Welcome to a deep dive into the intricate world of Life Sciences production scheduling. We'll explore how advanced planning and scheduling software, specifically PlanetTogether, revolutionizes the management of shelf life constraints, ensuring efficiency and compliance in pharmaceutical manufacturing.
Understanding Shelf Life Constraints:
Shelf life constraints are a critical consideration in pharmaceutical manufacturing, where product quality and compliance are paramount. Let's dissect how PlanetTogether tackles this challenge with precision and finesse.
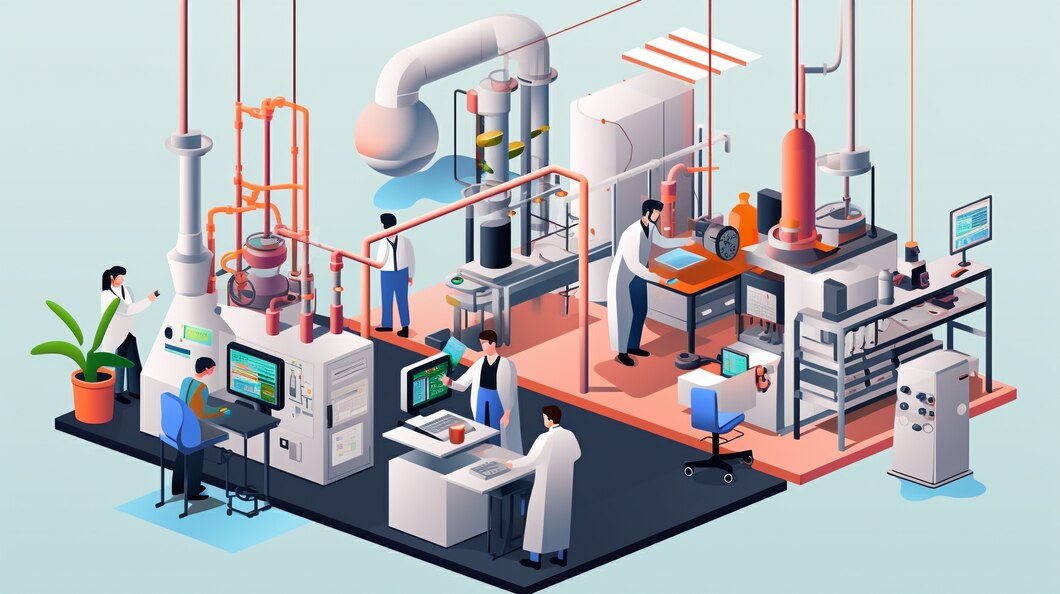
In our exploration, we'll navigate through simulated scenarios to understand the nuances of shelf life management facilitated by PlanetTogether's advanced algorithms. Here's a closer look at the process:
Implementation of Shelf Life Property:
PlanetTogether empowers users to define shelf life parameters for materials, setting time-bound thresholds for usability. By configuring this property, materials are effectively managed within their designated shelf life, minimizing the risk of product degradation.
Timely Material Consumption:
Through strategic scheduling and optimization, PlanetTogether ensures that materials are consumed within their shelf life window. By synchronizing production activities with material expiration dates, the software minimizes wastage and maintains product integrity.
Efficient Resource Utilization:
Optimizing resource allocation is key to mitigating shelf life violations. PlanetTogether intelligently schedules production activities to maximize resource utilization while adhering to shelf life constraints, thereby minimizing bottlenecks and enhancing operational efficiency.
Case Study:
Let's delve into a practical example to illustrate PlanetTogether's efficacy in managing shelf life constraints:
ShelfJob01: This operation exemplifies the seamless execution of shelf life constraints. By scheduling material consumption within the stipulated timeframe, PlanetTogether ensures optimal production flow while upholding compliance standards.
ShelfJob04: Despite encountering partial material consumption, PlanetTogether dynamically adjusts schedules to prevent wastage and minimize shelf life violations. This adaptive approach underscores the software's versatility in addressing real-world production challenges.
