Production Costs in Chemical Manufacturing
In the competitive and complex world of chemical manufacturing, production cost optimization isn't just a strategic advantage—it's a necessity. The volatile nature of raw material prices, the stringent regulatory environment, and the ever-present pressure to reduce environmental impact all play a significant role in the daily operations of a chemical facility.
For Supply Chain Managers, navigating these challenges requires not only keen industry insight but also robust technological tools.
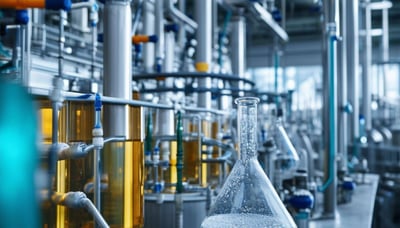
The Landscape of Production Costs
Before looking into the technical solutions, it's crucial to understand the various components that contribute to production costs in chemical manufacturing. These typically include:
- Raw Material Costs: Often the most significant expense, affected by global supply chains and market dynamics.
- Energy Consumption: Chemical processes are energy-intensive, and optimizing energy use is vital for cost reduction and environmental sustainability.
- Labor Costs: Efficiency and productivity of labor can significantly influence total production costs.
- Maintenance and Downtime: Preventive maintenance and minimizing downtime are essential for cost-effective operations.
- Compliance and Safety: Adhering to regulations and ensuring safety in handling chemicals are critical, which also incur costs.
Addressing these cost factors effectively demands a sophisticated approach to planning, scheduling, and executing production processes. This is where the integration of advanced planning and scheduling (APS) systems like PlanetTogether with enterprise resource planning (ERP), supply chain management (SCM), and manufacturing execution systems (MES) becomes critical.
-Apr-01-2024-01-39-55-8668-PM.png?width=300&height=48&name=logo%20(2)-Apr-01-2024-01-39-55-8668-PM.png)
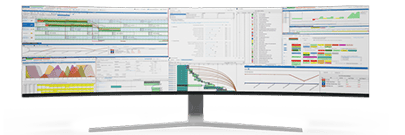
The Role of PlanetTogether in Cost Optimization
PlanetTogether is a powerful APS solution that is designed to enhance production efficiency and optimize resource use in manufacturing environments, including the chemical sector. It offers features such as multi-plant planning, detailed scheduling, and scenario simulation, which are indispensable for Supply Chain Managers aiming to reduce costs and improve throughput.
Key Features of PlanetTogether
- Advanced Scheduling: Allows for precise scheduling of machine and labor resources to reduce downtime and increase output.
- Capacity Planning: Helps in identifying bottlenecks and predicting capacity constraints before they cause issues.
- What-if Scenarios: Enables managers to simulate various production scenarios to find the most cost-effective strategies.
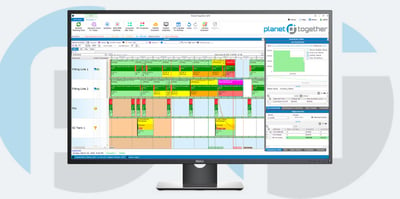
Integration with ERP, SCM, and MES Systems
Integrating PlanetTogether with various ERP, SCM, and MES systems magnifies its effectiveness by ensuring that data flows seamlessly across all platforms, enhancing decision-making and operational efficiency. Let’s explore how this integration works with popular systems like SAP, Oracle, Microsoft, Kinaxis, Aveva, and others.
Integration with SAP
SAP, one of the leading ERP systems, is extensively used in chemical manufacturing for its robust capabilities in managing financials, human resources, and operations. Integrating PlanetTogether with SAP allows real-time data exchange between the APS and ERP systems, ensuring that production schedules are based on the latest business data. This integration helps in minimizing inventory costs and production delays by aligning production schedules with demand forecasts and supply constraints.
Integration with Oracle
Oracle’s ERP solutions offer comprehensive features that support large-scale manufacturing operations. By integrating with Oracle, PlanetTogether can leverage detailed insights into procurement, supply chain management, and financial operations, thus optimizing the entire production schedule to meet business objectives while reducing costs.
Integration with Microsoft
Microsoft’s Dynamics 365 brings together CRM and ERP capabilities along with additional applications that run business processes. PlanetTogether’s integration with Microsoft Dynamics 365 can streamline operations from sales to production, ensuring that the manufacturing schedules are closely aligned with customer demands and delivery schedules, which helps in reducing holding costs and improving customer satisfaction.
Integration with Kinaxis
Kinaxis RapidResponse is a supply chain management software that provides end-to-end visibility and unparalleled agility in operations. Integrating it with PlanetTogether enhances the ability to respond to supply chain disruptions by adjusting production plans in real-time, thus minimizing the impact of disruptions on costs and service levels.
Integration with Aveva
Aveva's software focuses on industrial and engineering software solutions, making it particularly valuable in the chemical sector. Integration with Aveva allows chemical manufacturers to align their production planning with detailed engineering insights, thereby optimizing the use of resources and minimizing waste during production processes.
For Supply Chain Managers in the chemical manufacturing industry, optimizing production costs is not merely about cutting corners but improving efficiencies and leveraging technology to make informed, strategic decisions. Integrating advanced planning systems like PlanetTogether with ERP, SCM, and MES systems provides a comprehensive view of the supply chain and production processes, leading to significant cost reductions and enhanced competitive advantage.
By staying at the forefront of technology integration and leveraging data-driven insights, Supply Chain Managers can not only meet the current demands of the industry but also prepare for future challenges in an ever-evolving marketplace.
Are you ready to take your manufacturing operations to the next level? Contact us today to learn more about how PlanetTogether can help you achieve your goals and drive success in your industry.
LEAVE A COMMENT