Optimizing Supplier Risk Management
In today's interconnected global economy, effective supplier risk management is more critical than ever for packaging manufacturing facilities. Purchasing Managers play a pivotal role in ensuring that their organizations maintain a competitive edge while mitigating risks associated with their suppliers.
In this blog, we will explore the significance of supplier risk management and how integrating advanced planning and scheduling solutions like PlanetTogether with ERP, SCM, and MES systems can revolutionize your approach to mitigating supplier risks.
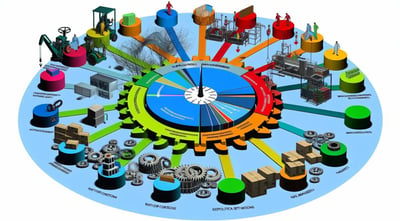
The Importance of Supplier Risk Management
Supplier risk management is the process of identifying, assessing, and mitigating the potential risks associated with your suppliers. These risks can range from supply chain disruptions, quality issues, price fluctuations, geopolitical events, and more. Effective supplier risk management helps in:
Maintaining Supply Chain Resilience: By identifying and addressing potential risks, you can reduce the impact of disruptions and maintain a resilient supply chain.
Cost Reduction: Proactive risk management can help you avoid costly supply chain interruptions, product recalls, or quality issues.
Enhancing Supplier Relationships: Open and transparent communication with suppliers fosters better relationships and collaborative problem-solving.
Regulatory Compliance: Ensuring that your suppliers meet regulatory requirements is crucial to avoid legal and reputational risks.
Strategic Decision-Making: Data-driven insights from supplier risk management can inform strategic decisions about supplier selection, sourcing strategies, and product development.

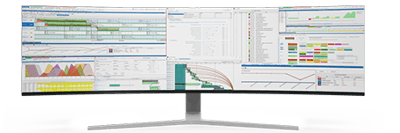
Integration Between PlanetTogether and ERP, SCM, MES Systems
To effectively manage supplier risks, you need real-time visibility into your supply chain operations and seamless collaboration across departments. This is where the integration of advanced planning and scheduling solutions like PlanetTogether with ERP, SCM, and MES systems becomes indispensable.
Integration with ERP Systems (SAP, Oracle, Microsoft)
-
-
Real-time Data Sharing: Integrating PlanetTogether with ERP systems allows for seamless data exchange, ensuring that all departments have access to the latest information.
-
Demand Forecasting: PlanetTogether can utilize historical data and real-time information from ERP systems to provide accurate demand forecasts, helping Purchasing Managers make informed decisions.
-
Inventory Optimization: By integrating with ERP systems, PlanetTogether can optimize inventory levels, reducing carrying costs and minimizing the risk of overstock or stockouts.
-
Purchase Order Automation: Automating purchase orders based on real-time demand data ensures that you maintain optimal stock levels while reducing manual intervention and errors.
Integration with SCM Systems (Kinaxis, Aveva, etc.)
-
End-to-End Visibility: Integrating PlanetTogether with SCM systems provides end-to-end visibility into your supply chain, enabling you to proactively identify and mitigate risks.
-
Collaborative Planning: Seamless collaboration between supply chain partners through integrated systems fosters effective risk management and responsive decision-making.
-
Scenario Analysis: PlanetTogether's advanced planning capabilities combined with SCM systems allow for scenario analysis, helping you evaluate the impact of various supply chain disruptions and make contingency plans.
Integration with MES Systems
-
Real-Time Production Data: Integration with MES systems ensures that PlanetTogether receives real-time production data, allowing for accurate scheduling and adjustment in case of disruptions.
-
Quality Control: MES systems can provide quality control data, which PlanetTogether can use to assess supplier quality and take corrective actions when necessary.
-
Traceability: The integration allows for end-to-end traceability, making it easier to track and manage products and materials through the supply chain.
-
Resource Optimization: MES data can be used to optimize resources and production schedules, reducing the risk of production delays.
Benefits of Integration for Supplier Risk Management
Proactive Risk Identification: Integration provides real-time data, enabling you to identify potential risks as they emerge and take immediate action.
Improved Communication: Seamless data exchange fosters better communication with suppliers, enhancing collaboration and risk mitigation efforts.
Data-Driven Decisions: Integrated systems enable data-driven decision-making, helping you prioritize and allocate resources to mitigate high-priority risks.
Supply Chain Resilience: By optimizing production schedules and inventory levels in real-time, you can enhance your supply chain's resilience and adaptability.
Reduced Manual Effort: Automation of tasks such as purchase order generation and production scheduling reduces the risk of human error and frees up time for strategic planning.
Competitive Advantage: An integrated approach to supplier risk management can give your packaging manufacturing facility a competitive advantage by reducing costs, improving quality, and ensuring on-time delivery.
In today's business environment, Purchasing Managers in packaging manufacturing facilities must prioritize supplier risk management to maintain competitiveness and resilience. Integrating advanced planning and scheduling solutions like PlanetTogether with ERP, SCM, and MES systems is the key to achieving effective and proactive risk mitigation.
By embracing integration, you can enhance your supply chain's visibility, optimize operations, and foster collaborative relationships with suppliers. Ultimately, this approach will help you navigate the complex landscape of supplier risks and position your organization for long-term success in the packaging manufacturing industry.
Are you ready to take your manufacturing operations to the next level? Contact us today to learn more about how PlanetTogether can help you achieve your goals and drive success in your industry.
LEAVE A COMMENT