Production Scheduling in the Food Industry
The food and beverage industry is marked by an unforgiving pace and the need for impeccable timing. From perishable goods to fluctuating demand, operations directors face unique challenges in production scheduling.
This is where integrated technological solutions such as PlanetTogether's Advanced Planning and Scheduling (APS) system become crucial. When seamlessly integrated with Enterprise Resource Planning (ERP), Supply Chain Management (SCM), and Manufacturing Execution Systems (MES) like SAP, Oracle, Microsoft Dynamics, Kinaxis, Aveva, and others, these tools can transform the efficiency and responsiveness of production lines.
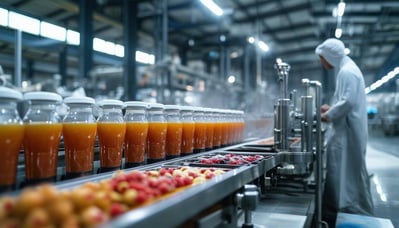
The Importance of Effective Production Scheduling
Production scheduling in the food and beverage industry is not just about maintaining timelines; it's about aligning every part of the manufacturing process to deliver quality products efficiently while minimizing waste and costs. This complex balancing act requires:
Optimal Resource Allocation: Ensuring that every part of the production line is utilized efficiently without overburdening any segment.
Demand Forecasting: Accurately predicting demand fluctuations to adjust production without leading to surplus or shortages.
Compliance and Quality Control: Adhering to strict health and regulatory standards, which require precise control over production processes.
-Apr-01-2024-01-39-55-8668-PM.png?width=300&height=48&name=logo%20(2)-Apr-01-2024-01-39-55-8668-PM.png)
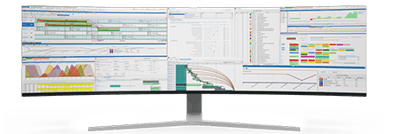
The Role of PlanetTogether in Production Scheduling
PlanetTogether’s APS provides a robust solution that helps operations directors manage these challenges. Its capabilities include:
Multi-Plant Coordination: Allowing synchronization across various production facilities to optimize schedules and resource allocation.
Real-Time Visibility: Offering instant updates on production statuses, allowing for quick reactions to any operational hiccups.
Advanced Analytics: Utilizing historical data and predictive analytics to forecast demand and adjust production schedules proactively.
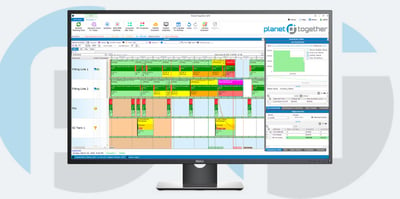
Integration with ERP Systems
SAP Integration
Integrating PlanetTogether with SAP enhances production scheduling by leveraging SAP’s comprehensive ERP tools alongside PlanetTogether’s specialized scheduling features. This integration allows for:
Data Consistency: Ensuring that all data across inventory, procurement, and production is synchronized and accurate.
Streamlined Operations: Allowing for seamless communication between the APS and ERP systems, reducing the time and potential for errors in data transfers.
Enhanced Decision-Making: Providing operations directors with comprehensive insights into both financial and operational metrics.
Oracle Integration
Similarly, integrating with Oracle can leverage its robust database and cloud solutions to enhance scalability and data security in production scheduling. Benefits include:
Scalable Operations: Adjusting production capacity quickly in response to market changes without sacrificing performance.
Secure Data Handling: Employing top-notch security measures to protect sensitive production and financial data.
Integration with SCM and MES Systems
Microsoft Dynamics Integration
When PlanetTogether is integrated with Microsoft Dynamics, it taps into Dynamics' strengths in SCM. This integration optimizes supply chain operations, ensuring that the materials needed for production are available and managed efficiently. Key advantages include:
Enhanced Supply Chain Visibility: Gaining deeper insights into the supply chain allows for better forecasting and inventory management.
Improved Supplier Collaboration: Facilitating better communication and data exchange with suppliers.
Kinaxis Integration
Integrating with Kinaxis, which specializes in rapid response SCM solutions, can significantly enhance the responsiveness of production scheduling to market volatility. This integration helps by:
Speeding Up Response Times: Quickly recalibrating production schedules in response to supply chain disruptions.
Optimizing Inventory Levels: Maintaining optimal inventory levels to meet production needs without overstocking.
Aveva Integration
Aveva’s focus on industrial software offers unique advantages when integrated with PlanetTogether’s scheduling capabilities. This includes:
Real-Time Operational Insight: Gaining a real-time overview of manufacturing operations, enhancing the ability to make informed decisions quickly.
Predictive Maintenance: Implementing predictive maintenance schedules based on accurate production data, reducing downtime and increasing equipment longevity.
For operations directors in the food and beverage industry, the integration of PlanetTogether with ERP, SCM, and MES systems is not just a technical upgrade—it is a strategic necessity. By harnessing the combined strengths of these systems, companies can achieve higher efficiency, better compliance, and ultimately, a stronger market position.
The future of food and beverage manufacturing lies in smart, integrated scheduling solutions that can keep pace with the industry’s demands and challenges. Are you ready to take your manufacturing operations to the next level? Contact us today to learn more about how PlanetTogether can help you achieve your goals and drive success in your industry.