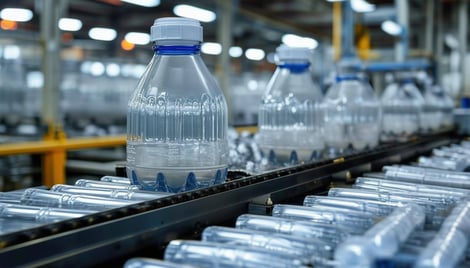
Predictive Scheduling with AI: Anticipating Bottlenecks and Disruptions in Packaging Manufacturing
In packaging manufacturing, staying ahead of potential disruptions and inefficiencies is critical. As a Manufacturing IT Manager, you are at the forefront of driving operational excellence through advanced technologies. Predictive scheduling powered by Artificial Intelligence (AI) has emerged as a game-changer, enabling facilities to anticipate bottlenecks and disruptions before they escalate into costly delays.
Coupled with seamless integration with advanced systems like PlanetTogether and enterprise software such as SAP, Oracle, Microsoft Dynamics, Kinaxis, or Aveva, predictive scheduling is revolutionizing the manufacturing landscape.
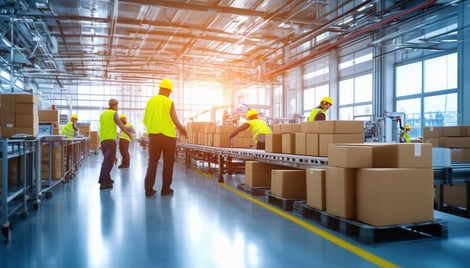
The Challenges of Traditional Scheduling
Packaging manufacturing involves complex processes, often running at full capacity to meet tight deadlines. Traditional scheduling methods, reliant on static data and manual adjustments, struggle to cope with dynamic variables such as:
Sudden equipment breakdowns.
Fluctuations in material availability.
Shifting customer demands.
Workforce constraints.
These challenges lead to inefficiencies, missed deadlines, and increased operational costs. Traditional scheduling systems lack the agility to adapt to real-time changes, leaving manufacturers reactive instead of proactive.
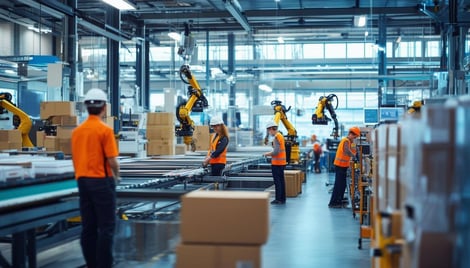
Enter Predictive Scheduling with AI
Predictive scheduling leverages AI and machine learning algorithms to create dynamic, real-time schedules. By analyzing historical data, machine conditions, and current production variables, predictive scheduling enables:
Proactive Bottleneck Identification: AI identifies potential bottlenecks in production workflows, allowing managers to address them before they impact operations.
Disruption Forecasting: Machine learning models analyze trends to predict potential disruptions, such as equipment failures or supply chain delays.
Optimized Resource Allocation: By understanding patterns and predicting needs, AI ensures optimal utilization of machinery, materials, and labor.
Dynamic Rescheduling: Predictive systems can adjust schedules on the fly, ensuring minimal downtime and maximum productivity.

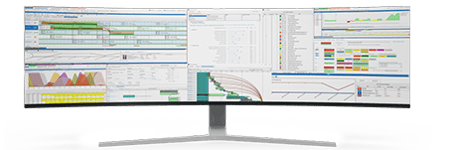
Integration with PlanetTogether and Leading Enterprise Software
To unlock the full potential of predictive scheduling, integration with advanced planning and scheduling (APS) platforms like PlanetTogether is essential. When combined with robust enterprise systems like SAP, Oracle, Microsoft Dynamics, Kinaxis, or Aveva, manufacturers can achieve unparalleled synchronization and efficiency.
Seamless Data Flow
Integration ensures a seamless flow of data between PlanetTogether and enterprise systems. For example:
SAP: Live production and inventory data from SAP feed into PlanetTogether, enabling real-time schedule adjustments based on material availability.
Oracle: Oracle’s comprehensive database integrates with AI-driven scheduling tools to provide deep insights into resource planning and capacity utilization.
Microsoft Dynamics: Predictive algorithms in PlanetTogether use data from Microsoft Dynamics to anticipate and mitigate disruptions in supply chain operations.
Kinaxis: Kinaxis’ rapid-response capabilities enhance the agility of predictive scheduling, allowing manufacturers to quickly adapt to demand fluctuations.
Aveva: Integration with Aveva’s industrial automation tools bridges the gap between planning and execution, ensuring operational precision.
Enhanced Decision-Making
By integrating predictive scheduling tools with enterprise systems, IT managers can access comprehensive dashboards that consolidate data from multiple sources. This integration empowers better decision-making by:
Providing a unified view of production metrics.
Highlighting potential risks and their impact on delivery timelines.
Suggesting actionable insights to mitigate disruptions.
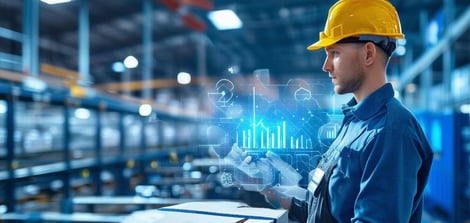
Key Benefits of Predictive Scheduling for Packaging Manufacturers
Increased Throughput
Predictive scheduling optimizes production workflows, reducing idle time and maximizing machine utilization. For example, AI-driven forecasts can predict when a machine is likely to experience downtime, allowing for preemptive maintenance.
Improved Customer Satisfaction
By ensuring on-time delivery through proactive disruption management, manufacturers can consistently meet customer expectations. Integration with CRM modules in SAP or Microsoft Dynamics ensures real-time updates on order statuses.
Cost Savings
Avoiding unplanned downtime and minimizing resource wastage translates to significant cost savings. Predictive systems also reduce reliance on last-minute expedited shipping or overtime labor.
Sustainability Gains
Efficient scheduling reduces energy consumption and material waste, aligning with sustainability goals. Integration with Aveva’s sustainability analytics can further track and report these improvements.
The Role of IT in Driving Change
As a Manufacturing IT Manager, your role is pivotal in driving the adoption of predictive scheduling. Your expertise in system integration, data management, and IT infrastructure ensures the success of such transformative initiatives. Here are a few strategies to lead effectively:
Champion Data-Driven Culture: Advocate for data accuracy and its importance in predictive modeling.
Invest in Training: Equip your team with the skills to manage and optimize AI-driven tools.
Focus on Cybersecurity: Ensure robust data protection measures, especially when integrating multiple systems.
Predictive scheduling with AI is a transformative force in packaging manufacturing, enabling facilities to anticipate and mitigate bottlenecks and disruptions effectively. By integrating PlanetTogether with enterprise systems like SAP, Oracle, Microsoft Dynamics, Kinaxis, or Aveva, Manufacturing IT Managers can unlock new levels of efficiency, agility, and cost savings. As the manufacturing landscape grows increasingly complex, embracing predictive scheduling is not just a competitive advantage—it’s a necessity.
Start your journey towards smarter manufacturing today and position your facility at the forefront of innovation and efficiency.