Maximizing Margins: The Power of Data-Driven Maintenance
Production planners face the constant challenge of optimizing resources, reducing downtime, and maximizing margins in today's hyper-competitive industrial manufacturing. One of the most potent tools in their arsenal is data-driven maintenance. By leveraging insights gleaned from integrated systems like PlanetTogether with leading ERP solutions such as SAP, Oracle, Microsoft, Kinaxis, or Aveva, production planners can revolutionize their maintenance strategies and drive significant improvements in profitability.
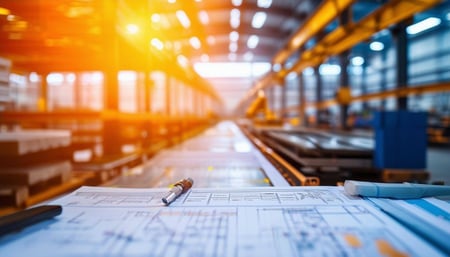
The Role of Production Planning in Industrial Manufacturing
Production planning is the backbone of any industrial manufacturing facility. It involves coordinating various resources—materials, machines, manpower, and time—to ensure efficient and timely production. However, traditional approaches to maintenance have often been reactive, leading to costly downtime, unexpected failures, and reduced productivity. In contrast, data-driven maintenance adopts a proactive approach, leveraging real-time data and predictive analytics to optimize equipment performance and minimize disruptions.

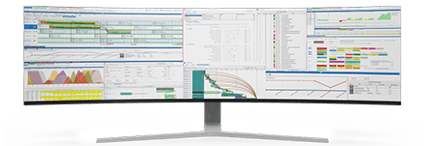
Integration between PlanetTogether and ERP Systems
PlanetTogether is a powerful production planning and scheduling software that enables manufacturers to optimize their production processes. By integrating PlanetTogether with leading ERP systems such as SAP, Oracle, Microsoft, Kinaxis, or Aveva, production planners gain access to a wealth of data that can be leveraged to enhance maintenance strategies.
For example, integrating PlanetTogether with SAP ERP allows production planners to seamlessly synchronize production schedules with maintenance activities. By analyzing historical production data and predictive maintenance algorithms, planners can identify optimal maintenance intervals, schedule preventive maintenance tasks during downtime, and minimize the risk of unplanned breakdowns.
Similarly, integration with Oracle ERP provides production planners with real-time visibility into inventory levels, equipment status, and production schedules. By leveraging this data, planners can identify maintenance requirements, prioritize tasks based on criticality and resource availability, and optimize maintenance schedules to minimize production disruptions.
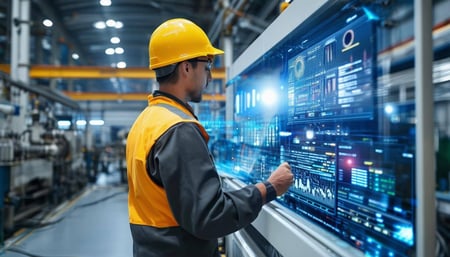
The Benefits of Data-Driven Maintenance
Improved Equipment Reliability: By proactively monitoring equipment health and performance metrics, production planners can detect potential issues before they escalate into costly failures. Predictive maintenance algorithms can analyze data from sensors, IoT devices, and historical maintenance records to forecast equipment failures and schedule preemptive repairs.
Reduced Downtime: Unplanned downtime can wreak havoc on production schedules and profitability. Data-driven maintenance allows production planners to schedule maintenance activities during planned downtime periods, minimizing the impact on production throughput. By optimizing maintenance schedules and prioritizing critical tasks, planners can reduce the frequency and duration of unplanned shutdowns.
Optimized Spare Parts Inventory: Inventory management is a critical aspect of maintenance operations. By integrating PlanetTogether with ERP systems, production planners can optimize spare parts inventory levels based on historical usage patterns, lead times, and criticality. Advanced inventory forecasting algorithms can predict future demand, ensuring that the right parts are available when needed without tying up excess capital in inventory stockpiles.
Enhanced Asset Performance: Maximizing the lifespan and performance of capital assets is essential for long-term profitability. Data-driven maintenance enables production planners to track key performance indicators (KPIs) such as equipment uptime, mean time between failures (MTBF), and overall equipment effectiveness (OEE). By continuously monitoring and analyzing these metrics, planners can identify opportunities for performance improvement, optimize maintenance strategies, and maximize asset ROI.
Data-driven maintenance is a powerful tool for enhancing margins and improving competitiveness in industrial manufacturing. By integrating systems like PlanetTogether with leading ERP solutions such as SAP, Oracle, Microsoft, Kinaxis, or Aveva, production planners can unlock the full potential of their data to optimize maintenance strategies, minimize downtime, and maximize profitability.
As we look to the future, the adoption of advanced analytics, IoT sensors, and AI-driven predictive maintenance will continue to drive innovation in maintenance practices, enabling manufacturers to stay ahead of the curve and thrive in an increasingly competitive marketplace.
Are you ready to take your manufacturing operations to the next level? Contact us today to learn more about how PlanetTogether can help you achieve your goals and drive success in your industry.