Custom Order Production Scheduling
Production scheduling plays a pivotal role in meeting customer demands efficiently in food and beverage manufacturing. As a Production Scheduler in this industry, you're no stranger to the challenges posed by custom orders. Meeting the unique requirements of each order while ensuring efficient resource utilization is no easy task.
In this blog, we'll look into the art of production scheduling for custom orders and explore how integration between PlanetTogether and leading ERP, SCM, and MES systems like SAP, Oracle, Microsoft, Kinaxis, and Aveva can elevate your scheduling game.
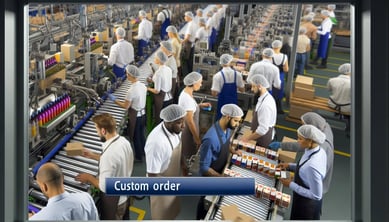
The Challenge of Custom Orders
Custom orders are a double-edged sword. On one hand, they allow your company to cater to individual customer needs and preferences, fostering brand loyalty. On the other hand, they can disrupt your production flow, leading to increased costs, longer lead times, and potential customer dissatisfaction. Here's where effective production scheduling becomes crucial.
Demand Variability
Custom orders bring unpredictability to your production floor. Unlike standard products with consistent demand, custom orders can fluctuate wildly, making it challenging to allocate resources efficiently.
Recipe and Ingredient Complexity
Food and beverage manufacturers often deal with complex recipes and ingredient lists. Custom orders may require unique ingredients or formulations, further complicating scheduling.
Equipment Constraints
Certain equipment may be dedicated to specific product lines, making it harder to fit custom orders into your production schedule without causing bottlenecks.
The Role of Production Scheduling
Production scheduling is the compass that guides your manufacturing operations through the tumultuous waters of custom orders. It helps you strike a balance between meeting customer expectations and optimizing resource utilization.

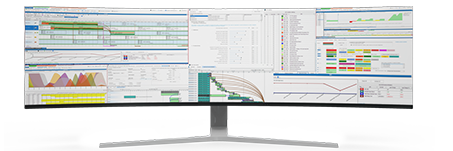
Integrating PlanetTogether with Leading ERP, SCM, and MES Systems
Integration with SAP
SAP is a powerhouse in the world of enterprise resource planning. Integrating PlanetTogether with SAP brings a seamless flow of information between production scheduling and other critical business processes.
Real-Time Data: SAP integration ensures that your production schedule is always based on the most up-to-date data, reducing the risk of overcommitting resources.
Streamlined Communication: Orders and changes made in SAP are automatically reflected in PlanetTogether, eliminating the need for manual data entry and reducing the chance of errors.
Integration with Oracle
Oracle is renowned for its robust supply chain management solutions. When integrated with PlanetTogether, Oracle can help you tackle the intricacies of custom order scheduling effectively.
Predictive Analytics: Oracle's predictive analytics capabilities can be leveraged by PlanetTogether to anticipate demand fluctuations and adjust schedules accordingly.
Inventory Management: Integration allows for better inventory visibility, ensuring that the necessary ingredients are on hand when custom orders come in.
Integration with Microsoft Dynamics
Microsoft Dynamics offers a comprehensive suite of business solutions. Integration with PlanetTogether and Microsoft Dynamics can enhance your production scheduling in several ways:
Collaboration: Seamless communication between scheduling and other departments ensures that everyone is on the same page regarding custom orders.
Data Analysis: Microsoft's data analytics tools can provide valuable insights into production trends, helping you make informed scheduling decisions.
Integration with Kinaxis
Kinaxis specializes in supply chain solutions, making it an ideal partner for PlanetTogether in custom order scheduling.
Scenario Planning: Kinaxis's scenario planning capabilities can help you model different scheduling scenarios for custom orders, allowing you to choose the most efficient one.
Supply Chain Visibility: Integration with Kinaxis provides end-to-end supply chain visibility, aiding in better decision-making during custom order scheduling.
Integration with Aveva
Aveva's manufacturing execution system (MES) is designed to optimize production operations. When integrated with PlanetTogether, it can streamline custom order scheduling.
Production Monitoring: Real-time production data from Aveva enhances the accuracy of your schedules, ensuring that custom orders are produced as efficiently as possible.
Quality Control: Aveva's MES capabilities can be used to implement stringent quality control measures for custom orders.
Other ERP, SCM, and MES Systems
Apart from the mentioned systems, there are numerous other ERP, SCM, and MES systems available in the market. The key takeaway here is the importance of integrating your chosen system with PlanetTogether. Regardless of the system you use, integration enables:
Efficiency: Reduced manual intervention and automated data exchange lead to more efficient scheduling processes.
Accuracy: Real-time data synchronization ensures that your schedules are based on the latest information.
Flexibility: Customization options allow you to tailor the integration to meet your specific custom order scheduling needs.
Custom orders are a defining feature of the food and beverage manufacturing industry. While they present challenges, they also offer opportunities for differentiation and customer satisfaction. By embracing the power of integrated production scheduling with systems like SAP, Oracle, Microsoft, Kinaxis, Aveva, and others, you can navigate the complexities of custom orders with confidence.
As a Production Scheduler, your role is pivotal in ensuring that custom orders are executed flawlessly. The integration of PlanetTogether with your chosen ERP, SCM, or MES system empowers you with the tools and insights needed to optimize scheduling, meet customer expectations, and drive the success of your food and beverage manufacturing facility.