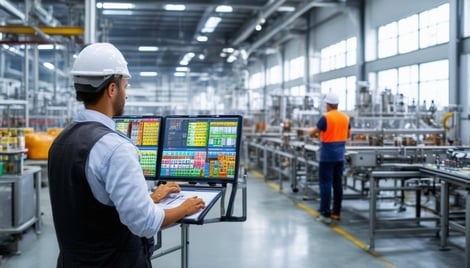
Optimizing Resource Allocation in Food and Beverage Manufacturing with Integrated Scheduling Tools
Efficient resource allocation is the cornerstone of success in food and beverage manufacturing. With razor-thin margins, fluctuating demand, and strict quality standards, Production Schedulers face the challenge of balancing productivity, compliance, and cost efficiency.
Leveraging advanced scheduling software like PlanetTogether, integrated with enterprise resource planning (ERP) systems such as SAP, Oracle, Microsoft Dynamics, Kinaxis, or Aveva, can revolutionize how resources are allocated to achieve operational excellence.
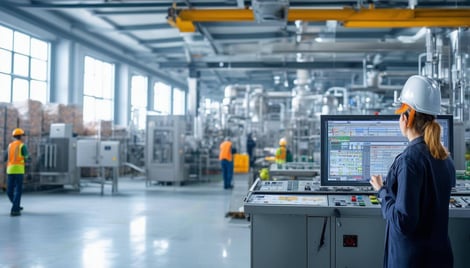
The Importance of Resource Allocation in Food and Beverage Manufacturing
Resource allocation involves the strategic distribution of labor, machinery, raw materials, and time to ensure seamless production processes. In the food and beverage industry, resource allocation is particularly critical due to:
Perishability of raw materials: Managing inventory levels to avoid waste while meeting production schedules.
Regulatory compliance: Ensuring production adheres to food safety standards and traceability requirements.
Demand variability: Rapidly adjusting to seasonal trends, promotions, and sudden market changes.
Complex supply chains: Coordinating multiple suppliers and distribution channels to avoid bottlenecks.
Challenges Faced by Production Schedulers
Production Schedulers must navigate a labyrinth of challenges, including:
Dynamic demand forecasts: Anticipating changes in order volumes and adjusting production schedules accordingly.
Equipment downtime: Minimizing disruptions due to maintenance or unexpected breakdowns.
Labor management: Allocating skilled workers across shifts to meet production goals.
Regulatory constraints: Ensuring compliance with industry standards without sacrificing efficiency.
Data silos: Struggling with fragmented data sources that hinder decision-making.

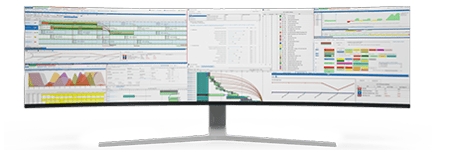
The Role of Advanced Scheduling Tools
Integrating advanced scheduling tools like PlanetTogether with ERP systems provides a robust solution to these challenges. These tools offer:
Real-time visibility: A unified view of resources, enabling dynamic adjustments to schedules.
Predictive analytics: Forecasting demand and identifying potential bottlenecks before they occur.
Scenario planning: Testing different scheduling strategies to find the optimal resource allocation.
Automation: Reducing manual intervention and errors through automated scheduling processes.
Collaboration: Facilitating communication between departments to align production goals with supply chain strategies.
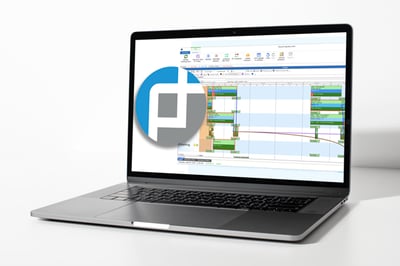
Integration of PlanetTogether with ERP Systems
To fully harness the benefits of advanced scheduling, integration with ERP systems is essential. Let’s explore how PlanetTogether integrates with popular ERP solutions to optimize resource allocation:
SAP Integration
SAP’s comprehensive ERP platform is widely used in the food and beverage industry. Integrating PlanetTogether with SAP provides:
Streamlined workflows: Automatic updates between production schedules and inventory levels.
Enhanced traceability: Real-time tracking of raw materials and finished goods.
Optimized procurement: Aligning purchase orders with production schedules to avoid overstocking or stockouts.
Oracle Integration
Oracle’s ERP solutions are known for their robust analytics and reporting capabilities. Integration with PlanetTogether enables:
Data-driven decisions: Combining Oracle’s analytics with PlanetTogether’s scheduling to improve efficiency.
Resource utilization insights: Identifying underutilized assets and reallocating them to high-demand areas.
Improved compliance: Ensuring production schedules align with regulatory requirements.
Microsoft Dynamics Integration
Microsoft Dynamics offers flexible ERP solutions ideal for mid-sized food and beverage manufacturers. Integration with PlanetTogether delivers:
Scalable solutions: Seamlessly adjusting to production volume changes.
Collaboration tools: Leveraging Microsoft Teams for better communication among schedulers, procurement, and operations teams.
Enhanced reporting: Combining Dynamics’ reports with PlanetTogether’s analytics for actionable insights.
Kinaxis Integration
Kinaxis specializes in supply chain optimization, making it a perfect partner for PlanetTogether. Together, they offer:
End-to-end visibility: Bridging the gap between supply chain planning and production scheduling.
Risk mitigation: Quickly identifying and addressing disruptions in the supply chain.
Scenario modeling: Evaluating different supply chain strategies to optimize resource allocation.
Aveva Integration
Aveva focuses on industrial software, particularly for process industries like food and beverage. Integration with PlanetTogether enables:
Process optimization: Aligning production schedules with manufacturing processes for minimal waste.
Energy efficiency: Scheduling operations to reduce energy consumption during peak hours.
Predictive maintenance: Using Aveva’s analytics to schedule maintenance during low-demand periods.
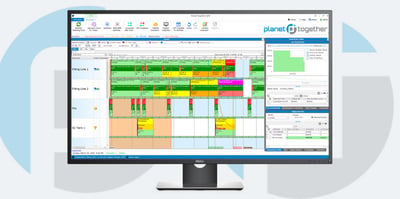
Key Benefits of Integration
The integration of PlanetTogether with ERP systems transforms resource allocation by:
Reducing waste: Optimized schedules minimize overproduction and raw material spoilage.
Increasing throughput: Efficient use of labor and machinery boosts production capacity.
Improving flexibility: Quickly adapting to market changes without disrupting production.
Enhancing visibility: Real-time data ensures informed decision-making.
Lowering costs: Streamlined operations reduce overhead and operational expenses.
Optimizing resource allocation is no longer a luxury but a necessity for food and beverage manufacturers striving to remain competitive. By integrating PlanetTogether with ERP systems like SAP, Oracle, Microsoft Dynamics, Kinaxis, or Aveva, Production Schedulers can achieve unprecedented efficiency, flexibility, and cost savings. Embracing these technologies not only improves operational performance but also positions manufacturers for long-term success in a dynamic industry.
The journey to optimized resource allocation begins with the right tools and strategies. Are you ready to take your manufacturing operations to the next level? Contact us today to learn more about how PlanetTogether can help you achieve your goals and drive success in your industry.
LEAVE A COMMENT