Zero-Based Scheduling for Cost Optimization
As a Plant Manager, you're constantly seeking ways to streamline processes, reduce costs, and improve overall productivity while maintaining compliance with stringent regulations. One approach gaining traction in the industry is zero-based scheduling (ZBS), a methodology that re-evaluates every aspect of production planning to optimize resource utilization and minimize waste.
In this blog, we'll explore the concept of ZBS and its integration with advanced scheduling software like PlanetTogether, alongside ERP, SCM, and MES systems such as SAP, Oracle, Microsoft, Kinaxis, and Aveva, to achieve cost optimization in pharmaceutical manufacturing.
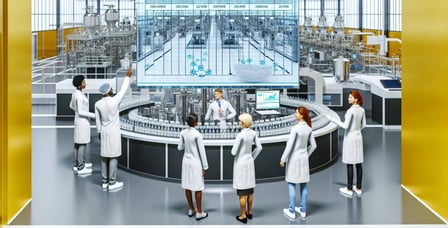
Zero-Based Scheduling (ZBS)
Zero-based scheduling (ZBS) is a methodology that differs from traditional scheduling approaches by requiring a complete reassessment of production plans and resource allocation from scratch, rather than simply adjusting existing schedules. The core principle behind ZBS is to question every assumption and allocate resources based on current needs and priorities, rather than historical data or preconceived notions.
Key Elements of ZBS
Resource Optimization: ZBS emphasizes the efficient use of resources, including raw materials, equipment, labor, and time. By analyzing production requirements and capacity constraints in real-time, ZBS enables Plant Managers to allocate resources effectively, minimizing idle time and maximizing throughput.
Flexibility and Adaptability: ZBS recognizes the dynamic nature of manufacturing operations and allows for quick adjustments in response to changing demand, supply chain disruptions, or unforeseen events. This flexibility ensures that production remains agile and responsive to market conditions.
Continuous Improvement: ZBS fosters a culture of continuous improvement by encouraging regular reviews of production processes and performance metrics. By identifying areas for optimization and implementing corrective actions, Plant Managers can drive efficiency gains over time.
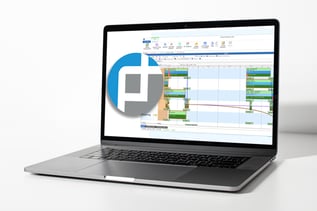
Integration of ZBS with Advanced Scheduling Software
While ZBS offers significant benefits for pharmaceutical manufacturers, its successful implementation requires advanced scheduling software capable of handling complex production environments and integrating seamlessly with other enterprise systems.
One such solution is PlanetTogether, a leading provider of production planning and scheduling software. PlanetTogether's advanced algorithms and intuitive interface make it an ideal tool for implementing ZBS in pharmaceutical manufacturing facilities.
Integration with ERP Systems
Integrating PlanetTogether with ERP systems like SAP, Oracle, or Microsoft Dynamics enables Plant Managers to leverage real-time data on inventory levels, sales orders, and production forecasts to inform scheduling decisions. By synchronizing information between these systems, manufacturers can ensure that production plans align with business objectives and resource availability.
Integration with SCM Systems
Supply chain management (SCM) systems play a critical role in pharmaceutical manufacturing by optimizing procurement, warehousing, and distribution processes. By integrating PlanetTogether with SCM systems like Kinaxis or Aveva, Plant Managers can improve visibility across the supply chain and mitigate risks associated with material shortages or delivery delays. This integration allows for seamless coordination between production schedules and procurement activities, ensuring that the right materials are available when needed.
Integration with MES Systems
Manufacturing execution systems (MES) provide real-time visibility into shop floor operations, including equipment status, production performance, and quality control metrics. By integrating PlanetTogether with MES systems, Plant Managers can monitor production progress in real-time and identify bottlenecks or inefficiencies that may impact scheduling decisions. This integration enables proactive problem-solving and optimization of production processes to maximize throughput and minimize downtime.
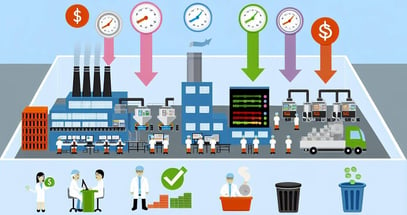
Benefits of Integrated ZBS Approach
Improved Decision-Making: Integration between PlanetTogether and ERP, SCM, and MES systems provides Plant Managers with a comprehensive view of production operations, enabling informed decision-making based on real-time data and analytics.
Optimized Resource Utilization: By adopting a ZBS approach, supported by advanced scheduling software and integrated enterprise systems, pharmaceutical manufacturers can optimize resource utilization across the entire production process, reducing waste and improving efficiency.
Enhanced Agility and Responsiveness: Integration enables manufacturers to quickly adapt to changing market conditions or unforeseen events, ensuring that production remains agile and responsive to customer demands.
Cost Optimization: Zero-based scheduling facilitates cost optimization by identifying opportunities to streamline processes, minimize downtime, and reduce inventory carrying costs. By aligning production plans with actual demand and resource availability, manufacturers can achieve significant cost savings without sacrificing quality or compliance.
In pharmaceutical manufacturing landscape, achieving cost optimization requires a holistic approach that combines zero-based scheduling (ZBS) with advanced scheduling software and integrated enterprise systems. By adopting a ZBS approach and integrating solutions like PlanetTogether with ERP, SCM, and MES systems, Plant Managers can optimize resource utilization, enhance agility, and drive continuous improvement in production operations.
The successful implementation of an integrated ZBS approach enables pharmaceutical manufacturers to achieve cost optimization, improve efficiency, and maintain compliance with regulatory requirements, ultimately ensuring their long-term success in a dynamic and demanding industry.
Are you ready to take your manufacturing operations to the next level? Contact us today to learn more about how PlanetTogether can help you achieve your goals and drive success in your industry.
LEAVE A COMMENT