Mixed-Model Manufacturing Scheduling
In today's evolving market, the packaging manufacturing industry faces unique challenges in meeting diverse customer demands while maintaining efficiency and minimizing costs. Mixed-model manufacturing, where multiple product types are produced on the same production line, offers a flexible solution to these challenges. However, the complexity of scheduling in a mixed-model environment can be daunting without the right tools and strategies.
This blog explores how integrating advanced planning systems like PlanetTogether with ERP, SCM, and MES systems such as SAP, Oracle, Microsoft, Kinaxis, and Aveva can revolutionize scheduling practices for production planners.
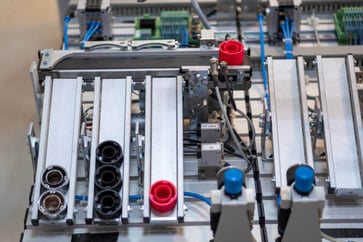
Mixed-Model Manufacturing
Mixed-model manufacturing is characterized by its ability to handle various products on a single production line. This approach not only optimizes equipment usage but also reduces the time and cost associated with setup changes. However, it introduces complexity in production planning and scheduling, demanding a strategy that can seamlessly integrate detailed scheduling with broad-scale operational planning.
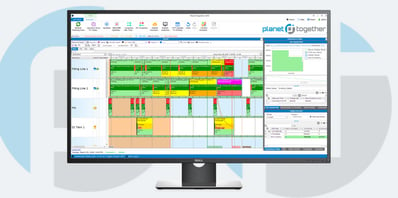
The Role of Advanced Planning Systems (APS)
PlanetTogether is a prominent APS that stands out in managing the complexities of mixed-model manufacturing. It provides real-time visibility, advanced analytics, and powerful simulation capabilities, which are essential for effective decision-making. Here’s how PlanetTogether interacts with various ERP, SCM, and MES systems:
Integration with SAP
SAP, being one of the leading ERP systems, offers robust functionalities for managing business operations. Integrating PlanetTogether with SAP enables production planners to synchronize manufacturing schedules with business processes, ensuring that inventory levels, workforce capacity, and production timelines are aligned with the overall business objectives. This integration facilitates a more agile response to market changes, optimizing operational efficiency and reducing lead times.
Oracle Integration
Oracle's ERP solutions are renowned for their scalability and comprehensive feature set. When integrated with PlanetTogether, production planners can leverage enhanced data analytics and real-time data exchange. This synergy improves forecasting accuracy, demand planning, and capacity planning, providing a holistic view of the production landscape and enabling more informed decision-making.
Microsoft Dynamics 365
Microsoft Dynamics 365 brings together CRM and ERP capabilities into a comprehensive business management solution. Integrating this system with PlanetTogether allows for a unified approach to resource planning and management. The combined power of Dynamics 365 and PlanetTogether enhances workflow automation, reduces redundancy, and streamlines scheduling activities, making it easier to manage multiple product lines efficiently.
Kinaxis RapidResponse
Kinaxis RapidResponse is a supply chain management software that excels in rapid scenario planning. The integration of PlanetTogether with Kinaxis RapidResponse empowers production planners with the ability to quickly adjust schedules in response to supply chain disruptions or sudden shifts in demand. This integration ensures continuous alignment of supply chain plans with production schedules, crucial for maintaining service levels in the face of volatility.
Aveva Integration
Aveva's solutions focus on industrial software that drives digital transformation. By integrating Aveva's MES with PlanetTogether, production planners gain access to detailed insights into machine performance and maintenance schedules. This information is critical for optimizing machine utilization and minimizing downtime in a mixed-model manufacturing setup.
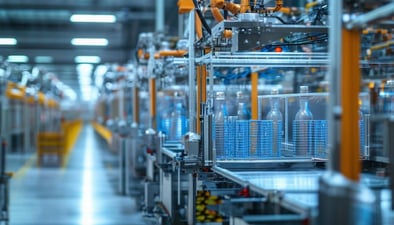
Challenges in Mixed-Model Manufacturing Scheduling
While the integration of APS with ERP, SCM, and MES systems brings numerous benefits, it also presents several challenges:
Data Synchronization: Ensuring real-time data flow between different systems can be complex. It requires robust IT infrastructure and effective data governance policies.
Change Management: Implementing a new scheduling system or upgrading existing systems necessitates careful change management. Training staff and aligning business processes with new technologies are crucial for successful integration.
Customization and Scalability: Each manufacturing facility has unique needs. Customizing solutions to fit specific requirements while ensuring they are scalable to handle future growth poses a significant challenge.
Best Practices for Effective Scheduling
To overcome these challenges, production planners should consider the following best practices:
Continuous Training and Support: Regular training sessions for staff to enhance familiarity with new systems and processes.
Phased Implementation: Gradually integrating new systems to minimize disruptions.
Regular System Reviews: Periodically reviewing system performance and making adjustments as needed.
The integration of advanced planning systems like PlanetTogether with major ERP, SCM, and MES systems is transforming the landscape of mixed-model manufacturing. By harnessing the strengths of each system, production planners in the packaging manufacturing industry can achieve unprecedented levels of operational efficiency and flexibility.
Embracing these technologies and adhering to best practices in implementation will ensure that companies remain competitive in a dynamic market environment.
For production planners looking to enhance their mixed-model manufacturing scheduling capabilities, exploring the integration options between PlanetTogether and your existing systems is a step towards achieving operational excellence. Engage with IT specialists and system providers to tailor a solution that best fits your operational needs and strategic goals.
Are you ready to take your manufacturing operations to the next level? Contact us today to learn more about how PlanetTogether can help you achieve your goals and drive success in your industry.
LEAVE A COMMENT