Data-Driven Demand Forecasting
In today's world, where demand patterns can be as unpredictable as they are sporadic, medical manufacturing facilities face unique challenges in ensuring their production processes are optimized to meet fluctuating demands. Plant Managers in these facilities are tasked with the responsibility of maintaining efficient operations while keeping costs under control and delivering high-quality products on time. However, achieving these goals can be a daunting task, especially when faced with sporadic demand patterns.
Fortunately, advancements in technology, particularly in the realm of Artificial Intelligence (AI) and data analytics, have provided innovative solutions to help Plant Managers tackle these challenges head-on.
By leveraging AI algorithms for demand forecasting, coupled with seamless integration between advanced planning and scheduling (APS) software like PlanetTogether and Enterprise Resource Planning (ERP), Supply Chain Management (SCM), and Manufacturing Execution Systems (MES) platforms such as SAP, Oracle, Microsoft, Kinaxis, and Aveva, medical manufacturing facilities can enhance their operational efficiency and adaptability to sporadic demand patterns.
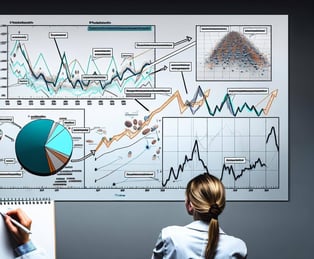
Sporadic Demand Patterns
Unlike steady or predictable demand, sporadic demand is characterized by irregular fluctuations in the need for a product or service. In the medical manufacturing industry, this could result from various factors such as seasonal trends, changes in healthcare regulations, new product launches, or unexpected shifts in consumer preferences.
For Plant Managers, managing sporadic demand poses several challenges, including:
- Inventory Management: Balancing inventory levels to meet fluctuating demand without overstocking or stockouts.
- Production Planning: Optimizing production schedules to accommodate sudden changes in demand while minimizing downtime and maximizing resource utilization.
- Supply Chain Coordination: Ensuring seamless coordination with suppliers and distributors to respond swiftly to changes in demand.
- Cost Efficiency: Minimizing costs associated with excess inventory, overtime, rush orders, and inefficient resource allocation.
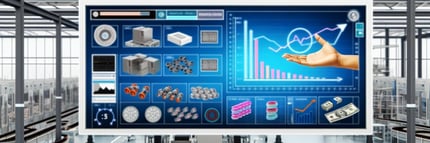
The Role of Data-Driven Demand Forecasting
Traditionally, demand forecasting relied on historical data and manual forecasting techniques, which often fell short in accurately predicting sporadic demand patterns. However, with the advent of AI and machine learning algorithms, Plant Managers now have access to more sophisticated tools capable of analyzing vast amounts of data in real-time to generate accurate demand forecasts.
Data-driven demand forecasting involves the use of AI algorithms to analyze various data sources, including historical sales data, market trends, seasonal patterns, competitor analysis, and even external factors like weather forecasts or geopolitical events. By identifying patterns and correlations within this data, AI algorithms can generate more accurate demand forecasts, even for products with sporadic demand patterns.

Integration with Advanced Planning and Scheduling (APS) Software
To effectively translate demand forecasts into actionable production plans, Plant Managers can leverage advanced planning and scheduling (APS) software like PlanetTogether. APS software utilizes AI-driven optimization algorithms to create optimal production schedules based on demand forecasts, resource constraints, and production objectives.
The integration between PlanetTogether and ERP, SCM, and MES systems is crucial for streamlining data flow and ensuring synchronization between planning, execution, and monitoring stages of the production process. By seamlessly exchanging data between these systems, Plant Managers can achieve greater visibility and control over their operations, enabling them to respond swiftly to changes in demand and optimize resource allocation in real-time.
Benefits of Integrated AI-Driven Solutions
The integration of AI-driven demand forecasting with APS and ERP systems offers several benefits for medical manufacturing facilities:
- Improved Forecast Accuracy: AI algorithms can analyze vast amounts of data to generate more accurate demand forecasts, reducing the risk of stockouts or excess inventory.
- Optimized Production Schedules: APS software can generate optimal production schedules based on demand forecasts, resource availability, and production constraints, maximizing efficiency and minimizing downtime.
- Enhanced Resource Utilization: By synchronizing planning and execution processes, Plant Managers can allocate resources more effectively, reducing idle time and optimizing workforce productivity.
- Real-Time Adaptability: Integrated systems enable real-time monitoring of production processes, allowing Plant Managers to adjust schedules, allocate resources, and respond to changes in demand as they occur.
- Cost Savings: By minimizing inventory holding costs, reducing overtime expenses, and optimizing resource utilization, integrated AI-driven solutions can help medical manufacturing facilities achieve significant cost savings in their operations.
Data-driven demand forecasting, coupled with integration between APS software like PlanetTogether and ERP, SCM, and MES systems, offers a powerful solution for medical manufacturing facilities seeking to optimize their operations in the face of sporadic demand patterns.
By leveraging AI algorithms to generate accurate demand forecasts and seamlessly integrating planning and execution processes, Plant Managers can enhance efficiency, minimize costs, and improve responsiveness to changing market dynamics.
As the medical manufacturing industry continues to evolve, embracing these technologies will be essential for staying competitive and meeting the demands of an increasingly dynamic market landscape. Are you ready to take your manufacturing operations to the next level? Contact us today to learn more about how PlanetTogether can help you achieve your goals and drive success in your industry.
LEAVE A COMMENT