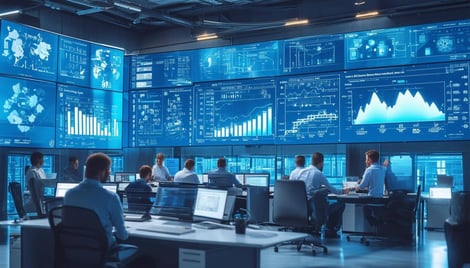
Optimizing Capacity Planning for Production Planners in Chemical Manufacturing
Capacity planning is a critical component of chemical manufacturing, where precision, efficiency, and adaptability determine success. For production planners, managing production schedules and resources effectively can be daunting, especially in a dynamic environment where demand volatility, regulatory compliance, and safety standards converge. Integrating advanced production planning tools like PlanetTogether with enterprise systems such as SAP, Oracle, Microsoft, Kinaxis, or Aveva can transform capacity planning processes.
This blog explores how production planners in chemical manufacturing can optimize capacity planning, leveraging the synergy of PlanetTogether and leading ERP/MES platforms.
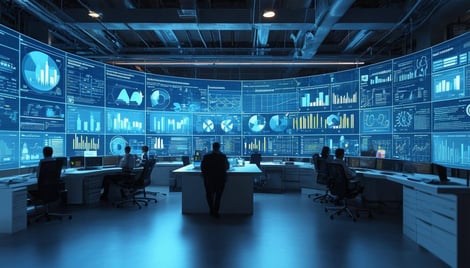
The Unique Challenges of Capacity Planning in Chemical Manufacturing
Capacity planning in chemical manufacturing is unlike other industries due to the sector's inherent complexities:
- Variable Batch Sizes: Production often involves batch processing, requiring precise calculations to optimize the use of reactors, mixers, and other equipment.
- Regulatory Constraints: Compliance with safety and environmental regulations can impose limitations on capacity utilization and production schedules.
- Volatile Demand: Fluctuations in demand for chemical products necessitate flexible and scalable production planning.
- Resource Dependency: Equipment availability, raw material constraints, and workforce scheduling are tightly interlinked.
These factors demand a capacity planning approach that is agile, data-driven, and seamlessly integrated across the organization.
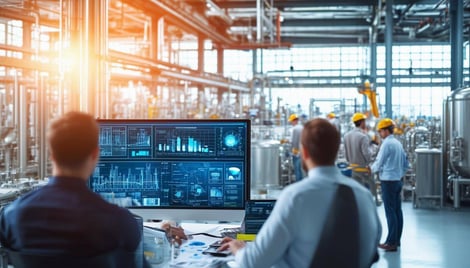
Why Traditional Capacity Planning Falls Short
Traditional capacity planning relies on static spreadsheets, siloed systems, and manual adjustments. While these methods may work for routine operations, they fall short when responding to real-time changes or aligning production with strategic goals. Key limitations include:
Lack of Real-Time Visibility: Disconnected systems prevent planners from gaining a holistic view of operations, leading to suboptimal decisions.
Inflexible Planning Models: Static models are ill-suited for dynamic environments, where rapid adjustments are necessary.
High Risk of Errors: Manual processes are prone to errors, which can result in resource wastage, delays, or compliance issues.
To overcome these limitations, integrating advanced planning tools like PlanetTogether with robust ERP/MES platforms is essential.

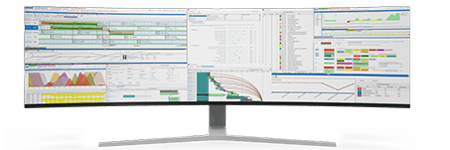
Optimizing Capacity Planning with PlanetTogether
PlanetTogether is a powerful production scheduling and capacity planning tool designed to enhance operational efficiency and agility. By integrating PlanetTogether with ERP systems such as SAP, Oracle, Microsoft, Kinaxis, or Aveva, chemical manufacturers can achieve:
- Enhanced Visibility: A unified view of production schedules, resource availability, and demand forecasts.
- Dynamic Scheduling: Automated adjustments to schedules in response to real-time changes in demand, inventory, or equipment status.
