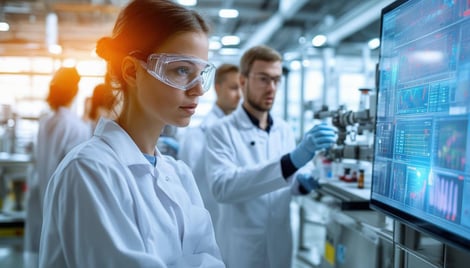
Mitigating Risk in Pharmaceutical Manufacturing
In the highly regulated and competitive pharmaceutical manufacturing industry, mitigating risk is more than just a best practice; it is a critical necessity. For purchasing managers, risk management spans various dimensions, including supply chain disruptions, regulatory compliance, quality assurance, and cost control.
Advanced planning and scheduling systems, like PlanetTogether, combined with enterprise resource planning (ERP) platforms such as SAP, Oracle, Microsoft, Kinaxis, or Aveva, are transforming how pharmaceutical manufacturers mitigate risk and enhance operational efficiency.
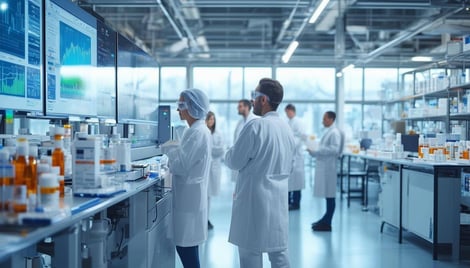
The Manufacturing Risk Landscape
Before looking into solutions, it’s essential to understand the breadth of risks that industrial manufacturing facilities face:
Supply Chain Volatility
Global supply chain disruptions, geopolitical instability, and fluctuating raw material costs can derail production schedules and inflate costs.
Operational Inefficiencies
Downtime, bottlenecks, and inefficient resource allocation lead to financial losses and diminished capacity utilization.
Compliance and Regulatory Risks
Non-compliance with safety, environmental, and quality standards can result in hefty fines and reputational damage.
Market and Demand Uncertainty
Shifts in consumer preferences and unpredictable demand can cause overproduction or underproduction, both of which are costly.
Technological Challenges
Fragmented systems and lack of interoperability hinder data-driven decision-making, leaving organizations vulnerable to disruptions.

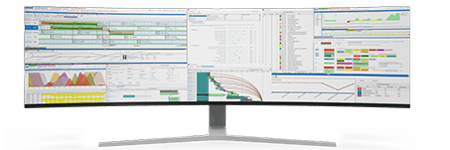
The Role of Technology in Risk Mitigation
Integrating advanced planning and scheduling tools like PlanetTogether with robust ERP systems such as SAP, Oracle, Microsoft, Kinaxis, or Aveva provides pharmaceutical manufacturers with powerful capabilities to identify, assess, and mitigate risks effectively.
1. Enhanced Supply Chain Visibility
A significant advantage of integrating PlanetTogether with ERP platforms is the ability to achieve end-to-end supply chain visibility. This visibility enables purchasing managers to:
Monitor Supplier Performance: Real-time data on supplier reliability, delivery times, and quality metrics helps identify potential risks before they escalate.
Predict Disruptions: Advanced analytics and predictive modeling forecast potential supply chain issues, allowing proactive mitigation strategies.
Optimize Inventory Management: Integration ensures optimal stock levels, reducing the risk of shortages or overstocking.
2. Improved Regulatory Compliance
Compliance risks can be mitigated through digital tools that streamline regulatory adherence:
Automated Documentation: Integrated systems automate the generation and storage of essential compliance documents, reducing the risk of errors or omissions.
Traceability and Auditing: PlanetTogether’s integration with ERP systems provides full traceability of raw materials and components, simplifying audits and inspections.
Real-Time Alerts: Configurable alerts notify purchasing managers of any deviations from compliance requirements, enabling timely corrective actions.
3. Quality Assurance through Data Integration
Quality risks are significantly reduced when data integration facilitates a seamless flow of information between departments and systems:
Supplier Qualification: Integrated platforms maintain comprehensive records of supplier certifications, audits, and performance metrics, ensuring only qualified suppliers are used.
Batch Tracking: Real-time batch tracking ensures that any quality issues are quickly traced back to the source, minimizing the impact on production.
