Production Gains with Operations Technologies
Operations Directors in packaging manufacturing face relentless pressure to optimize production, reduce waste, and increase output without sacrificing quality. Achieving these goals requires more than just lean management techniques; it necessitates a robust integration of advanced operations technologies that can streamline workflows, synchronize activities, and maximize efficiency.
This blog explores how leveraging technologies like PlanetTogether, in conjunction with enterprise software solutions like SAP, Oracle, Microsoft, Kinaxis, and Aveva, can drive tangible production gains in packaging manufacturing.
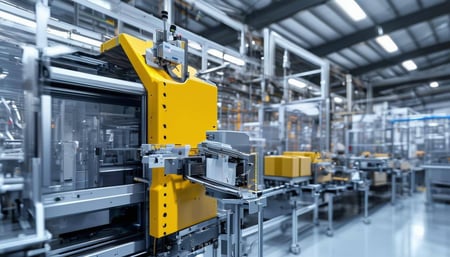
The Need for Integrated Operations Technology in Packaging Manufacturing
Packaging manufacturing is a complex, resource-intensive process that requires precise coordination across various functions—design, procurement, production, and distribution. Achieving this coordination is challenging, especially as manufacturers strive to meet tighter timelines and shifting customer demands. Traditional, siloed approaches to operations management are no longer sufficient; rather, packaging manufacturers must harness the power of integrated operations technologies to achieve their goals. This integration is particularly critical for:
Real-Time Production Monitoring: Instant access to production data helps Operations Directors make swift decisions to optimize throughput.
Advanced Planning and Scheduling (APS): A connected APS system, like PlanetTogether, enhances production planning by balancing demand fluctuations, minimizing bottlenecks, and increasing machine utilization.
Inventory Optimization: Integrated systems provide visibility across the supply chain, preventing stockouts and overstock situations, which improves overall cost-efficiency.
When platforms like PlanetTogether are integrated with ERP systems such as SAP, Oracle, Microsoft, Kinaxis, or Aveva, they create a seamless information flow that supports informed decision-making and greater production efficiency.

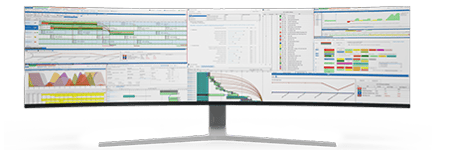
How PlanetTogether’s APS Enhances Production Efficiency
PlanetTogether’s APS software is a powerhouse for managing scheduling complexities in packaging manufacturing. By integrating with ERP systems, it offers key advantages for Operations Directors looking to enhance their facility's performance.
Dynamic Scheduling and Real-Time Adjustments
Unlike static schedules, PlanetTogether’s APS system dynamically adjusts based on real-time data, such as order changes, machine availability, and resource capacity. Integrating it with SAP or Microsoft allows this data to flow seamlessly, ensuring that operations stay in sync and can respond rapidly to unexpected shifts.
Reduced Downtime Through Predictive Maintenance
Downtime remains a significant barrier to productivity. By linking PlanetTogether with systems like Oracle or Aveva, data from machines can be harnessed to predict maintenance needs. Predictive maintenance minimizes unplanned downtime and keeps the production line moving, directly enhancing output.
Enhanced Resource Allocation
Through integrated APS, Operations Directors can view resource availability across multiple production lines and plants. Integration with ERP solutions enables this data to align with real-time demand forecasts, helping to allocate resources optimally and reduce idle times.
Improved Workflow Visibility
Integrating PlanetTogether with Microsoft or Kinaxis provides a bird's-eye view of workflows and bottlenecks. This visibility allows Operations Directors to intervene strategically, either by reallocating resources or adjusting production schedules to maximize throughput and meet delivery timelines.
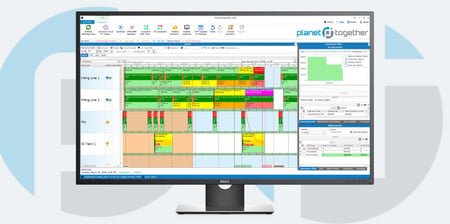
Key Benefits of ERP Integration for Operations Directors
In an era where data is a strategic asset, ERP systems are the backbone of data management for most packaging manufacturers. Integrating APS with an ERP system allows for the seamless sharing of crucial data points, such as order forecasts, inventory levels, and customer demand trends. Here are some pivotal benefits that Operations Directors can expect from ERP-integrated APS solutions:
Streamlined Data Access and Analysis
A single source of truth for production and financial data helps Operations Directors make informed, data-backed decisions. Integrating PlanetTogether with SAP or Oracle facilitates comprehensive data analysis, enabling the identification of patterns that can guide strategic adjustments to production.
Enhanced Demand Forecasting
Demand planning in packaging manufacturing is particularly challenging due to its reliance on client needs. Integrating APS with a robust ERP system like Kinaxis or SAP helps ensure that demand forecasts are not only accurate but also actionable. Operations can be scheduled proactively, avoiding last-minute bottlenecks and enabling smoother production cycles.
