Integrating Lean Principles
In the realm of chemical manufacturing, where precision and efficiency are vital, the integration of Lean principles into scheduling processes is not just an option but a necessity. Operations Directors overseeing such facilities understand the intricate dance between production schedules, resource allocation, and maintaining profitability.
With the advent of advanced scheduling tools like PlanetTogether and the integration possibilities with ERP, SCM, and MES systems such as SAP, Oracle, Microsoft, Kinaxis, and Aveva, optimizing scheduling practices to align with Lean principles becomes more attainable than ever before.
In this blog, we'll look into the significance of integrating Lean principles in scheduling within chemical manufacturing facilities, exploring the benefits, challenges, and strategies for successful implementation.
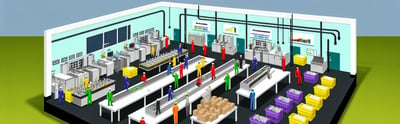
Lean Principles in Scheduling
At its core, Lean manufacturing aims to eliminate waste and maximize value through continuous improvement. When applied to scheduling, Lean principles emphasize efficiency, flexibility, and responsiveness to customer demand while minimizing inventory and production downtime.
Just-in-Time (JIT) Production: JIT principles advocate for producing goods only as needed, reducing excess inventory and associated costs. Scheduling in alignment with JIT involves precise timing of production runs to meet customer demand without overproduction.
Kanban Systems: Kanban systems help streamline material flow by signaling replenishment needs based on actual consumption. Integrating Kanban principles into scheduling ensures that production orders are initiated only when necessary, preventing excess inventory buildup.
Continuous Improvement: Scheduling processes should be continuously evaluated and refined to eliminate bottlenecks, reduce setup times, and improve overall efficiency. Lean scheduling involves fostering a culture of continuous improvement, where feedback from the shop floor informs iterative adjustments to scheduling practices.

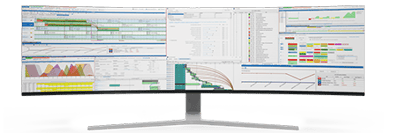
Integration of Lean Principles with Advanced Scheduling Tools
Advanced scheduling tools such as PlanetTogether offer capabilities to optimize production schedules based on various constraints and objectives. When integrated with ERP, SCM, and MES systems, these tools become even more powerful in aligning scheduling practices with Lean principles.
Real-Time Data Integration: Integration with ERP systems like SAP or Oracle enables real-time access to crucial data such as customer orders, inventory levels, and production capacities. By leveraging up-to-date information, schedulers can make informed decisions to minimize waste and maximize resource utilization.
Demand Forecasting: Integration with SCM systems allows for seamless incorporation of demand forecasts into scheduling algorithms. By accurately predicting future demand, scheduling decisions can be made proactively to avoid production shortages or excess inventory.
Shop Floor Visibility: MES integration provides visibility into shop floor activities, including machine status, production progress, and quality control metrics. This real-time feedback loop enables schedulers to adjust plans on the fly to address unforeseen issues and optimize production flow.
Challenges and Considerations
While the integration of Lean principles in scheduling offers substantial benefits, it's not without its challenges. Some common considerations include:
Change Management: Implementing Lean scheduling practices requires buy-in from all levels of the organization. Operations Directors must effectively communicate the rationale behind changes and provide training to ensure smooth adoption.
Data Integrity: Integration between scheduling tools and existing systems relies on accurate and consistent data. Operations Directors must invest in data quality initiatives to ensure the reliability of information used for scheduling decisions.
Complexity: Chemical manufacturing processes can be highly complex, with multiple dependencies and constraints. Integrating Lean principles into scheduling may require sophisticated algorithms and modeling techniques to account for these complexities effectively.
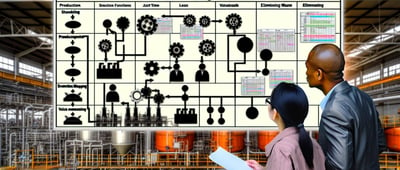
Strategies for Successful Implementation
To successfully integrate Lean principles in scheduling, Operations Directors can adopt the following strategies:
Pilot Projects: Start with small-scale pilot projects to test scheduling improvements before implementing them across the entire facility. Pilot projects allow for iterative refinement and minimize the risk of disruptions to ongoing operations.
Cross-Functional Collaboration: Foster collaboration between production, logistics, and engineering teams to gain diverse perspectives and identify opportunities for improvement. Cross-functional teams can work together to address systemic issues and drive continuous improvement initiatives.
Performance Metrics: Establish key performance indicators (KPIs) to measure the effectiveness of Lean scheduling initiatives. Metrics such as on-time delivery, inventory turnover, and schedule adherence can provide valuable insights into the impact of scheduling improvements on overall performance.
Chemical manufacturing facilities must continuously seek ways to optimize operational efficiency and maximize value for customers. Integrating Lean principles in scheduling offers a pathway to achieve these objectives by minimizing waste, improving resource utilization, and enhancing responsiveness to customer demand.
With advanced scheduling tools like PlanetTogether and seamless integration with ERP, SCM, and MES systems, Operations Directors have the tools and capabilities to transform scheduling practices and drive sustainable improvements in performance and profitability.
By embracing Lean principles and leveraging technology effectively, chemical manufacturing facilities can position themselves for long-term success in a rapidly evolving industry landscape.
Are you ready to take your manufacturing operations to the next level? Contact us today to learn more about how PlanetTogether and integrated scheduling solutions can help you achieve your sustainability goals and drive success in the chemical industry.
LEAVE A COMMENT