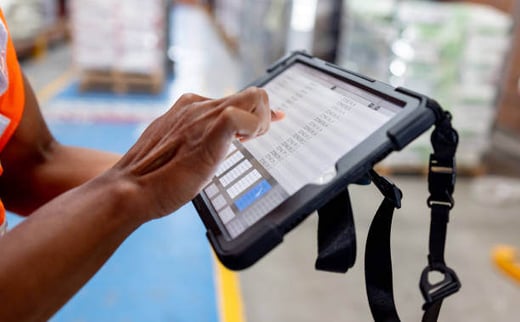
Optimizing Data Management for Production Scheduling in Food and Beverage Manufacturing
Production scheduling in the food and beverage manufacturing industry is a high-stakes balancing act. Schedulers must manage fluctuating demand, short shelf-life products, regulatory compliance, and operational efficiency—all while ensuring minimal waste and maximum throughput. Data management plays a critical role in navigating these challenges effectively. Without accurate, real-time data, even the most well-structured schedules can fall apart, leading to bottlenecks, excess inventory, or underutilized resources.
With the integration of PlanetTogether Advanced Planning and Scheduling (APS) software with enterprise systems such as SAP, Oracle, Microsoft, Kinaxis, or Aveva, production schedulers gain access to a centralized, automated, and intelligent scheduling system that streamlines data management. This article explores how integrated data management enhances scheduling efficiency and optimizes production planning.
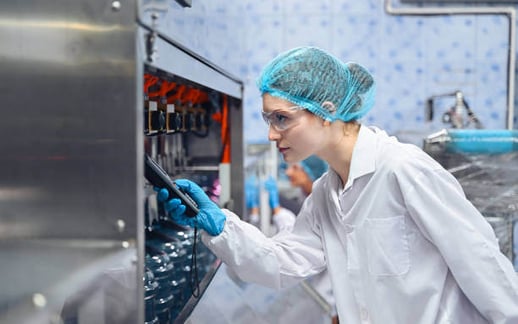
The Role of Data in Production Scheduling
Effective production scheduling relies on accurate, real-time data to optimize manufacturing operations. Data management encompasses:
Demand Forecasting Data: Understanding customer demand fluctuations for proactive scheduling.
Inventory Data: Real-time tracking of raw materials, work-in-progress (WIP), and finished goods.
Machine and Workforce Availability: Ensuring optimal utilization of production resources.
Regulatory Compliance Data: Meeting food safety, quality, and traceability requirements.
Cost and Efficiency Metrics: Analyzing production costs to improve profitability.
Integrating an APS system like PlanetTogether with ERP platforms such as SAP, Oracle, Microsoft, Kinaxis, or Aveva ensures that this data is consolidated and accessible in real-time, allowing schedulers to make informed decisions.
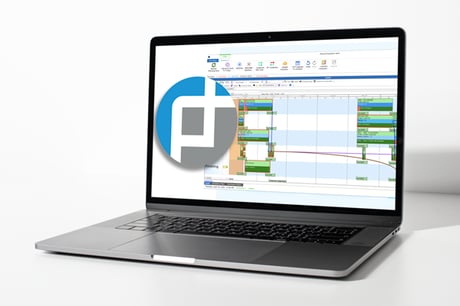
Challenges in Data Management for Food & Beverage Scheduling
Siloed Data and Lack of Visibility
One of the biggest hurdles in food and beverage production scheduling is fragmented data. Schedulers often rely on disconnected spreadsheets, legacy systems, and manual updates, leading to inefficiencies and errors.
Solution: Integration of PlanetTogether APS with an ERP system ensures a seamless flow of data across departments, providing real-time visibility into production schedules, inventory levels, and equipment availability.
Managing Perishable Inventory
Unlike other manufacturing industries, food and beverage manufacturers must deal with raw materials and finished products that have limited shelf lives. Poor data management can result in excessive spoilage or stockouts.
Solution: With an integrated system, PlanetTogether APS uses real-time inventory data from SAP, Oracle, Microsoft, Kinaxis, or Aveva to ensure First-Expire, First-Out (FEFO) scheduling and minimize waste.
Regulatory Compliance and Traceability
Food manufacturers must maintain compliance with FDA, USDA, and other global regulatory standards. Inadequate data tracking can lead to compliance violations, product recalls, and reputational damage.
Solution: Integration enables automated documentation and tracking of production batches, ingredient sourcing, and quality checks, ensuring compliance with industry regulations.
Demand Volatility and Production Adjustments
Food and beverage products are highly sensitive to market trends, seasonal demand shifts, and external disruptions. Traditional static scheduling cannot accommodate sudden changes efficiently.
Solution: APS integration allows for dynamic scheduling adjustments based on demand data, ensuring agility and responsiveness to market changes.
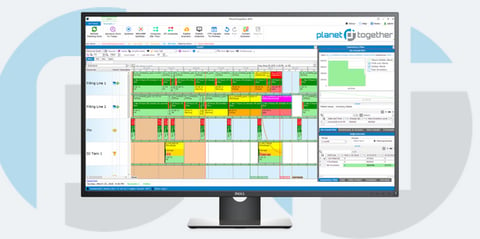
Benefits of Integrating PlanetTogether APS with ERP Systems
Real-time Data Synchronization
By integrating PlanetTogether APS with SAP, Oracle, Microsoft, Kinaxis, or Aveva, data synchronization across the entire manufacturing network becomes seamless. This eliminates delays and ensures that schedulers always work with the most up-to-date information.
Automated Scheduling and Optimization
Integrated APS solutions automatically generate the most efficient production schedules by considering real-time constraints such as machine availability, labor shifts, and raw material stock levels.
Advanced Analytics and Predictive Insights
Schedulers can leverage AI-driven analytics to identify inefficiencies, forecast production bottlenecks, and make proactive decisions. Predictive insights improve order fulfillment rates and reduce unexpected downtime.
Improved Supply Chain Coordination
With APS and ERP integration, food manufacturers achieve better alignment between production planning and supply chain operations. This ensures raw materials arrive just in time, reducing excess inventory costs and storage issues.
Reduction of Waste and Increased Sustainability
Optimized scheduling ensures that perishable raw materials are used efficiently, minimizing food waste. Integrated data analytics also help companies track sustainability KPIs, such as energy consumption and carbon footprint reduction.
In the food and beverage industry, data-driven production scheduling is no longer optional—it’s essential. By integrating PlanetTogether APS with SAP, Oracle, Microsoft, Kinaxis, or Aveva, food manufacturers can transform their scheduling operations with real-time insights, automation, and predictive analytics.
For Production Schedulers, this means fewer scheduling conflicts, better resource utilization, and reduced waste—all while ensuring compliance and responsiveness to market changes. Investing in integrated APS and ERP solutions is the key to staying competitive in today’s dynamic food and beverage manufacturing landscape.
Are you ready to take your manufacturing operations to the next level? Contact us today to learn more about how PlanetTogether can help you achieve your goals and drive success in your industry.
LEAVE A COMMENT