Improved Cost Management
Operations Directors are tasked with balancing efficiency with cost. An integrated ERP-APS ecosystem provides granular insights into production costs at each stage, empowering directors to identify areas for cost savings, from labor allocation to material usage, without sacrificing output quality.
Seamless Supplier Collaboration
Efficient supplier collaboration is critical in packaging, especially for just-in-time manufacturing models. Integrating APS with Oracle or Aveva enhances transparency with suppliers, enabling more responsive procurement practices and reducing the risk of production stoppages due to material shortages.
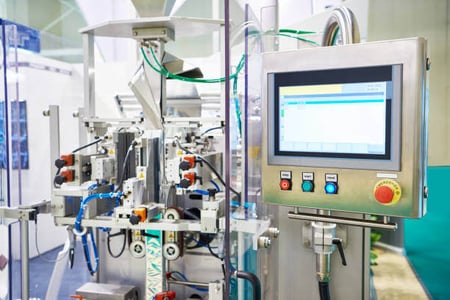
Real-World Applications of Integrated APS and ERP in Packaging Manufacturing
Minimizing Production Waste with Real-Time Inventory Tracking
For an Operations Director, waste reduction is a top priority. By integrating PlanetTogether with an ERP solution like Microsoft Dynamics, packaging manufacturers can leverage real-time inventory tracking to reduce raw material waste. For instance, when stock levels approach critical thresholds, automated alerts allow production to adjust accordingly, reducing excess inventory and preventing stockouts that may lead to production delays.
Boosting Throughput with Optimized Scheduling
In high-demand periods, optimized scheduling is essential to meet production targets without overextending resources. PlanetTogether’s scheduling algorithms, when linked to SAP, dynamically adjust production sequences based on current machine and labor availability. This approach not only minimizes idle time but also enhances throughput by ensuring that each production run is maximally efficient.
Enhancing Quality Control through Predictive Analytics
Quality control in packaging is non-negotiable, given that a defective package can compromise product integrity. Integration with analytics-powered systems like Aveva can help detect potential quality issues in real-time, triggering preventive actions before problems escalate. By connecting APS to such analytics tools, packaging manufacturers can maintain high-quality standards and improve production efficiency.
Adapting Quickly to Demand Changes
Packaging manufacturers frequently need to adjust production based on fluctuating demand. Integrated systems like PlanetTogether and Kinaxis allow Operations Directors to reallocate resources and adjust production schedules in response to these changes. This flexibility ensures that facilities can respond to spikes in demand without compromising the quality or timing of production, which is vital for customer satisfaction and profitability.
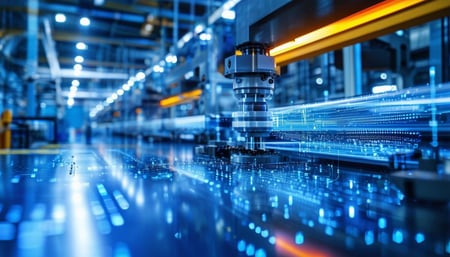
Embracing the Future: Scaling Production Gains with Advanced Technologies
For Operations Directors in packaging manufacturing, integrating APS and ERP systems is a foundational step toward long-term production optimization. However, the industry is evolving, and additional technologies are emerging that can further amplify these gains. Consider the potential of adding the following:
IoT-Connected Machines: By connecting machines to the Internet of Things (IoT), Operations Directors can receive detailed insights into machine health, energy consumption, and productivity. Integrating IoT data into PlanetTogether and an ERP system provides a clearer view of production efficiency.
AI and Machine Learning: Leveraging AI in integrated systems like PlanetTogether allows for advanced predictive analytics. Machine learning algorithms can spot inefficiencies and recommend adjustments that improve scheduling, maintenance, and resource allocation.
Extended Reality (XR) for Training and Maintenance: XR technologies, when integrated with operational data systems, allow plant operators to visualize machine status, receive real-time maintenance instructions, and even train in virtual environments. This innovation reduces downtime due to training gaps and enhances operational readiness.
For an Operations Director in packaging manufacturing, production gains are not just about ramping up output but also about achieving a delicate balance of speed, quality, and cost-efficiency. Leveraging technologies like PlanetTogether APS in tandem with ERP systems such as SAP, Oracle, Microsoft, Kinaxis, or Aveva offers an unparalleled advantage in optimizing operations, reducing waste, and enhancing productivity. These integrated systems provide the real-time data, visibility, and flexibility necessary to meet today's manufacturing challenges.
As packaging manufacturers prepare for the future, embracing integrated operations technologies will be essential to remain competitive. With the right tools and strategies, Operations Directors can drive meaningful, lasting production gains that ensure both immediate improvements and sustainable success in the years to come.
Are you ready to take your manufacturing operations to the next level? Contact us today to learn more about how PlanetTogether can help you achieve your goals and drive success in your industry.
LEAVE A COMMENT