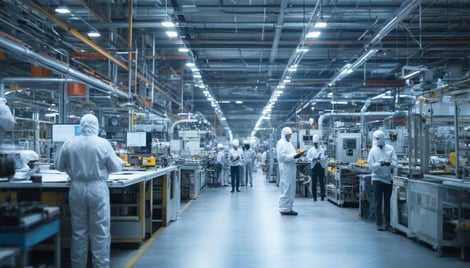
Minimizing Waste Through Better Production Scheduling: A Strategy for Medical Manufacturing
In medical manufacturing, precision is essential—not just in the products themselves but also in the processes that bring them to life. From complex regulatory requirements to the demand for high-quality output, minimizing waste isn't just a financial imperative; it is a critical factor for operational excellence and sustainability.
For Operations Directors, integrating cutting-edge solutions like PlanetTogether with enterprise systems such as SAP, Oracle, Microsoft Dynamics, Kinaxis, or Aveva presents a transformative opportunity to optimize production scheduling and reduce waste.
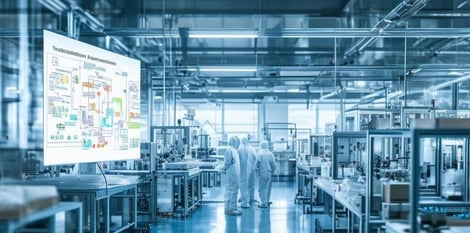
Understanding Waste in Medical Manufacturing
Before looking into solutions, it’s essential to understand the types of waste encountered in medical manufacturing:
Material Waste: Overproduction, expired materials, and damaged inventory contribute significantly to losses.
Time Waste: Inefficient scheduling leads to idle equipment, extended lead times, and delayed deliveries.
Energy Waste: Overrunning machines or redundant processes consume unnecessary energy.
Human Resources Waste: Misalignment in labor scheduling results in underutilized or overstressed teams.
Regulatory Non-Compliance: Errors in production or documentation can lead to rework or rejected batches.
Every piece of waste represents lost revenue, increased environmental impact, and a potential risk to the company’s reputation.
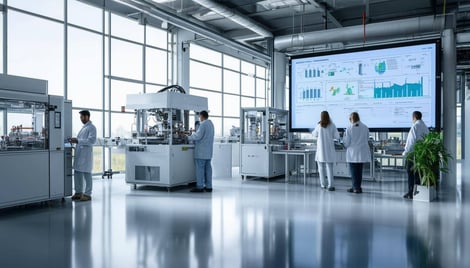
Production Scheduling in Waste Reduction
Production scheduling is the heartbeat of any manufacturing facility. For medical manufacturing, where precision and compliance are non-negotiable, optimizing this aspect can have a ripple effect across the entire operation. Effective production scheduling ensures:
Better Resource Utilization: By aligning production with demand forecasts, raw materials and labor are used more efficiently.
Minimized Inventory Waste: Avoiding overproduction reduces the risk of excess inventory becoming obsolete.
Shorter Lead Times: Streamlined processes lead to faster delivery times, enhancing customer satisfaction.
Improved Quality: Proper scheduling minimizes the likelihood of errors and rework, improving compliance rates.

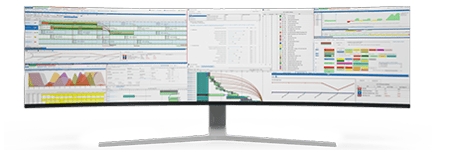
PlanetTogether: A Game-Changer in Production Scheduling
PlanetTogether, a leading advanced planning and scheduling (APS) tool, is designed to tackle the unique challenges of medical manufacturing. When integrated with ERP systems like SAP, Oracle, Microsoft Dynamics, Kinaxis, or Aveva, it becomes a powerful ally for waste reduction. Here’s how:
Enhanced Visibility and Real-Time Data
Integration between PlanetTogether and ERP systems ensures seamless data flow, enabling real-time visibility across the production cycle. For example:
SAP Integration: Combines production data with supply chain insights to identify bottlenecks and eliminate redundancies.
Microsoft Dynamics: Leverages real-time demand forecasts to adjust schedules dynamically.
This holistic view allows Operations Directors to anticipate and address inefficiencies before they escalate into waste.
Scenario Planning and What-If Analysis
PlanetTogether excels in enabling scenario planning, allowing decision-makers to simulate various production strategies. By integrating with tools like Kinaxis, which specializes in supply chain optimization, medical manufacturers can evaluate:
The impact of raw material shortages.
The benefits of running smaller, more frequent batches to minimize inventory waste.
Adjustments needed to meet sudden spikes in demand.
This capability ensures that production decisions are both data-driven and agile, reducing the likelihood of overproduction or downtime.
Optimized Resource Allocation
With PlanetTogether, resources—including machines, labor, and materials—are allocated based on priority and availability. When integrated with Oracle’s robust resource management modules, the tool can:
Automate labor scheduling to match production demands.
Synchronize material orders with production timelines to avoid shortages or surpluses.
By aligning resources with precise scheduling needs, waste is significantly reduced.
Compliance and Quality Assurance
Integration with systems like Aveva, which focuses on engineering and operational efficiency, ensures that every production schedule adheres to stringent regulatory requirements. For instance:
Batch Traceability: PlanetTogether tracks batches to ensure that no expired or non-compliant materials are used.
Production Logs: Automated documentation reduces errors, ensuring that compliance is maintained without wasting time or resources.
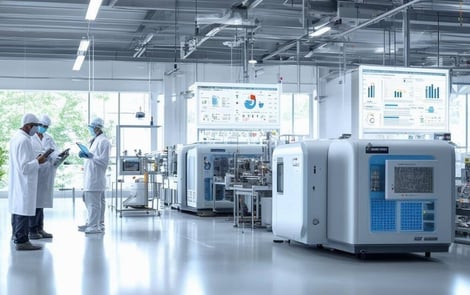
Key Takeaways for Operations Directors
Integrate for Success: PlanetTogether’s integration with ERP systems such as SAP, Oracle, Microsoft Dynamics, Kinaxis, or Aveva provides a comprehensive solution to production inefficiencies.
Focus on Real-Time Data: Utilize real-time visibility and analytics to make proactive, informed decisions.
Embrace Agility: Scenario planning and dynamic scheduling allow for rapid adaptation to changing market demands.
Prioritize Compliance: Ensure every production plan meets regulatory standards to avoid costly errors and rework.
For Operations Directors in medical manufacturing, minimizing waste through better production scheduling is not merely an operational goal; it is a strategic imperative. Tools like PlanetTogether, when integrated with powerful ERP systems, provide the visibility, agility, and precision needed to drive waste reduction across the board. By adopting these technologies, medical manufacturers can achieve operational excellence, ensure compliance, and contribute to a more sustainable industry.
Are you ready to take your manufacturing operations to the next level? Contact us today to learn more about how PlanetTogether and integrated scheduling solutions can help you achieve your sustainability goals and drive success in the medical industry.