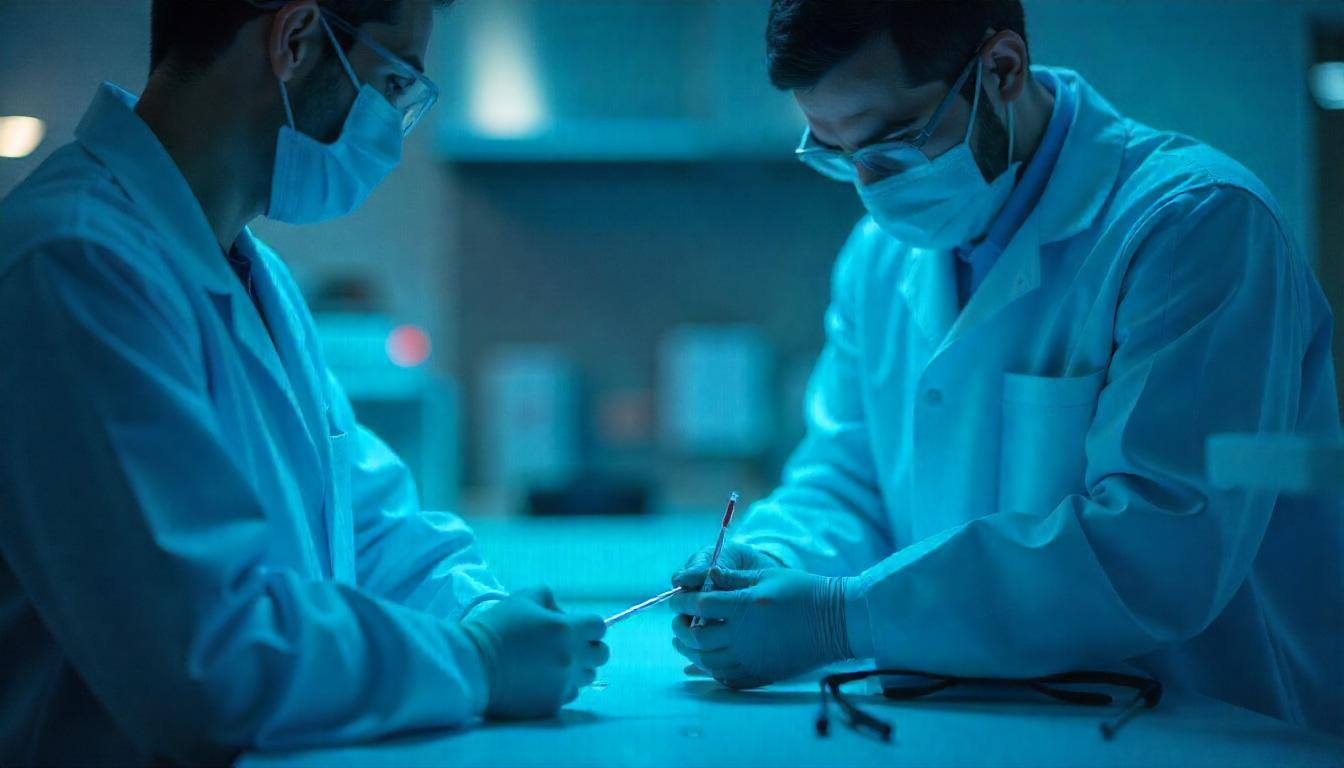
Ensuring Quality and Compliance: Advisories for Effective Shelf Life Management in Life Sciences
Advisories for Success:
Leverage Advanced Planning and Scheduling Software:
Invest in robust software solutions like PlanetTogether to streamline production scheduling and optimize resource allocation. By harnessing advanced algorithms and intuitive interfaces, these tools empower organizations to effectively manage shelf life constraints while enhancing operational efficiency.
Define Clear Shelf Life Parameters:
Establish clear parameters for shelf life constraints based on product specifications and regulatory requirements. Define expiration thresholds for materials and integrate them into production scheduling processes to minimize wastage and maintain product integrity.
Implement Real-Time Monitoring and Analytics:
Embrace real-time monitoring and analytics capabilities to track material consumption, production progress, and shelf life expiration. By leveraging data-driven insights, organizations can proactively identify potential shelf life violations and implement corrective measures in a timely manner.
Foster Cross-Functional Collaboration:
Promote collaboration and communication across departments involved in production scheduling, inventory management, and quality assurance. Foster alignment on shelf life considerations and ensure that all stakeholders are actively engaged in mitigating risks and optimizing processes.
Continuously Evaluate and Adapt:
Adopt a culture of continuous improvement by regularly evaluating production processes and identifying opportunities for optimization. Stay abreast of industry trends, technological advancements, and regulatory updates to adapt strategies and ensure ongoing compliance and competitiveness.
Watch the video below for a demo: