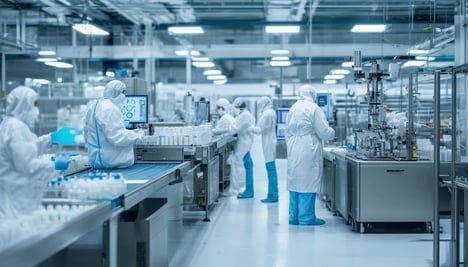
Optimizing Resource Allocation in Pharmaceutical Manufacturing
Efficient resource allocation can significantly impact production schedules, compliance, and profitability. For production schedulers, the complexity of balancing labor, equipment, materials, and timelines is compounded by stringent regulatory requirements and market demand for high-quality, life-saving products.
Leveraging advanced tools like PlanetTogether, integrated with enterprise systems such as SAP, Oracle, Microsoft, Kinaxis, or Aveva, can revolutionize resource allocation and optimize production workflows.
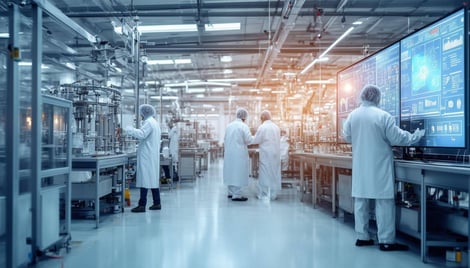
Resource Allocation in Pharmaceutical Manufacturing
Pharmaceutical production schedulers face numerous challenges, including:
Regulatory Compliance: Adhering to Good Manufacturing Practices (GMP) and FDA requirements necessitates meticulous planning and documentation.
Complex Production Processes: Multiple stages of manufacturing—from formulation and mixing to packaging—require precise coordination.
Resource Constraints: Limited availability of skilled labor, specialized equipment, and critical materials can disrupt schedules.
Demand Fluctuations: Sudden changes in market demand for specific drugs or vaccines require agile adjustments.
Downtime Risks: Equipment maintenance, changeovers, and unforeseen breakdowns can delay production.
Optimizing resource allocation in this environment demands sophisticated scheduling tools and seamless data integration across departments.

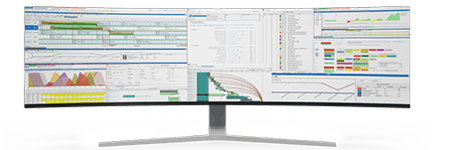
The Role of Advanced Scheduling Tools
Traditional spreadsheets and manual scheduling methods are often inadequate for handling the complexity of pharmaceutical manufacturing. Advanced scheduling software like PlanetTogether provides production schedulers with tools to:
Visualize Schedules: Intuitive dashboards display real-time data, helping schedulers identify bottlenecks and optimize workflows.
Automate Decisions: Algorithms suggest the most efficient resource allocations based on constraints and priorities.
Scenario Planning: Simulations allow schedulers to test "what-if" scenarios and prepare for contingencies.
Monitor Performance: KPIs and analytics provide insights into production efficiency and resource utilization.
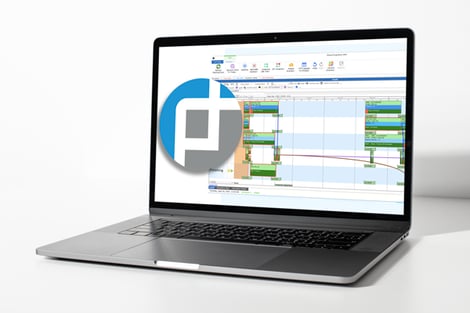
Integrating PlanetTogether with Enterprise Systems
Integration between PlanetTogether and enterprise systems such as SAP, Oracle, Microsoft Dynamics, Kinaxis, or Aveva amplifies the value of advanced scheduling. This interconnected ecosystem ensures that data flows seamlessly across platforms, enabling better decision-making and resource optimization.
Benefits of Integration
Real-Time Data Sharing: Integration ensures that production schedules are based on the most up-to-date information, including inventory levels, equipment availability, and order priorities.
Enhanced Collaboration: Cross-functional teams can access a unified platform, fostering collaboration between production, procurement, and quality assurance teams.
Proactive Issue Resolution: Early warnings about potential delays or resource conflicts enable swift corrective actions.
Improved Forecasting: Demand forecasts from systems like Kinaxis can inform scheduling decisions, ensuring alignment with market needs.
Regulatory Compliance: Integration streamlines documentation and audit trails, supporting compliance with GMP and other regulations.
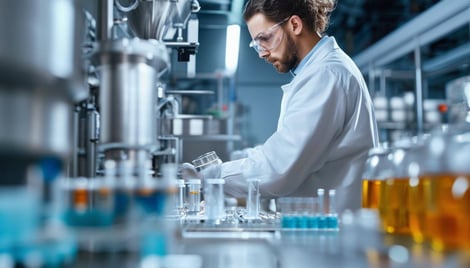
Best Practices for Optimizing Resource Allocation
Prioritize Critical Resources
Identify and prioritize the resources that are most critical to production. For example, a sterile filling line might be a bottleneck in vaccine production. Use scheduling tools to ensure these resources are utilized efficiently, minimizing idle time and maximizing throughput.
Leverage Predictive Analytics
Predictive maintenance and analytics—powered by integration with platforms like Aveva—can reduce equipment downtime. PlanetTogether’s integration capabilities can pull maintenance schedules and predict when equipment is likely to fail, allowing schedulers to adjust production plans proactively.
Balance Labor and Automation
Effective resource allocation requires balancing human labor with automated systems. PlanetTogether, integrated with Microsoft Dynamics, can provide insights into labor availability and skill sets, ensuring that the right people are assigned to the right tasks.
Minimize Changeovers
Frequent equipment changeovers can reduce productivity and increase costs. Advanced scheduling software can group similar production orders to minimize changeovers, ensuring smoother transitions and better resource utilization.
Implement Just-In-Time Scheduling
Integrate scheduling software with ERP systems like SAP or Oracle to implement just-in-time (JIT) scheduling. This approach reduces inventory holding costs and ensures that materials and resources are available exactly when needed.
Use Scenario Planning
PlanetTogether’s scenario planning features allow schedulers to simulate different resource allocation strategies. For example, if a critical supplier faces a delay, schedulers can test alternative sourcing options or production sequences to mitigate disruptions.
Optimizing resource allocation is critical for production schedulers in pharmaceutical manufacturing. Advanced tools like PlanetTogether, when integrated with systems such as SAP, Oracle, Microsoft, Kinaxis, or Aveva, provide the insights and automation needed to navigate complex production environments.
By embracing these technologies and following best practices, schedulers can enhance efficiency, ensure regulatory compliance, and meet market demands effectively. The result is a streamlined manufacturing process that delivers high-quality pharmaceutical products to patients on time and within budget.
Are you ready to take your manufacturing operations to the next level? Contact us today to learn more about how PlanetTogether can help you achieve your goals and drive success in your industry.