- Scenario Analysis: The ability to model multiple capacity planning scenarios and evaluate their impact on KPIs such as throughput, costs, and on-time delivery.
- Collaboration Across Teams: Seamless data sharing between planning, procurement, and operations teams, ensuring alignment and reducing silos.
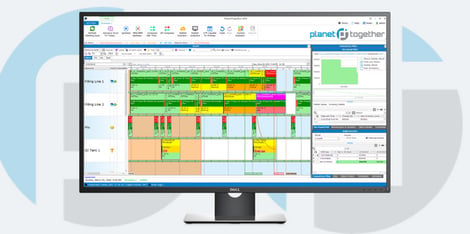
Key Features of PlanetTogether Integration
The integration of PlanetTogether with platforms like SAP, Oracle, Microsoft Dynamics 365, Kinaxis, or Aveva offers production planners in chemical manufacturing several critical advantages:
1. Real-Time Data Synchronization
PlanetTogether pulls data from ERP systems to create a real-time, detailed view of production capacity. For instance, integrating with SAP provides access to material availability, sales orders, and production data, ensuring planners have accurate, up-to-date information for decision-making.
2. Capacity Optimization
PlanetTogether’s advanced algorithms analyze production constraints, such as equipment downtime or labor availability, to maximize capacity utilization. Integration with Aveva MES enhances this by incorporating IoT data from shop-floor equipment, providing insights into machine performance and availability.
3. Demand Forecasting and Planning
By connecting PlanetTogether with Kinaxis for supply chain management, planners can align production capacity with demand forecasts, reducing the risk of overproduction or stockouts.
4. Regulatory Compliance
PlanetTogether’s scheduling engine considers regulatory constraints, such as maximum production limits or hazardous material handling requirements. Oracle’s robust compliance tools complement this by ensuring adherence to industry standards.
5. User-Friendly Interface
Microsoft Dynamics 365 integration provides an intuitive interface for planners, simplifying the management of complex schedules and enabling easy collaboration with other departments.
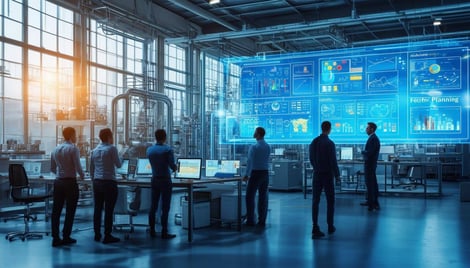
Best Practices for Implementing PlanetTogether Integration
To fully realize the benefits of PlanetTogether integration, chemical manufacturers should consider the following best practices:
- Define Clear Objectives: Identify specific pain points in your current capacity planning process and set measurable goals for improvement.
- Ensure Data Quality: Accurate, consistent data is crucial for effective planning. Invest in data cleansing and validation before integration.
- Collaborate Across Teams: Involve stakeholders from production, supply chain, IT, and compliance teams to ensure alignment and smooth implementation.
- Train Users: Provide comprehensive training for planners and operators to maximize the tool’s potential.
- Monitor and Optimize: Continuously monitor the system’s performance and refine planning parameters based on feedback and changing conditions.
As the chemical manufacturing industry evolves, capacity planning will increasingly rely on advanced technologies like artificial intelligence, machine learning, and predictive analytics. PlanetTogether is well-positioned to integrate these capabilities, offering production planners unprecedented levels of insight and control. By combining the power of PlanetTogether with platforms like SAP, Oracle, Microsoft, Kinaxis, or Aveva, manufacturers can not only optimize capacity planning but also achieve strategic objectives such as sustainability, cost reduction, and customer satisfaction.
For production planners in chemical manufacturing, the integration of PlanetTogether with leading ERP/MES platforms marks a significant step forward in capacity planning. By leveraging real-time data, dynamic scheduling, and advanced analytics, planners can overcome traditional limitations and drive operational excellence. The result is a more agile, efficient, and resilient manufacturing process that meets the demands of a competitive and rapidly changing market.
Are you ready to take your manufacturing operations to the next level? Contact us today to learn more about how PlanetTogether can help you achieve your goals and drive success in your industry.
LEAVE A COMMENT