Improving Replenishment Materials Efficiency
Optimizing replenishment materials management can significantly impact operational success in packaging manufacturing. As a Plant Manager, you understand the critical balance between meeting production demands and managing inventory costs.
This blog explores strategies and tools to enhance replenishment materials efficiency, with a focus on integration between PlanetTogether, a leading production planning software, and major enterprise resource planning (ERP) systems like SAP, Oracle, Microsoft, Kinaxis, and Aveva.
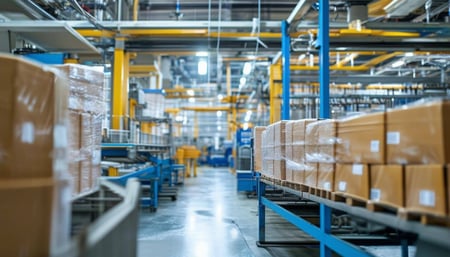
Replenishment Materials Efficiency
Efficient replenishment materials management involves the timely acquisition of raw materials and supplies needed for production. Key metrics include inventory turnover rates, stockout occurrences, and lead times. By optimizing these factors, manufacturers can reduce costs, minimize waste, and improve production continuity.
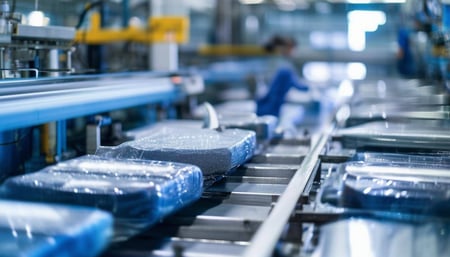
Challenges in Materials Replenishment
Forecasting Accuracy
Accurate demand forecasting is crucial for determining the quantity and timing of replenishment orders. Challenges often arise from unpredictable market trends, seasonal variations, and sudden shifts in customer demand. Traditional forecasting methods may not suffice in today's dynamic market environment.
Inventory Management
Balancing inventory levels is essential to prevent stockouts without overstocking, which ties up capital and storage space. Poor inventory management can lead to increased costs, production delays, and customer dissatisfaction.
Supplier Relationships
Effective communication and collaboration with suppliers are vital for ensuring timely deliveries and resolving supply chain disruptions. Poor supplier management can lead to delays, quality issues, and increased costs.

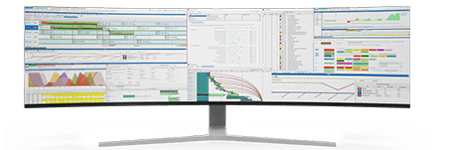
Integration of PlanetTogether with ERP Systems
PlanetTogether offers robust production planning capabilities that can be enhanced through integration with ERP systems such as SAP, Oracle, Microsoft Dynamics, Kinaxis RapidResponse, and Aveva. This integration allows for seamless data exchange and real-time updates between production schedules and inventory management systems.
SAP Integration: SAP ERP integration with PlanetTogether enables synchronized production planning and procurement processes. Real-time data visibility improves decision-making and reduces lead times.
Oracle Integration: Oracle ERP integration enhances supply chain visibility and streamlines order processing. By automating replenishment workflows, manufacturers can optimize inventory levels and reduce carrying costs.
Microsoft Dynamics Integration: Integration with Microsoft Dynamics ERP provides comprehensive production planning capabilities. Automated data synchronization improves forecasting accuracy and inventory management efficiency.
Kinaxis RapidResponse Integration: Kinaxis integration facilitates real-time demand sensing and scenario analysis. This capability enables agile responses to market changes and minimizes supply chain risks.
Aveva Integration: Aveva ERP integration supports end-to-end supply chain optimization. By integrating with PlanetTogether, manufacturers can achieve operational excellence through advanced analytics and predictive insights.
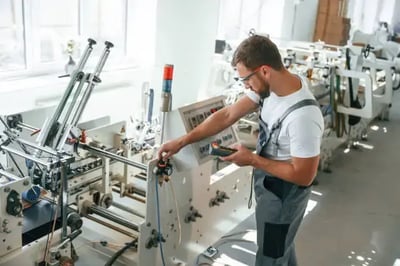
Strategies for Optimizing Replenishment Materials Efficiency
Demand Forecasting and Planning
Implement advanced forecasting techniques supported by historical data analysis, machine learning algorithms, and predictive analytics. Collaborate closely with sales and marketing teams to incorporate market intelligence into demand planning processes.
Lean Inventory Practices
Adopt lean manufacturing principles to reduce waste and optimize inventory levels. Implement just-in-time (JIT) and kanban systems to synchronize production with demand and minimize excess inventory.
Supplier Collaboration
Establish strategic partnerships with key suppliers and implement vendor-managed inventory (VMI) programs. Leverage supplier portals and automated communication channels to improve transparency and responsiveness.
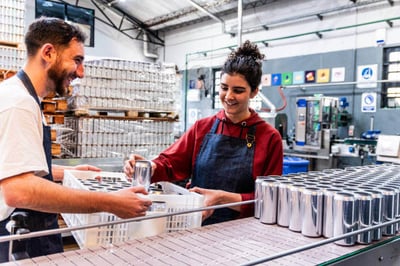
Benefits of Improved Replenishment Materials Efficiency
Cost Reduction
Optimizing materials replenishment reduces carrying costs associated with excess inventory and minimizes stockouts that lead to production delays and expedited shipping expenses.
Enhanced Productivity
Streamlined production planning and materials management processes improve overall operational efficiency and resource utilization, allowing for increased throughput and on-time deliveries.
Improved Customer Satisfaction
Consistent supply availability and reliable delivery schedules enhance customer satisfaction and loyalty, positioning the company competitively in the market.
Optimizing replenishment materials efficiency is critical for packaging manufacturing facilities to achieve sustainable growth and competitive advantage. By integrating advanced production planning software like PlanetTogether with ERP systems such as SAP, Oracle, Microsoft, Kinaxis, and Aveva, plant managers can streamline operations, reduce costs, and improve overall supply chain resilience.
Embracing innovative technologies and best practices in materials management will pave the way for continued success in the dynamic packaging industry.
Are you ready to take your manufacturing operations to the next level? Contact us today to learn more about how PlanetTogether can help you achieve your goals and drive success in your industry.