Navigating Sustainable Manufacturing Ecosystems
As a production scheduler in food and beverage manufacturing, you play a pivotal role in ensuring that operations run smoothly while also contributing to the broader goal of creating sustainable manufacturing ecosystems.
In this blog, we'll explore how the integration between PlanetTogether and leading ERP, SCM, and MES systems can revolutionize your approach to sustainability.
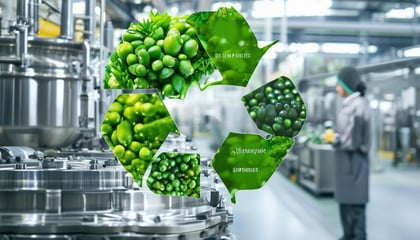
Sustainable Manufacturing Ecosystems
Essentially, it's about fostering a harmonious relationship between people, processes, and the planet. This involves optimizing resource utilization, minimizing waste, reducing carbon footprint, and prioritizing ethical practices throughout the supply chain.
For a production scheduler, this translates into balancing production efficiency with environmental responsibility. It means optimizing schedules to minimize energy consumption, reducing material waste, and ensuring compliance with sustainability regulations. Achieving these objectives requires not only operational excellence but also seamless integration between various software systems.

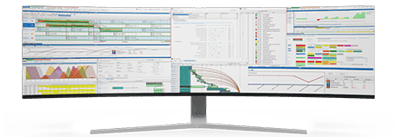
The Role of Integration
Integration lies at the heart of sustainable manufacturing ecosystems. By connecting disparate systems such as Enterprise Resource Planning (ERP), Supply Chain Management (SCM), Manufacturing Execution Systems (MES), and production scheduling software like PlanetTogether, organizations can streamline operations, enhance visibility, and make data-driven decisions to drive sustainability initiatives.
Among the myriad of integration possibilities, let's focus on the synergy between PlanetTogether and leading ERP systems like SAP, Oracle, Microsoft, Kinaxis, and Aveva.
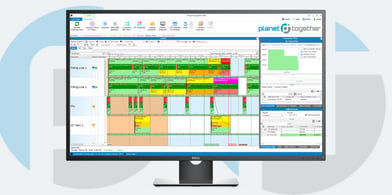
PlanetTogether and ERP Integration: A Game-Changer for Sustainability
Data Synchronization: Integrating PlanetTogether with ERP systems enables seamless data synchronization across the production planning and execution landscape. This ensures that schedules are aligned with real-time demand forecasts, inventory levels, and procurement plans, thereby minimizing overproduction and reducing waste.
Optimized Resource Utilization: By leveraging data from ERP systems, production schedulers can optimize resource utilization based on factors such as machine availability, labor capacity, and energy consumption. This allows for the creation of leaner schedules that maximize efficiency while minimizing environmental impact.
Supply Chain Visibility: Integration between PlanetTogether and ERP systems provides end-to-end visibility into the supply chain, from raw material sourcing to finished product delivery. This transparency allows production schedulers to proactively identify and address sustainability risks such as supplier non-compliance or transportation inefficiencies.
Compliance Management: With stringent regulations governing environmental sustainability, compliance management is paramount for food and beverage manufacturers. By integrating PlanetTogether with ERP systems, organizations can automate compliance monitoring, track sustainability metrics, and generate reports to demonstrate adherence to regulatory requirements.
Sustainable manufacturing ecosystems are the cornerstone of modern food and beverage manufacturing. As a production scheduler, your ability to navigate these ecosystems hinges on effective integration between production scheduling software like PlanetTogether and ERP, SCM, and MES systems.
By harnessing the power of integration, you can optimize resource utilization, enhance supply chain visibility, and ensure compliance with sustainability regulations. In doing so, you not only drive operational excellence but also contribute to the greater goal of creating a more sustainable future for generations to come.
Are you ready to take your manufacturing operations to the next level? Contact us today to learn more about how PlanetTogether can help you achieve your goals and drive success in your industry.
LEAVE A COMMENT