Overcoming Workforce Shortages Through Reskilling
Production planners play a pivotal role in ensuring efficient operations and timely delivery of goods in food and beverage manufacturing. However, the industry is facing an unprecedented challenge - workforce shortages. The aging workforce, coupled with evolving skill requirements and demographic shifts, has created a pressing need for innovative solutions. One such solution lies in reskilling existing employees to meet the demands of the future.
In this blog, we'll explore how production planners can overcome workforce shortages through reskilling initiatives, with a focus on integrating tools like PlanetTogether with leading enterprise resource planning (ERP) systems such as SAP, Oracle, Microsoft, Kinaxis, and Aveva.
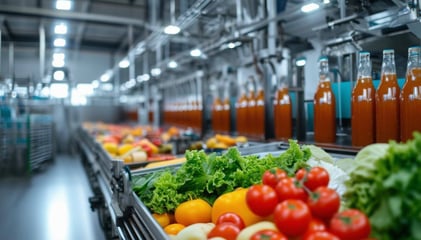
Understanding the Challenge
Workforce shortages in the food and beverage manufacturing sector are multifaceted. The retirement of experienced workers, coupled with a shrinking pool of skilled labor, has created a talent deficit that traditional hiring practices alone cannot remedy. Additionally, rapid technological advancements require workers to possess a diverse skill set, making it imperative for organizations to invest in continuous learning and development.
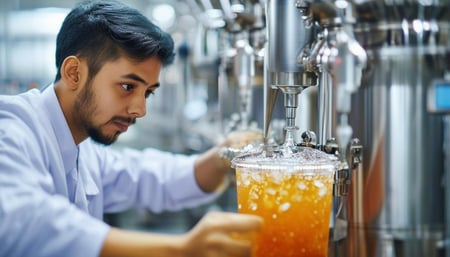
Reskilling: A Strategic Imperative
Reskilling, the process of training employees in new skills to fill emerging roles, has emerged as a strategic imperative for organizations grappling with workforce shortages. For production planners, reskilling offers a pathway to adapt to changing job requirements and leverage technology to enhance efficiency.
However, successful reskilling initiatives require a holistic approach that encompasses training, technology integration, and organizational support. Reskilling presents a proactive approach to address workforce shortages. Rather than solely relying on external hiring, companies can invest in training and upskilling their existing employees to fill critical roles. By identifying gaps in skill sets and providing targeted training programs, production planners can cultivate a versatile workforce capable of adapting to evolving demands.
Reskilling initiatives in food and beverage manufacturing are becoming increasingly essential as the industry faces evolving challenges such as technological advancements, changing consumer preferences, and workforce shortages.
Here are some notable examples of reskilling initiatives that companies in this sector have implemented:
Training Programs for Advanced Machinery Operation: Many food and beverage manufacturing companies are investing in training programs to equip their workforce with the skills required to operate advanced machinery and automated production lines. These programs often include hands-on training sessions, simulations, and certifications to ensure that employees are proficient in handling complex equipment safely and efficiently. By enhancing technical skills, companies can improve productivity, reduce downtime, and maintain high product quality standards.
Quality Control and Food Safety Training: Ensuring product quality and safety is paramount in the food and beverage industry. Reskilling initiatives often focus on providing employees with comprehensive training in quality control protocols, food safety regulations, and sanitation practices. By investing in continuous training and certification programs, companies can mitigate risks related to contamination, maintain compliance with industry standards, and safeguard their brand reputation.
Cross-Functional Training Programs: Cross-functional training programs are designed to empower employees with diverse skill sets and enable them to perform various roles within the organization. For example, production line workers may receive training in maintenance tasks, while maintenance technicians may undergo training in quality assurance procedures. By fostering a culture of versatility and adaptability, companies can optimize workforce flexibility, facilitate smoother transitions during staffing shortages, and improve overall operational resilience.
Digital Skills and Industry 4.0 Training: As the industry embraces digital transformation and Industry 4.0 technologies, reskilling initiatives are focusing on imparting digital literacy and technical skills to employees. Training programs may cover topics such as data analysis, automation technologies, Internet of Things (IoT), and robotics. By upskilling employees in emerging technologies, companies can enhance operational efficiency, reduce costs, and stay competitive in an increasingly digitized marketplace.
Leadership Development Programs: Leadership development programs are essential for cultivating the next generation of managers and supervisors in food and beverage manufacturing. These programs often include modules on effective communication, decision-making, conflict resolution, and strategic planning. By investing in leadership development, companies can foster a culture of innovation, empower employees to take ownership of their roles, and drive organizational growth and success.
Collaboration with Educational Institutions and Industry Partners: Some companies collaborate with educational institutions, industry associations, and government agencies to develop customized training programs tailored to the specific needs of the food and beverage manufacturing sector. These partnerships may involve curriculum development, apprenticeship programs, internships, and workforce development grants. By leveraging external expertise and resources, companies can access specialized training opportunities and ensure that their workforce remains competitive and up-to-date with industry trends and best practices.

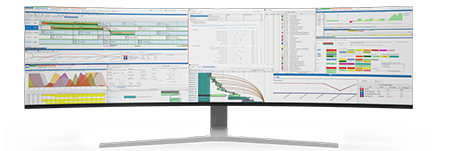
Integration of Advanced Planning Systems
Central to successful reskilling initiatives is the integration of advanced planning systems with enterprise resource planning (ERP) solutions. Platforms like PlanetTogether offer sophisticated tools for production planning and scheduling, enabling planners to optimize resources and minimize disruptions.
When seamlessly integrated with ERP systems such as SAP, Oracle, Microsoft Dynamics, Kinaxis RapidResponse, or Aveva MES, these solutions create a unified ecosystem where data flows seamlessly across departments, facilitating informed decision-making and efficient resource allocation.
Benefits of Integration
Real-time Data Visibility: Integration between advanced planning systems and ERP solutions provides production planners with real-time visibility into key metrics such as inventory levels, machine availability, and production schedules. This visibility enables proactive decision-making and ensures alignment between production plans and business objectives.
Automated Workflows: By automating workflows and data exchange processes, integration streamlines operations and reduces manual intervention. Production planners can leverage this automation to focus on strategic tasks such as capacity planning and scenario analysis, rather than getting bogged down by administrative tasks.
Optimized Resource Allocation: Integrated planning systems empower production planners to optimize resource allocation based on dynamic demand signals and production constraints. Whether it’s reallocating labor resources or adjusting production schedules in response to changing market conditions, planners can make data-driven decisions that maximize efficiency and minimize costs.
Enhanced Collaboration: Integration fosters collaboration across departments by providing a shared platform for communication and information exchange. Production planners can collaborate with other stakeholders, such as procurement, logistics, and maintenance, to ensure seamless execution of production plans and address potential bottlenecks proactively.
Continuous Improvement: By harnessing the power of data analytics and machine learning, integrated planning systems facilitate continuous improvement initiatives. Production planners can leverage historical data and predictive analytics to identify trends, forecast demand, and refine planning parameters, driving operational excellence and resilience.
Reskilling presents a viable solution for food and beverage manufacturers grappling with workforce shortages. By investing in employee development and integrating advanced planning and scheduling software like PlanetTogether with leading ERP systems, production planners can navigate the complexities of modern manufacturing environments with confidence.
By leveraging technology to streamline operations, optimize resource utilization, and enhance decision-making capabilities, organizations can not only overcome workforce shortages but also drive sustainable growth and innovation in the food and beverage industry.
Are you ready to take your manufacturing operations to the next level? Contact us today to learn more about how PlanetTogether and integrated scheduling solutions can help you achieve your sustainability goals and drive success in your industry.