time visibility into inventory levels, production schedules, and customer orders. This enables proactive decision-making and rapid response to changing market dynamics.
Enhanced Collaboration: Integrated systems facilitate seamless collaboration across departments, from production and procurement to sales and distribution. This ensures that everyone is working towards a common goal, optimizing resource allocation and minimizing bottlenecks.
Data-Driven Insights: With data flowing seamlessly between systems, plant managers can harness the power of analytics to uncover actionable insights. From demand forecasting to production forecasting, integrated systems enable data-driven decision-making at every step of the manufacturing process.
Improved Traceability and Compliance: In industries like food and beverage, traceability and compliance are non-negotiable. Integrated systems ensure end-to-end traceability, from raw materials to finished products, while also simplifying regulatory compliance through automated reporting and documentation.
The choice between Push and Pull manufacturing is not a binary decision but rather a delicate balancing act. By leveraging advanced technologies like PlanetTogether and integrating them with ERP, SCM, and MES systems, plant managers can achieve the perfect harmony between efficiency and responsiveness.
In doing so, they pave the way for operational excellence, customer satisfaction, and sustainable growth in an ever-evolving industry.
LEAVE A COMMENT