Proactive Risk Assessment: Machine learning algorithms analyze historical data to identify patterns and risks associated with specific suppliers or materials.
4. Cost Optimization and Financial Risk Mitigation
Cost-related risks are minimized when purchasing decisions are informed by accurate, real-time data:
Dynamic Pricing Models: Integration enables the use of dynamic pricing models, which adjust procurement strategies based on market conditions.
Scenario Planning: PlanetTogether’s advanced scenario planning capabilities help assess the financial impact of various procurement strategies, ensuring cost-effective decisions.
Supplier Collaboration: Enhanced collaboration with suppliers fosters long-term partnerships, reducing costs associated with frequent supplier changes.
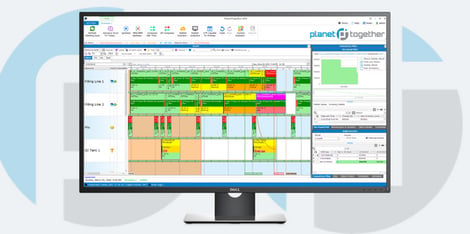
How Integration Mitigates Risks
The integration of PlanetTogether APS with ERP systems like SAP, Oracle, or Microsoft Dynamics creates a unified platform that fosters real-time visibility, enhances collaboration, and drives agility in decision-making. Here’s how this integration mitigates specific risks:
1. Reducing Supply Chain Disruptions
Integration allows for real-time synchronization between the APS and the ERP system, providing a comprehensive view of inventory levels, supplier performance, and material requirements. This enables plant managers to:
Anticipate Shortages: Forecast demand more accurately and align procurement schedules accordingly.
Enhance Agility: Adjust production plans dynamically in response to supply chain delays or shortages.
Strengthen Supplier Relationships: Leverage data insights to negotiate better contracts or identify alternative suppliers proactively.
2. Optimizing Production Schedules
PlanetTogether’s APS capabilities, when integrated with enterprise systems, enable intelligent scheduling that accounts for constraints like machine capacity, labor availability, and maintenance schedules. Benefits include:
Minimized Downtime: Proactively schedule maintenance and reduce unplanned breakdowns.
Improved Throughput: Identify and eliminate bottlenecks using real-time data analytics.
Enhanced Resource Utilization: Allocate resources optimally to maximize production efficiency.
3. Ensuring Compliance and Quality
Compliance risks are reduced through integration, as it ensures alignment between production plans and regulatory requirements. Features include:
Automated Traceability: Track raw materials and finished goods across the production lifecycle for compliance reporting.
Standardized Workflows: Enforce quality checks at every production stage to prevent costly rework.
Audit Readiness: Maintain a digital record of processes, ensuring preparedness for audits.
4. Responding to Market Shifts
Market fluctuations require manufacturers to pivot quickly, and integration facilitates this agility by:
Demand-Driven Planning: Use ERP data to align production schedules with sales forecasts.
Scenario Analysis: Simulate various market scenarios within PlanetTogether to identify the best course of action.
Inventory Optimization: Prevent stockouts or excess inventory through just-in-time production strategies.
5. Enhancing Data Interoperability
Fragmented systems lead to siloed decision-making. Integration resolves this by creating a unified data ecosystem, enabling:
Real-Time Decision-Making: Access accurate, up-to-date information across departments.
Collaborative Planning: Facilitate communication between production, procurement, and sales teams.
Predictive Insights: Use machine learning algorithms to predict potential disruptions and mitigate risks preemptively.
For purchasing managers in pharmaceutical manufacturing, mitigating risk is a multifaceted challenge that requires a combination of proactive strategies, advanced technology, and cross-functional collaboration. The integration of PlanetTogether with ERP systems like SAP, Oracle, Microsoft, Kinaxis, or Aveva provides a robust framework for addressing these challenges.
By enhancing supply chain visibility, ensuring regulatory compliance, improving quality assurance, and optimizing costs, this integration empowers purchasing managers to safeguard their operations against risks and drive sustained success in an ever-evolving industry.
Are you ready to take your manufacturing operations to the next level? Contact us today to learn more about how PlanetTogether can help you achieve your goals and drive success in your industry.
LEAVE A COMMENT