Optimizing Global Manufacturing Scheduling: A Guide to Risk Mitigation
Manufacturing operations are subject to numerous uncertainties and risks. From supply chain disruptions to fluctuating demand and regulatory changes, the modern Operations Director faces a multitude of challenges in ensuring efficient and reliable production schedules. Amidst these complexities, the integration of advanced scheduling solutions like PlanetTogether with Enterprise Resource Planning (ERP), Supply Chain Management (SCM), and Manufacturing Execution Systems (MES) becomes imperative for effective risk mitigation.
In this blog, we look into the strategies and tools that Operations Directors can leverage to optimize global manufacturing scheduling and mitigate risks effectively.
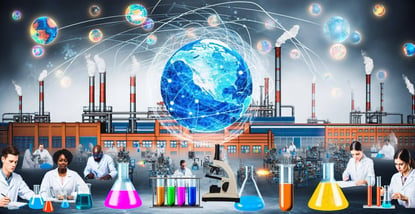
Understanding the Landscape of Global Manufacturing
The landscape of global manufacturing is characterized by its intricate web of interconnected processes, suppliers, and markets. Operations Directors must navigate through diverse challenges such as:
Supply Chain Disruptions: Events like natural disasters, geopolitical tensions, and pandemics can disrupt the flow of raw materials and components, leading to production delays and increased costs.
Fluctuating Demand: Rapid shifts in consumer preferences, market trends, and economic conditions can result in unpredictable demand patterns, challenging traditional forecasting methods.
Regulatory Compliance: Stringent regulations pertaining to environmental standards, safety protocols, and product quality impose additional constraints on manufacturing operations, necessitating proactive compliance measures.
Resource Optimization: Efficient utilization of resources, including machinery, labor, and energy, is essential for maximizing productivity while minimizing costs and environmental impact.
-May-08-2024-04-36-12-8483-PM.png?width=300&height=48&name=logo%20(2)-May-08-2024-04-36-12-8483-PM.png)
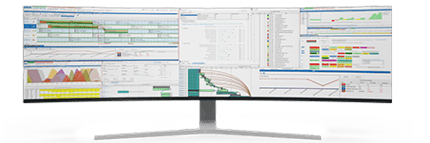
Integrating PlanetTogether with ERP, SCM, and MES Systems
To address these challenges and enhance operational resilience, Operations Directors can leverage the integration capabilities of advanced scheduling software like PlanetTogether with leading ERP, SCM, and MES systems. By seamlessly connecting these platforms, organizations can achieve the following benefits:
Real-Time Data Synchronization: Integrating PlanetTogether with ERP systems such as SAP, Oracle, or Microsoft Dynamics enables real-time synchronization of production plans, inventory levels, and resource availability. This ensures accurate decision-making and enhances agility in response to changing market conditions.
Enhanced Visibility and Collaboration: By integrating PlanetTogether with SCM systems like Kinaxis or Aveva, Operations Directors can gain end-to-end visibility across the supply chain, from raw material procurement to product delivery. This facilitates collaboration with suppliers, distributors, and other stakeholders, enabling proactive risk management and optimized inventory management.
Streamlined Production Execution: Integration with MES systems allows for seamless execution of production schedules, monitoring of key performance indicators (KPIs), and real-time tracking of production activities. This ensures compliance with quality standards, improves operational efficiency, and reduces lead times.
Predictive Analytics and Optimization: Leveraging advanced analytics capabilities within integrated platforms, Operations Directors can harness the power of predictive modeling and optimization algorithms to anticipate potential risks, simulate various scenarios, and optimize production schedules accordingly. This proactive approach minimizes disruptions and maximizes resource utilization, leading to improved profitability and customer satisfaction.
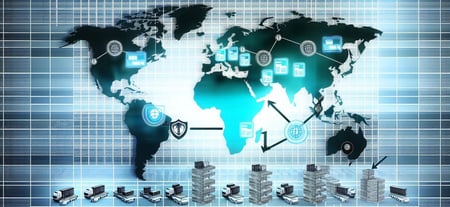
Best Practices for Risk Mitigation in Global Manufacturing Scheduling
In addition to leveraging integrated scheduling solutions, Operations Directors can implement the following best practices to mitigate risks effectively:
Scenario Planning: Develop contingency plans and scenario models to assess the impact of various risk factors on production schedules, such as supplier delays, capacity constraints, or market fluctuations. By simulating different scenarios and evaluating their respective outcomes, organizations can proactively identify vulnerabilities and devise mitigation strategies.
Cross-Functional Collaboration: Foster collaboration and communication among cross-functional teams, including operations, procurement, logistics, and sales. By aligning objectives and sharing insights, organizations can improve decision-making, anticipate potential bottlenecks, and expedite problem resolution.
Continuous Improvement: Embrace a culture of continuous improvement by monitoring key performance metrics, conducting root cause analysis of deviations, and implementing corrective actions. By systematically identifying areas for optimization and implementing process enhancements, organizations can enhance operational efficiency and resilience over time.
Invest in Employee Training and Development: Equip employees with the necessary skills and knowledge to leverage advanced scheduling tools effectively. Provide comprehensive training programs and professional development opportunities to ensure that staff members are proficient in utilizing integrated systems and interpreting analytics insights.
Effective risk mitigation in global manufacturing scheduling requires a proactive and holistic approach, leveraging advanced technologies, integrated platforms, and best practices. By integrating scheduling solutions like PlanetTogether with ERP, SCM, and MES systems, Operations Directors can enhance operational resilience, optimize resource utilization, and improve decision-making agility.
Moreover, by embracing best practices such as scenario planning, cross-functional collaboration, continuous improvement, and employee development, organizations can navigate through uncertainties and emerge stronger in today's competitive landscape.
Embracing innovation and leveraging data-driven insights will be essential for driving sustainable growth and mitigating risks effectively. Are you ready to take your manufacturing operations to the next level? Contact us today to learn more about how PlanetTogether can help you achieve your goals and drive success in your industry.
LEAVE A COMMENT