Production Layout in Packaging Manufacturing
As a Production Scheduler, you understand the critical importance of optimizing every aspect of the production process to meet deadlines, reduce costs, and enhance overall productivity. One area that often holds significant potential for improvement is the production layout.
In this blog, we'll look into the strategies and tools available to help you optimize your production layout for maximum efficiency, with a particular focus on integration between PlanetTogether and leading ERP, SCM, and MES systems like SAP, Oracle, Microsoft, Kinaxis, and Aveva.
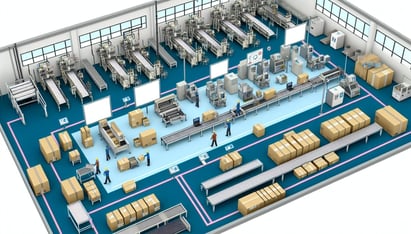
The Importance of Production Layout Optimization
The layout of your production facility plays a pivotal role in determining how smoothly operations run. A well-designed layout can minimize material handling, reduce bottlenecks, decrease cycle times, and ultimately boost throughput. On the other hand, a poorly optimized layout can lead to inefficiencies, increased lead times, and higher operating costs.
Challenges in Production Layout Optimization
Before we look into solutions, let's address some common challenges faced by Production Schedulers when it comes to optimizing production layouts:
Limited Space: Many manufacturing facilities face constraints when it comes to available space, making it challenging to design an optimal layout.
Changing Demand: Fluctuations in customer demand require production layouts to be adaptable and flexible to accommodate varying production volumes and product mix.
Complexity: Modern packaging manufacturing involves numerous production processes, equipment, and workflows, adding complexity to the task of designing an efficient layout.
Resource Allocation: Efficient allocation of resources, including machinery, manpower, and materials, is essential for maximizing productivity and minimizing idle time.
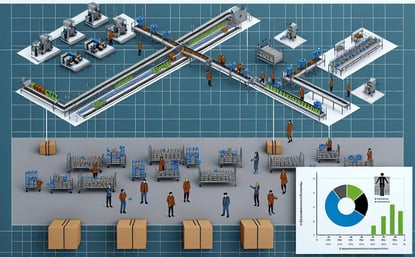
Strategies for Production Layout Optimization
Now, let's explore some strategies for optimizing your production layout:
Value Stream Mapping (VSM): Conduct a thorough analysis of your current production processes using VSM to identify areas of waste, bottlenecks, and inefficiencies. This visual representation will serve as a roadmap for redesigning your layout.
Workflow Optimization: Streamline workflow sequences to minimize material handling and transportation time. Grouping machines and workstations based on process flow can help reduce unnecessary movement and improve overall efficiency.
Zone Control: Divide your production floor into distinct zones based on product families, production volumes, or process requirements. This segmentation allows for better organization, faster changeovers, and improved resource utilization.
Utilization of Space: Make the most out of your available space by optimizing aisle widths, storage locations, and equipment placement. Implementing vertical storage solutions and maximizing floor space utilization can help alleviate space constraints.
Simulation and Modeling: Leverage advanced simulation software like PlanetTogether to create digital models of your production layout. By simulating different scenarios and configurations, you can identify the most efficient layout design before implementing changes on the shop floor.

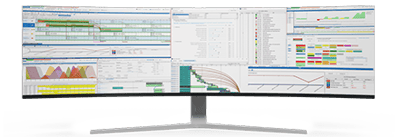
Integration with ERP, SCM, and MES Systems
Now, let's discuss how integration between production scheduling software like PlanetTogether and leading ERP, SCM, and MES systems can further enhance the optimization of your production layout:
Data Synchronization: Seamless integration allows for real-time synchronization of data between production scheduling software and ERP systems like SAP, Oracle, and Microsoft Dynamics. This ensures that production plans are aligned with customer orders, inventory levels, and resource availability.
Demand Forecasting: Integration with SCM systems enables more accurate demand forecasting based on historical data, market trends, and customer insights. This allows Production Schedulers to proactively adjust production layouts to accommodate forecasted demand fluctuations.
Resource Allocation: MES integration provides visibility into machine utilization, downtime, and overall equipment effectiveness (OEE). By analyzing this data in conjunction with production schedules, Production Schedulers can optimize resource allocation and minimize idle time.
Order Prioritization: Integrated systems enable dynamic order prioritization based on customer deadlines, order quantities, and production constraints. This ensures that high-priority orders are given precedence in scheduling and layout optimization.
Continuous Improvement: Integration facilitates the implementation of continuous improvement initiatives by providing a holistic view of production performance metrics, including throughput, cycle times, and lead times. This allows Production Schedulers to identify areas for improvement and make data-driven decisions to optimize the production layout further.
Optimizing the production layout is essential for maximizing efficiency and competitiveness in the packaging manufacturing industry. By employing strategies such as value stream mapping, workflow optimization, and space utilization, Production Schedulers can streamline operations and minimize waste. Furthermore, integration between production scheduling software and ERP, SCM, and MES systems enhances visibility, agility, and decision-making capabilities, enabling continuous improvement and adaptation to changing market conditions.
Embracing these approaches will not only drive operational excellence but also position your organization for long-term success in today's dynamic business environment. Are you ready to take your manufacturing operations to the next level? Contact us today to learn more about how PlanetTogether can help you achieve your goals and drive success in your industry.
LEAVE A COMMENT