Concurrent Engineering Approaches
Companies are under increasing pressure to optimize production processes, reduce costs, and improve efficiency while maintaining high-quality standards and meeting customer demands. Concurrent engineering, a methodology that emphasizes collaboration and integration across various stages of product development and manufacturing, has emerged as a key strategy to achieve these goals.
In this blog, we'll look into the concept of concurrent engineering and explore how it can be effectively applied in chemical manufacturing facilities, with a particular focus on the integration between production planning tools like PlanetTogether and leading ERP, SCM, and MES systems such as SAP, Oracle, Microsoft, Kinaxis, and Aveva.
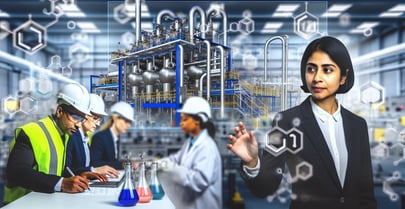
Concurrent Engineering
Concurrent engineering is a holistic approach that emphasizes the parallelization and integration of tasks traditionally performed sequentially in the product development and manufacturing process. Rather than waiting for one stage to be completed before moving on to the next, concurrent engineering allows for simultaneous collaboration between cross-functional teams, including design, engineering, production planning, procurement, and quality assurance.
By breaking down silos and fostering real-time communication and collaboration, concurrent engineering enables companies to streamline processes, reduce lead times, minimize errors, and ultimately bring products to market faster and more efficiently.
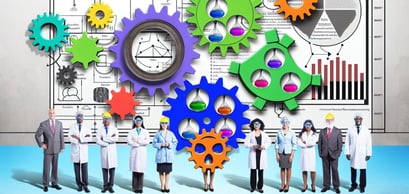
Key Principles of Concurrent Engineering
Early Collaboration: One of the fundamental principles of concurrent engineering is early collaboration among all stakeholders involved in the product lifecycle. By involving design, engineering, and production planning teams from the outset, companies can identify potential issues, address constraints, and make informed decisions that optimize both product design and manufacturing processes.
Integrated Information Systems: Effective communication and information sharing are essential for successful concurrent engineering implementation. Integration between production planning tools such as PlanetTogether and ERP, SCM, and MES systems like SAP, Oracle, Microsoft, Kinaxis, and Aveva play a crucial role in ensuring seamless data exchange across various functional areas.
This integration enables real-time visibility into inventory levels, production schedules, resource allocation, and other critical metrics, allowing teams to make data-driven decisions and respond promptly to changing market dynamics.
Iterative Design and Optimization: Concurrent engineering promotes an iterative approach to design and optimization, where teams continuously evaluate and refine product designs and manufacturing processes throughout the development lifecycle. By leveraging simulation, modeling, and predictive analytics capabilities, companies can identify potential bottlenecks, optimize production schedules, and mitigate risks proactively, leading to improved product quality and reduced time-to-market.
Cross-Functional Teams: Successful implementation of concurrent engineering requires collaboration and alignment across cross-functional teams with diverse expertise and perspectives. By breaking down departmental silos and fostering a culture of collaboration and knowledge sharing, companies can leverage the collective expertise of their teams to drive innovation, problem-solving, and continuous improvement initiatives.
Challenges in Implementing Concurrent Engineering
While the benefits of concurrent engineering are compelling, its successful implementation requires overcoming several challenges, including:
Cultural barriers: Shifting from a traditional sequential approach to a collaborative, cross-functional model may encounter resistance from entrenched organizational cultures.
Integration complexity: Integrating disparate systems and workflows across departments can be complex, requiring robust IT infrastructure and seamless data exchange mechanisms.
Change management: Adopting concurrent engineering requires a mindset shift and may necessitate training and support to ensure buy-in from all stakeholders.

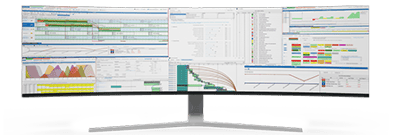
Integration of PlanetTogether with ERP, SCM, and MES Systems
To fully harness the power of concurrent engineering, chemical manufacturing facilities can leverage advanced planning and scheduling tools like PlanetTogether, integrated with leading ERP, SCM, and MES systems such as SAP, Oracle, Microsoft Dynamics, Kinaxis, and Aveva. Here's how this integration can drive operational excellence:
Real-Time Data Visibility: By integrating PlanetTogether with ERP systems, production planners gain real-time visibility into inventory levels, order status, and resource availability. This seamless flow of information enables better decision-making, as planners can quickly adjust production schedules in response to changing demand or supply chain disruptions.
Streamlined Workflows: Integrating PlanetTogether with MES systems allows for seamless data exchange between production planning and shop floor execution. This integration enables automated scheduling of manufacturing operations based on real-time machine availability, labor capacity, and material availability, minimizing downtime and maximizing resource utilization.
Demand Forecasting and Inventory Optimization: By integrating PlanetTogether with SCM systems, production planners can leverage advanced forecasting algorithms to predict demand trends accurately. This enables proactive inventory management, ensuring that raw materials are available when needed while minimizing excess inventory and carrying costs.
Enhanced Collaboration and Communication: Integration with collaboration tools such as Microsoft Teams or Slack facilitates real-time communication and collaboration among cross-functional teams. Whether it's sharing production schedules, coordinating maintenance activities, or resolving production bottlenecks, seamless communication accelerates decision-making and problem-solving.
Concurrent engineering represents a paradigm shift in how chemical manufacturing facilities approach product design and production planning. By breaking down silos, promoting collaboration, and leveraging integrated planning systems, companies can achieve greater agility, efficiency, and innovation.
By integrating advanced planning and scheduling tools like PlanetTogether with ERP, SCM, and MES systems, production planners can optimize resource utilization, minimize lead times, and drive operational excellence in today's competitive marketplace.
Embracing concurrent engineering is not just a strategy for survival—it's a pathway to sustainable growth and success in the chemical manufacturing industry. Are you ready to take your manufacturing operations to the next level? Contact us today to learn more about how PlanetTogether can help you achieve your goals and drive success in your industry.