Optimizing Manufacturing Equipment Lifecycle Management
To stay ahead in the competitive landscape, companies must constantly seek innovative solutions to streamline their operations. One area where optimization can yield significant benefits is in the management of manufacturing equipment lifecycles. From acquisition to decommissioning, every stage of a machine's lifecycle presents opportunities for improvement.
In this blog, we will look into the importance of effective equipment lifecycle management and explore how integration between PlanetTogether and leading ERP, SCM, and MES systems can revolutionize the process.
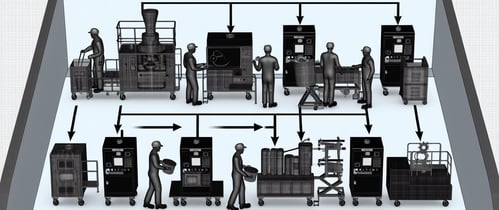
Understanding Equipment Lifecycle Management
Manufacturing equipment lifecycle management encompasses a series of stages, each with its own set of challenges and considerations. These stages typically include:
Acquisition: The initial procurement of machinery involves careful evaluation of requirements, vendor selection, and negotiation of contracts. It's crucial to choose equipment that aligns with production needs and long-term business goals.
Installation and Commissioning: Once acquired, machines need to be installed, configured, and integrated into existing production lines. This phase requires meticulous planning to minimize downtime and ensure smooth operation.
Operation and Maintenance: During the operational phase, regular maintenance is essential to prevent breakdowns and optimize performance. Monitoring equipment health in real-time can help identify issues before they escalate, reducing unplanned downtime.
Upgrades and Modifications: As technology advances and business needs evolve, manufacturing equipment may require upgrades or modifications to enhance functionality or efficiency. Implementing these changes seamlessly is critical to maintaining productivity.
Decommissioning: Eventually, equipment reaches the end of its useful life and must be decommissioned responsibly. Proper disposal or recycling practices minimize environmental impact while maximizing return on investment.
Challenges in Equipment Lifecycle Management
Despite its importance, managing equipment lifecycles effectively poses several challenges for packaging manufacturers:
Data Silos: Information about equipment status, maintenance history, and performance metrics is often scattered across disparate systems, making it difficult to gain comprehensive insights.
Manual Processes: Many companies still rely on manual methods for tracking equipment lifecycles, leading to inefficiencies, errors, and delays.
Lack of Integration: Incompatibility between software platforms used for production planning, inventory management, and maintenance tracking hinders seamless data exchange and collaboration.
Reactive Maintenance: Waiting for equipment to fail before taking action can result in costly downtime and production delays, impacting overall operational efficiency.
Compliance and Regulation: Packaging manufacturers must adhere to stringent regulations regarding equipment safety, environmental impact, and product quality throughout the lifecycle, adding complexity to management processes.
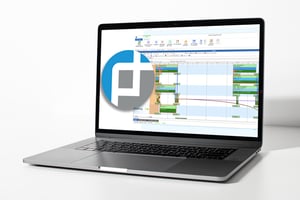
Integration Solutions for Enhanced Lifecycle Management
To overcome these challenges and optimize equipment lifecycle management, packaging manufacturers can leverage integration solutions that connect manufacturing execution systems (MES), enterprise resource planning (ERP), and supply chain management (SCM) platforms with advanced production planning tools like PlanetTogether.
By integrating these systems, companies can achieve:
Real-time Visibility: Integration enables seamless data flow between different stages of the equipment lifecycle, providing stakeholders with real-time visibility into equipment status, maintenance schedules, and performance metrics.
Predictive Maintenance: By analyzing historical data and machine learning algorithms, integrated systems can predict equipment failures before they occur, allowing for proactive maintenance and minimizing unplanned downtime.
Streamlined Workflows: Automated workflows and alerts facilitate smoother collaboration between production, maintenance, and procurement teams, reducing manual effort and improving response times.
Compliance Management: Integrated systems can ensure compliance with regulatory requirements by tracking documentation, audit trails, and maintenance records throughout the equipment lifecycle.
Optimization Opportunities: By analyzing data from integrated systems, manufacturers can identify optimization opportunities such as equipment upgrades, process improvements, and resource reallocation to enhance overall efficiency and profitability.
-May-08-2024-04-36-12-8483-PM.png?width=313&height=50&name=logo%20(2)-May-08-2024-04-36-12-8483-PM.png)
Integration between PlanetTogether and SAP ERP
Let's consider a hypothetical scenario where a packaging manufacturer integrates PlanetTogether, a leading production planning tool, with SAP ERP, a widely used enterprise resource planning platform. By connecting these systems, the company gains several benefits:
Seamless Data Exchange: Production orders, inventory levels, and material requirements are synchronized between PlanetTogether and SAP ERP in real-time, eliminating data silos and ensuring accurate planning.
Enhanced Production Planning: PlanetTogether's advanced algorithms optimize production schedules based on SAP ERP data, considering factors such as equipment availability, capacity constraints, and resource utilization.
Predictive Maintenance: By analyzing historical maintenance data from SAP ERP, PlanetTogether can predict equipment failures and incorporate maintenance activities into production schedules to minimize downtime.
Inventory Optimization: Integrated systems enable better inventory management by synchronizing material requirements with procurement and warehouse operations in SAP ERP, reducing stockouts and excess inventory.
Continuous Improvement: Data from both PlanetTogether and SAP ERP can be analyzed to identify trends, bottlenecks, and opportunities for process optimization, driving continuous improvement initiatives.
Effective equipment lifecycle management is essential for packaging manufacturers seeking to optimize efficiency, minimize downtime, and stay compliant with regulations. By integrating advanced production planning tools like PlanetTogether with leading ERP, SCM, and MES systems, companies can overcome challenges associated with data silos, manual processes, and reactive maintenance.
The result is a streamlined, interconnected ecosystem that provides real-time visibility, enables predictive maintenance, and unlocks optimization opportunities throughout the equipment lifecycle.
Embracing integration is not just a competitive advantage; it's a strategic imperative for packaging manufacturers looking to thrive in the digital era. Are you ready to take your manufacturing operations to the next level? Contact us today to learn more about how PlanetTogether can help you achieve your goals and drive success in your industry.