Production schedulers play a crucial role in ensuring that operations run smoothly, meeting demand while optimizing resources. With the complexities of the pharmaceutical industry, integrating lean principles into capacity management becomes essential for maintaining competitiveness and meeting regulatory requirements.
In this blog, we'll explore how production schedulers can leverage lean principles in capacity management, with a focus on integrating advanced planning and scheduling (APS) software like PlanetTogether with ERP, SCM, and MES systems such as SAP, Oracle, Microsoft, Kinaxis, and Aveva.
Understanding Lean Principles in Capacity Management
Lean principles revolve around eliminating waste, optimizing processes, and continuously improving efficiency. When applied to capacity management in pharmaceutical manufacturing, lean principles aim to streamline operations, reduce lead times, and enhance overall productivity. Let's look into some key lean principles and how they can be integrated into capacity management:
Value Stream Mapping (VSM):
Value stream mapping involves analyzing the entire production process to identify value-adding activities and eliminate non-value-adding ones. For production schedulers, this means mapping out the entire production workflow, from raw material procurement to finished product delivery. By identifying bottlenecks, redundancies, and inefficiencies, production schedulers can optimize capacity utilization and minimize resource wastage.
Just-in-Time (JIT) Production:
Just-in-time production involves producing goods only when needed, thereby reducing inventory levels and minimizing storage costs. Production schedulers can apply JIT principles by synchronizing production schedules with customer demand forecasts. By leveraging APS software like PlanetTogether integrated with ERP systems such as SAP or Oracle, production schedulers can dynamically adjust production schedules in real-time based on demand fluctuations, ensuring optimal resource utilization and minimizing inventory holding costs.
Continuous Improvement:
Continuous improvement is at the heart of lean principles, emphasizing the ongoing effort to identify and eliminate waste. Production schedulers can foster a culture of continuous improvement by regularly analyzing production data, soliciting feedback from frontline workers, and implementing process enhancements. By leveraging MES systems like Aveva integrated with APS software, production schedulers can monitor Key Performance Indicators (KPIs) in real-time, identify areas for improvement, and implement corrective actions promptly.
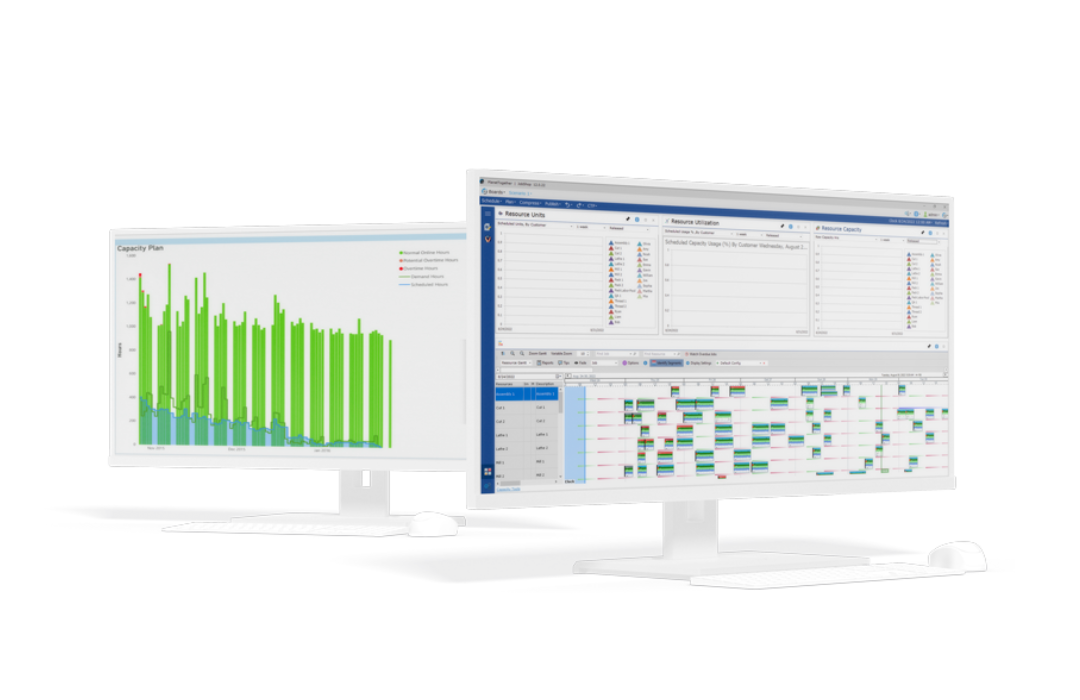
Integration of PlanetTogether with ERP, SCM, and MES Systems
To effectively implement lean principles in capacity management, seamless integration between APS software like PlanetTogether and ERP, SCM, and MES systems is crucial. Let's explore how such integration can enhance efficiency for production schedulers:
Integration with SAP:
Integration between PlanetTogether and SAP allows production schedulers to synchronize production schedules with SAP's Material Requirements Planning (MRP) module. By aligning production plans with material availability and procurement schedules, production schedulers can optimize inventory levels, reduce stockouts, and minimize carrying costs.
Integration with Oracle:
Integrating PlanetTogether with Oracle's Supply Chain Management (SCM) suite enables production schedulers to streamline order fulfillment processes. By synchronizing production schedules with Oracle's Order Management and Inventory modules, production schedulers can ensure timely delivery of products while minimizing lead times and optimizing resource allocation.
Integration with Microsoft Dynamics:
Integration between PlanetTogether and Microsoft Dynamics enables production schedulers to leverage advanced analytics for capacity planning. By integrating production schedules with Microsoft Dynamics' Power BI platform, production schedulers can gain actionable insights into production performance, identify trends, and make data-driven decisions to enhance efficiency.
Integration with Kinaxis:
Integrating PlanetTogether with Kinaxis RapidResponse allows production schedulers to achieve end-to-end supply chain visibility. By synchronizing production schedules with Kinaxis' Control Tower dashboard, production schedulers can monitor production progress in real-time, anticipate potential disruptions, and proactively adjust capacity plans to mitigate risks.
Integration with Aveva:
Integration between PlanetTogether and Aveva MES enables production schedulers to achieve real-time manufacturing visibility. By synchronizing production schedules with Aveva's Manufacturing Execution System, production schedulers can monitor shop floor activities, track produ ction progress, and ensure compliance with regulatory requirements.
In today's competitive pharmaceutical manufacturing landscape, efficiency is vital for success. Production schedulers play a pivotal role in optimizing capacity utilization while meeting demand fluctuations and regulatory requirements.
By embracing lean principles in capacity management and leveraging advanced planning and scheduling (APS) software like PlanetTogether integrated with ERP, SCM, and MES systems such as SAP, Oracle, Microsoft, Kinaxis, and Aveva, production schedulers can streamline operations, reduce lead times, and enhance overall productivity.
With seamless integration between APS software and enterprise systems, production schedulers can drive continuous improvement, achieve operational excellence, and maintain a competitive edge in the dynamic pharmaceutical industry.
Request a Free Demo Today!
LEAVE A COMMENT