Humanitarian Logistics: Overcoming Scheduling Challenges in Medical Manufacturing Facilities
The orchestration of logistics becomes not just a strategic imperative but a humanitarian one in medical manufacturing. The seamless integration of Manufacturing Execution Systems (MES), Enterprise Resource Planning (ERP), and Supply Chain Management (SCM) platforms is crucial in ensuring that life-saving medical supplies reach those in need, especially in times of crisis. However, this endeavor is not without its challenges.
In this blog, we look into the complexities of humanitarian logistics and explore how integration between PlanetTogether and leading ERP, SCM, and MES systems can help overcome scheduling hurdles in medical manufacturing facilities.
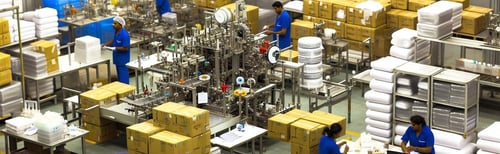
Understanding Humanitarian Logistics
Humanitarian logistics involves the efficient and effective flow of goods and services to those in need during crisis situations such as natural disasters, pandemics, or conflicts. In the context of medical manufacturing, this entails the timely production, distribution, and delivery of essential medical supplies such as pharmaceuticals, vaccines, and medical devices to healthcare facilities and disaster-stricken areas.
Challenges in Humanitarian Logistics
Demand Uncertainty: During humanitarian crises, demand for medical supplies can fluctuate rapidly and unpredictably. Forecasting becomes exceedingly challenging, making it difficult for manufacturers to plan production schedules accurately.
Supply Chain Disruptions: Natural disasters, geopolitical conflicts, or global pandemics can disrupt supply chains, leading to shortages of raw materials, transportation bottlenecks, or production delays.
Regulatory Compliance: Medical manufacturing facilities must adhere to stringent regulatory requirements, which can vary across regions and jurisdictions. Compliance with regulations such as Good Manufacturing Practices (GMP) adds another layer of complexity to logistics operations.
Limited Resources: Humanitarian crises often strain resources, including manpower, equipment, and infrastructure. Manufacturers must optimize resource utilization to meet demand while ensuring the safety and well-being of their workforce.

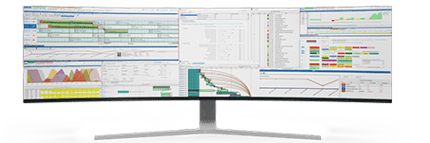
Integration with PlanetTogether and ERP, SCM, and MES Systems
To address these challenges, seamless integration between scheduling software like PlanetTogether and ERP, SCM, and MES systems is essential. Let's explore how such integration can enhance humanitarian logistics in medical manufacturing facilities:
Real-time Data Exchange: Integration enables the seamless flow of data between scheduling, ERP, SCM, and MES systems, providing stakeholders with real-time visibility into production processes, inventory levels, and supply chain dynamics. This allows for better decision-making and more accurate forecasting in the face of uncertainty.
Optimized Production Planning: By integrating scheduling software with ERP systems such as SAP, Oracle, or Microsoft Dynamics, manufacturers can optimize production planning based on demand forecasts, resource availability, and production capacities. This ensures efficient utilization of manufacturing assets while meeting regulatory requirements.
Streamlined Supply Chain Management: Integration with SCM platforms like Kinaxis or Aveva allows manufacturers to streamline supply chain processes, from procurement and inventory management to distribution and logistics. This enables agile response to supply chain disruptions and facilitates the timely delivery of medical supplies to affected areas.
Automated Workflows: MES integration automates workflows on the shop floor, reducing manual intervention and minimizing the risk of errors. This enhances production efficiency, quality control, and traceability, ensuring compliance with regulatory standards while maximizing output.
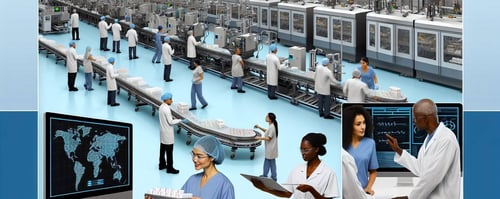
Optimizing Humanitarian Logistics with Integrated Scheduling
Imagine a scenario where a medical manufacturing facility is tasked with producing and distributing vaccines during a global pandemic. With demand fluctuating rapidly and supply chain disruptions looming, the facility leverages integrated scheduling solutions to navigate logistical challenges effectively:
- Real-time data exchange between PlanetTogether scheduling software and SAP ERP system enables dynamic production planning based on demand forecasts and inventory levels.
- Integration with Kinaxis SCM platform facilitates agile procurement and distribution of raw materials, ensuring uninterrupted supply chain operations.
- Automated workflows through MES integration streamline production processes, from batch manufacturing and quality assurance to packaging and labeling.
- Continuous monitoring and analytics provide stakeholders with actionable insights, allowing for proactive decision-making and rapid response to emerging challenges.
In medical manufacturing, where every dose of medication or medical device can make a difference between life and death, the importance of efficient humanitarian logistics cannot be overstated. By integrating scheduling software like PlanetTogether with leading ERP, SCM, and MES systems, manufacturers can overcome scheduling challenges and optimize their response to humanitarian crises.
Through real-time data exchange, optimized production planning, streamlined supply chain management, and automated workflows, integrated solutions empower medical manufacturing facilities to fulfill their humanitarian mission and save lives around the globe.
Are you ready to take your manufacturing operations to the next level? Contact us today to learn more about how PlanetTogether can help you achieve your goals and drive success in your industry.