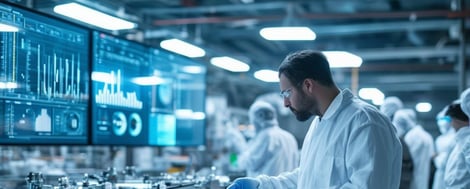
Navigating Demand Variability in Medical Manufacturing
The medical manufacturing sector operates in a dynamic environment where demand variability is a constant challenge. From the spike in requirements during global health crises to the need for precise inventory control of life-saving devices and pharmaceuticals, production schedulers must navigate a landscape of unpredictability with efficiency and precision.
One of the most transformative strategies for managing demand variability is integrating advanced production planning systems like PlanetTogether with enterprise resource planning (ERP) tools such as SAP, Oracle, Microsoft, Kinaxis, or Aveva. These integrations provide a unified, data-driven approach to scheduling, ensuring adaptability and resilience in the face of fluctuating demands.
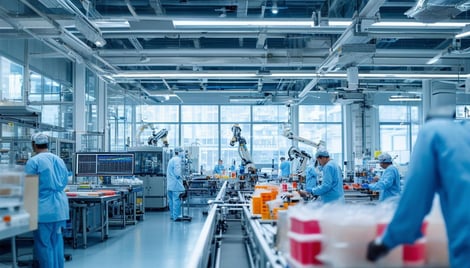
The Impact of Demand Variability in Medical Manufacturing
Demand variability in medical manufacturing arises from multiple factors:
Healthcare Crises: Sudden outbreaks or pandemics lead to unexpected surges in demand for specific products.
Regulatory Changes: Shifts in compliance requirements can alter production timelines and inventory needs.
Seasonal Variations: Demand for certain medical devices and consumables can vary based on seasons or planned healthcare initiatives.
Customer-Specific Needs: Customization and precision requirements add layers of complexity to forecasting and production planning.
For production schedulers, the ripple effects of demand variability can manifest as missed delivery deadlines, overstocked inventories, or idle production lines—all of which erode profitability and customer trust.
Leveraging Integrated Technologies to Tame Variability
PlanetTogether: A Production Scheduler’s Ally
PlanetTogether’s Advanced Planning and Scheduling (APS) software offers robust tools tailored for production environments grappling with variability. Its features include real-time visibility into production schedules, capacity planning, and what-if scenario analysis—all vital for adapting to sudden changes in demand.
The Power of Integration
When PlanetTogether is integrated with ERP systems such as SAP, Oracle, Microsoft, Kinaxis, or Aveva, it creates a seamless flow of data across the supply chain. This integration facilitates:
Accurate Forecasting: ERPs aggregate historical data and demand signals, which PlanetTogether can use for more precise scheduling.
Real-Time Adjustments: With up-to-date data from ERP systems, production schedules can be dynamically adjusted to accommodate shifts in demand.
Enhanced Collaboration: Integrations break down silos between departments, enabling a coordinated approach to demand management.
Scenario Planning: Combining PlanetTogether’s what-if analysis with ERP’s predictive analytics allows schedulers to proactively address potential disruptions.
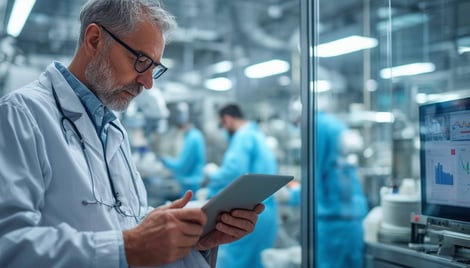
Strategies for Managing Demand Variability
1. Real-Time Data Integration
Medical manufacturing thrives on precision, and real-time data integration ensures that production schedules align with current demand signals. By leveraging PlanetTogether integrated with SAP or Microsoft, for example, schedulers gain immediate insights into inventory levels, supplier lead times, and production capacities.
2. Dynamic Scheduling
Static schedules are inadequate in a world of fluctuating demand. PlanetTogether’s dynamic scheduling capabilities, paired with Oracle’s supply chain analytics, enable schedulers to:
Optimize production runs based on available resources.
Minimize downtime by reallocating tasks in response to unexpected delays.
Balance workloads across multiple facilities.
3. Scenario Planning for Contingencies
Demand variability often comes with surprises. PlanetTogether’s scenario planning tools allow schedulers to simulate the impact of demand surges or supplier disruptions. When integrated with Kinaxis’ supply chain agility platform, these simulations provide actionable insights to maintain continuity without overextending resources.
4. Inventory Optimization
In medical manufacturing, overstocking can be as costly as understocking. By combining PlanetTogether’s inventory planning features with Aveva’s real-time asset monitoring, production schedulers can maintain optimal inventory levels that support demand variability without excessive carrying costs.
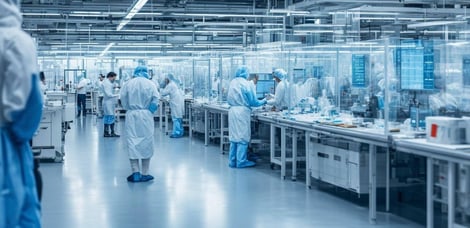
Key Benefits of Integration
For Production Schedulers:
Increased Agility: Rapidly adapt schedules to meet demand changes.
Data-Driven Decisions: Leverage integrated analytics for precise planning.
Resource Optimization: Balance workloads and minimize bottlenecks.
For Organizations:
Enhanced Efficiency: Streamlined processes reduce waste and improve productivity.
Better Customer Service: Timely deliveries enhance customer satisfaction and loyalty.
Cost Savings: Avoid penalties for late deliveries and reduce excess inventory costs.
Demand variability in medical manufacturing is a challenge that can be effectively managed with the right tools and strategies. Integrating PlanetTogether with leading ERP systems like SAP, Oracle, Microsoft, Kinaxis, or Aveva equips production schedulers with the agility, visibility, and precision needed to thrive in an unpredictable environment.
By embracing these technologies and strategies, production schedulers can not only mitigate the risks associated with demand variability but also turn it into a competitive advantage—ensuring that their facilities remain resilient, efficient, and customer-focused.
Are you ready to take your manufacturing operations to the next level? Contact us today to learn more about how PlanetTogether can help you achieve your goals and drive success in your industry.
LEAVE A COMMENT