Predictive Scheduling in High-Variability Packaging Manufacturing
In packaging manufacturing, variability is the norm. Changing customer demands, fluctuating raw material availability, and frequent design updates can make it challenging for production schedulers to meet deadlines while optimizing efficiency. For schedulers, the ability to anticipate and adapt to these dynamic conditions is crucial.
Enter predictive scheduling—a transformative approach powered by advanced technologies such as PlanetTogether and integrated enterprise systems like SAP, Oracle, Microsoft Dynamics, Kinaxis, or Aveva.
The Challenge of High Variability in Packaging Manufacturing
Packaging manufacturing is inherently complex due to the need to produce customized designs, accommodate diverse material types, and maintain high quality standards. For example:
Custom Orders: Clients may require bespoke packaging solutions tailored to their products, leading to frequent schedule adjustments.
Material Variability: Raw materials may differ in availability, quality, or cost, requiring on-the-fly changes to production plans.
Rapid Turnaround Times: Tight deadlines often leave little room for error or downtime.
Traditional scheduling methods struggle to keep pace with these demands. Static schedules quickly become obsolete, and manual adjustments often lead to inefficiencies or missed deadlines.
What Is Predictive Scheduling?
Predictive scheduling leverages data-driven insights and advanced algorithms to forecast potential disruptions and proactively optimize production plans. By integrating real-time data from multiple sources, such as ERP systems like SAP or Oracle and advanced planning tools like PlanetTogether, schedulers can:
Identify Bottlenecks: Detect production constraints before they occur.
Enhance Flexibility: Quickly adapt schedules to accommodate unexpected changes.
Improve Resource Utilization: Allocate labor, equipment, and materials more effectively.
Reduce Downtime: Minimize idle time and increase throughput.

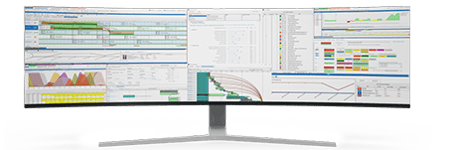
The Role of PlanetTogether and ERP Integration
PlanetTogether’s Advanced Planning and Scheduling (APS) system is a game-changer for production schedulers in packaging manufacturing. When integrated with leading ERP platforms like SAP, Oracle, Microsoft Dynamics, Kinaxis, or Aveva, it provides a unified framework for predictive scheduling. Here’s how:
Data Synchronization
Integration ensures that critical data—such as order details, inventory levels, and production capacity—flows seamlessly between systems. For instance, an update in SAP regarding raw material availability can immediately trigger a schedule adjustment in PlanetTogether.
Real-Time Visibility
With integrated systems, schedulers gain a holistic view of the production floor, supply chain, and customer orders. This visibility enables faster decision-making and better alignment with business goals.
Scenario Planning
PlanetTogether’s APS enables schedulers to simulate various scenarios, such as machine downtime or rush orders. By integrating with platforms like Microsoft Dynamics, these scenarios can incorporate financial impacts, helping businesses make informed trade-offs.
Predictive Analytics
Advanced analytics tools within PlanetTogether use historical data and machine learning to predict potential issues, such as equipment failures or late deliveries. When integrated with Aveva’s industrial solutions, these insights can be enriched with IoT data from the shop floor.
Key Benefits of Predictive Scheduling
Increased Agility
In a high-variability environment, agility is essential. Predictive scheduling allows production teams to adapt quickly to changes in demand, ensuring customer satisfaction without sacrificing efficiency.
Example: A customer places a last-minute order for a custom packaging design. With predictive scheduling, the system can identify available capacity, adjust priorities, and ensure on-time delivery.
Reduced Waste
Predictive scheduling minimizes waste by optimizing material usage and reducing downtime. Integration with ERP systems provides accurate inventory data, helping schedulers plan more effectively.
Example: By analyzing production data, the system identifies an overuse of a specific material and recommends adjustments to the cutting process.
Improved On-Time Delivery
Meeting deadlines is critical in packaging manufacturing. Predictive scheduling enhances reliability by proactively addressing potential delays.
Example: A predictive model identifies a risk of equipment failure and schedules maintenance during off-peak hours, preventing disruptions to production.
Enhanced Collaboration
Integration between PlanetTogether and ERP platforms fosters collaboration across departments. Sales, production, and supply chain teams can align their efforts more effectively.
Example: A sales team using Oracle CRM updates an order priority, which is automatically reflected in the production schedule, ensuring alignment with customer expectations.
Predictive scheduling represents a paradigm shift for production schedulers in packaging manufacturing. By integrating tools like PlanetTogether with ERP systems such as SAP, Oracle, Microsoft Dynamics, Kinaxis, or Aveva, businesses can achieve unprecedented levels of efficiency, agility, and reliability.
For production schedulers, adopting predictive scheduling is not just about keeping up with industry trends; it’s about staying ahead in a competitive landscape. By embracing this innovative approach, you can transform variability from a challenge into an opportunity for growth and innovation.
Are you ready to take your manufacturing operations to the next level? Contact us today to learn more about how PlanetTogether can help you achieve your goals and drive success in your industry.
Topics: PlanetTogether Software, Integrating PlanetTogether, Reduced Waste, Enhanced Collaboration, Increased Agility, Packaging Manufacturing, Improved On-time Delivery Performance
LEAVE A COMMENT