Dynamic Supplier Collaboration
With the increasing demand for innovative products and sustainable practices, production planners are tasked with the challenge of optimizing operations while ensuring seamless collaboration with suppliers.
In this blog, we'll explore the concept of dynamic supplier collaboration and how integrating advanced planning tools like PlanetTogether with leading ERP, SCM, and MES systems can revolutionize efficiency in chemical manufacturing.
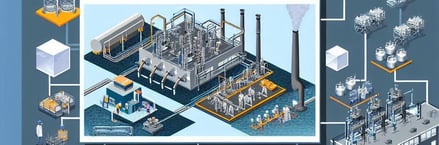
Understanding Dynamic Supplier Collaboration
Dynamic supplier collaboration goes beyond traditional supply chain management. It involves real-time communication, data sharing, and collaborative decision-making between manufacturers and suppliers. This proactive approach enables quicker response times to market changes, reduces inventory costs, minimizes supply chain disruptions, and ultimately enhances customer satisfaction.
Key Components of Dynamic Supplier Collaboration:
Real-time Data Exchange: Timely access to accurate data is crucial for effective collaboration. By integrating planning software like PlanetTogether with ERP systems such as SAP, Oracle, or Microsoft Dynamics, production planners can synchronize information on inventory levels, production schedules, and demand forecasts in real-time. This enables suppliers to align their production and delivery schedules accordingly, reducing the risk of stockouts or excess inventory.
Demand Forecasting and Planning: Anticipating customer demand is a complex yet essential aspect of production planning. Advanced planning tools leverage historical data, market trends, and predictive analytics to generate accurate demand forecasts. By sharing these forecasts with suppliers and integrating them into their production planning processes, manufacturers can optimize inventory levels, minimize lead times, and ensure on-time delivery of raw materials.
Collaborative Capacity Planning: Effective capacity planning requires collaboration between manufacturers and suppliers to ensure that production capacities align with demand fluctuations. Integrated planning systems enable real-time visibility into capacity constraints and production schedules across the entire supply chain. This allows for proactive adjustments to production plans, allocation of resources, and identification of alternative suppliers in case of capacity shortages or production disruptions.
Quality Management and Compliance: Maintaining product quality and compliance with regulatory standards is paramount in the chemical industry. Dynamic supplier collaboration involves establishing clear quality specifications, conducting regular audits, and sharing performance metrics with suppliers. Integration between planning software and MES systems facilitates traceability, quality control, and compliance monitoring throughout the production process, ensuring consistency and safety in product delivery.
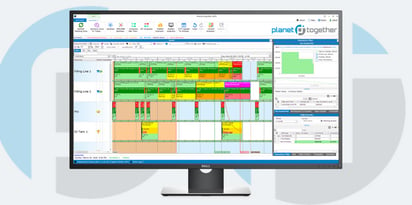
Benefits of Integration between PlanetTogether and ERP, SCM, and MES Systems
Streamlined Communication: Integration eliminates the need for manual data entry and communication, reducing errors and delays in information sharing between systems. Production planners can access comprehensive insights and collaborate with suppliers seamlessly within a unified platform.
Enhanced Visibility and Transparency: By consolidating data from multiple systems, integration provides end-to-end visibility into the supply chain, from raw material procurement to product delivery. This transparency enables proactive decision-making, risk mitigation, and performance tracking across all stages of production.
Optimized Inventory Management: Dynamic supplier collaboration facilitates inventory optimization by aligning supply with demand in real-time. Integration enables automatic replenishment triggers, safety stock calculations, and just-in-time inventory management, reducing carrying costs and improving inventory turnover.
Agile Response to Market Changes: In today's volatile market environment, agility is key to staying competitive. Integrated planning systems enable rapid scenario analysis, what-if simulations, and dynamic adjustments to production plans in response to changing market conditions or unforeseen disruptions.
Continuous Improvement: Integration fosters a culture of continuous improvement by providing actionable insights and performance metrics for evaluation. Production planners can identify areas for optimization, collaborate with suppliers on process improvements, and drive efficiency gains throughout the supply chain.
Dynamic supplier collaboration is a game-changer for chemical manufacturers seeking to optimize operations, reduce costs, and enhance customer satisfaction. By integrating advanced planning tools like PlanetTogether with leading ERP, SCM, and MES systems, production planners can unlock the full potential of their supply chain.
Embracing collaboration, transparency, and agility enables manufacturers to stay ahead in today's competitive landscape while driving sustainable growth and innovation. Are you ready to take your manufacturing operations to the next level? Contact us today to learn more about how PlanetTogether can help you achieve your goals and drive success in your industry.
LEAVE A COMMENT