Building Resilient Manufacturing Strategies
In the interconnected world, supply chain disruptions have become a common challenge for businesses across all industries. However, the food and beverage manufacturing sector faces unique hurdles due to its perishable nature, stringent regulations, and complex supply networks. Supply chain managers in these facilities constantly grapple with ensuring uninterrupted production while mitigating risks associated with disruptions.
In this blog, we'll look into the development of resilient manufacturing strategies tailored specifically for the food and beverage industry. We'll explore the integration between advanced planning and scheduling (APS) tools like PlanetTogether and leading Enterprise Resource Planning (ERP), Supply Chain Management (SCM), and Manufacturing Execution Systems (MES) such as SAP, Oracle, Microsoft, Kinaxis, Aveva, and others.
By leveraging these technologies, supply chain managers can fortify their operations against disruptions and safeguard their production processes.
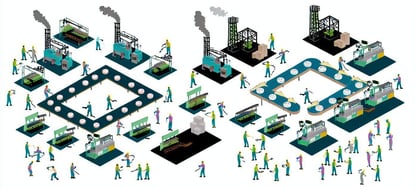
Understanding the Challenges
The food and beverage industry operates within a highly dynamic environment, characterized by fluctuating consumer demands, seasonality, stringent regulatory requirements, and a diverse supplier base. These factors make it susceptible to various disruptions such as ingredient shortages, transportation delays, natural disasters, and regulatory changes.
In such a scenario, a single disruption can cascade down the entire supply chain, leading to production delays, increased costs, and ultimately, customer dissatisfaction.
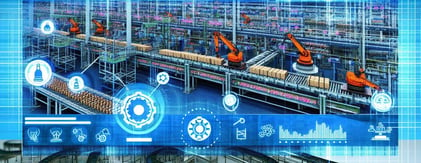
Resilient Manufacturing Strategies
To address these challenges, food and beverage manufacturers need to adopt resilient manufacturing strategies that prioritize flexibility, agility, and adaptability. Here are key components of such strategies:
Demand Forecasting and Planning: Accurate demand forecasting forms the foundation of resilient manufacturing. By leveraging historical data, market trends, and predictive analytics, manufacturers can anticipate demand fluctuations and adjust production schedules accordingly. Advanced planning and scheduling (APS) tools like PlanetTogether play a crucial role in optimizing production plans, considering capacity constraints, material availability, and production priorities.
Supplier Collaboration and Diversification: Collaborating closely with suppliers and building robust relationships can mitigate the risk of supply chain disruptions. Establishing alternative sourcing options and maintaining safety stock of critical ingredients or components can buffer against sudden supplier failures or shortages. Integration between ERP systems like SAP or Oracle and APS tools enables real-time visibility into supplier performance, inventory levels, and lead times, facilitating proactive decision-making.
Inventory Optimization: Striking the right balance between inventory levels and customer service levels is paramount for resilience. Excessive inventory ties up capital and increases carrying costs, while insufficient stock leaves manufacturers vulnerable to demand spikes or supply disruptions. By integrating APS tools with ERP systems, supply chain managers can optimize inventory levels, synchronize production with demand, and minimize excess stock through just-in-time manufacturing practices.
Production Flexibility and Efficiency: Investing in flexible manufacturing processes and agile production lines enables swift adaptation to changing market conditions or unforeseen disruptions. MES systems provide real-time visibility into production workflows, equipment performance, and quality metrics, empowering operators to identify bottlenecks, optimize production schedules, and maintain consistent product quality. Integration between MES and APS tools facilitates seamless data exchange, enabling synchronized planning and execution across the production floor.
Continuous Improvement and Risk Management: Resilience is not a one-time effort but an ongoing journey of continuous improvement and risk mitigation. Conducting regular supply chain risk assessments, scenario planning, and implementing contingency plans can enhance preparedness for potential disruptions. Leveraging advanced analytics and machine learning algorithms within ERP and SCM systems enables proactive risk identification, root cause analysis, and scenario simulation, empowering supply chain managers to make informed decisions and pre-emptively address vulnerabilities.
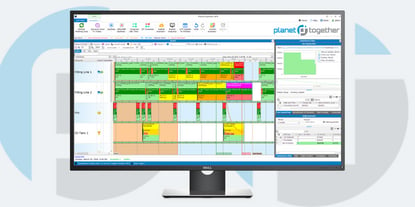
Integration between PlanetTogether and ERP/SCM/MES Systems
The integration between advanced planning and scheduling (APS) tools like PlanetTogether and leading ERP, SCM, and MES systems plays a pivotal role in orchestrating resilient manufacturing strategies in the food and beverage industry. Here's how this integration enhances operational efficiency and agility:
Real-time Data Synchronization: Integration ensures seamless data exchange between APS and ERP/SCM/MES systems, eliminating silos and providing supply chain managers with a unified view of operations. Real-time visibility into inventory levels, production schedules, and order statuses enables timely decision-making and proactive risk management.
Optimized Production Planning: By combining the forecasting capabilities of ERP/SCM systems with the optimization algorithms of APS tools, manufacturers can generate accurate production plans that balance demand, capacity, and inventory constraints. This enables efficient resource utilization, reduces lead times, and improves on-time delivery performance.
Dynamic Response to Changes: In a volatile environment, the ability to quickly adapt production schedules in response to demand fluctuations or supply disruptions is critical. Integration between PlanetTogether and ERP/SCM systems enables automated re-scheduling based on real-time data updates, enabling supply chain managers to rapidly adjust production priorities, allocate resources, and minimize the impact of disruptions on customer service levels.
Enhanced Collaboration and Visibility: Integrated systems facilitate seamless collaboration across departments and supply chain partners by providing a centralized platform for communication and data sharing. Supply chain managers can track production progress, monitor KPIs, and collaborate with suppliers or customers in real-time, fostering transparency and accountability throughout the supply chain.
The development of resilient manufacturing strategies is imperative for food and beverage manufacturers to navigate supply chain disruptions effectively. By embracing technologies like advanced planning and scheduling (APS) tools and integrating them with leading ERP, SCM, and MES systems, supply chain managers can enhance operational efficiency, agility, and adaptability.
By adopting a proactive approach to risk management, leveraging data-driven insights, and fostering collaboration across the supply chain, food and beverage manufacturers can build robust and resilient operations capable of withstanding any disruptions that come their way.
Remember, resilience is not just about weathering the storm but thriving in the face of adversity. Embrace change, empower your teams, and leverage technology to build a supply chain that's not just resilient but truly agile and future-proof.
Are you ready to take your manufacturing operations to the next level? Contact us today to learn more about how PlanetTogether can help you achieve your goals and drive success in your industry.