Digital Supply Chain Networks for Responsive Operations
In the rapidly evolving business landscape, agility is the name of the game, especially in the food and beverage manufacturing industry. As a Supply Chain Manager, you're likely well aware of the challenges that come with ensuring seamless operations while meeting dynamic consumer demands, regulatory requirements, and market fluctuations. In this digital age, the integration of advanced technologies and systems has become paramount to achieving agility and responsiveness throughout the supply chain.
In this blog, we'll explore the significance of integrating digital supply chain networks, with a focus on the integration between PlanetTogether and leading ERP, SCM, and MES systems like SAP, Oracle, Microsoft, Kinaxis, Aveva, and others.
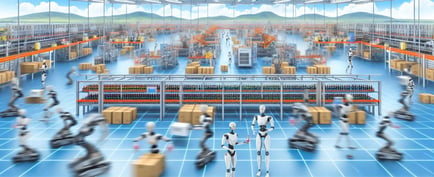
The Need for Agility
In the food and beverage industry, agility isn't just a buzzword; it's a necessity. Consumer preferences are constantly changing, regulatory standards are becoming more stringent, and global events can disrupt supply chains overnight. To thrive in this environment, businesses must be agile and responsive. This means having the ability to adapt quickly to changes in demand, supply, and market conditions while maintaining operational efficiency and product quality.
The Role of Digital Supply Chain Networks
Digital supply chain networks leverage technology to connect various stakeholders, processes, and systems across the entire supply chain. These networks enable real-time visibility, collaboration, and decision-making, empowering organizations to anticipate and respond to disruptions proactively. By integrating disparate systems and data sources, digital supply chain networks break down silos and create a unified platform for end-to-end supply chain management.
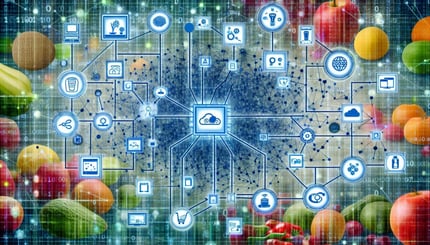
The Power of Integration
Integration is the cornerstone of a seamless and efficient supply chain. By connecting planning, execution, and monitoring functions, integration enables data to flow freely across the organization, eliminating manual tasks, reducing errors, and speeding up decision-making. When it comes to integrating digital supply chain networks, compatibility between different software solutions is crucial.
PlanetTogether: A Key Player in Supply Chain Planning
PlanetTogether is a leading provider of advanced planning and scheduling software, designed to optimize production planning and scheduling processes. By utilizing advanced algorithms and analytics, PlanetTogether enables organizations to create accurate production plans, optimize resource utilization, and minimize lead times. However, to fully leverage the capabilities of PlanetTogether, integration with other systems such as ERP, SCM, and MES is essential.
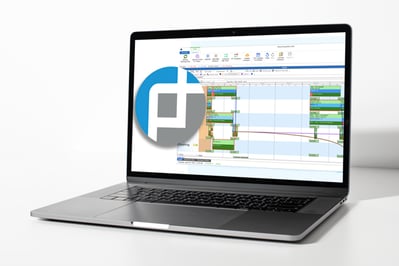
Integration with Leading ERP, SCM, and MES Systems
When it comes to integrating PlanetTogether with other enterprise systems, several options are available, including SAP, Oracle, Microsoft, Kinaxis, Aveva, and others. Each of these systems offers unique features and functionalities, catering to specific business needs and preferences. By integrating PlanetTogether with these systems, organizations can achieve greater visibility, efficiency, and agility across the entire supply chain.
Benefits of Integration
The integration between PlanetTogether and leading ERP, SCM, and MES systems offers a myriad of benefits for food and beverage manufacturers:
Real-Time Data Sync: Integration ensures that data is synchronized in real-time across all systems, providing stakeholders with up-to-date information for better decision-making.
Streamlined Processes: By automating data exchange and workflow integration, organizations can streamline processes, reduce manual effort, and minimize errors.
Enhanced Visibility: Integration provides end-to-end visibility into the supply chain, enabling stakeholders to track inventory levels, monitor production progress, and anticipate potential bottlenecks.
Improved Planning and Scheduling: By combining the power of PlanetTogether's advanced planning capabilities with the data accuracy of ERP, SCM, and MES systems, organizations can optimize production plans and schedules for maximum efficiency.
Faster Response to Changes: With integrated systems, organizations can respond quickly to changes in demand, supply, or production constraints, minimizing disruptions and maximizing customer satisfaction.
Best Practices for Integration
To ensure successful integration between PlanetTogether and other enterprise systems, consider the following best practices:
Define Integration Objectives: Clearly define your integration objectives and requirements, taking into account the specific needs of your organization and supply chain processes.
Choose the Right Integration Platform: Select a robust integration platform that supports bi-directional data exchange, workflow automation, and scalability to accommodate future growth.
Collaborate Across Departments: Involve key stakeholders from IT, operations, supply chain, and finance departments in the integration process to ensure alignment of goals and priorities.
Prioritize Data Quality: Invest in data cleansing and normalization to ensure that data exchanged between systems is accurate, consistent, and reliable.
Monitor Performance: Continuously monitor the performance of integrated systems, track key metrics, and make adjustments as needed to optimize efficiency and effectiveness.
The integration of digital supply chain networks is essential for food and beverage manufacturers looking to enhance agility and responsiveness in today's competitive market. By integrating PlanetTogether with leading ERP, SCM, and MES systems, organizations can streamline processes, improve visibility, and optimize planning and scheduling for maximum efficiency and customer satisfaction.
By following best practices and leveraging the power of integration, Supply Chain Managers can position their organizations for success in the digital age. Are you ready to take your manufacturing operations to the next level? Contact us today to learn more about how PlanetTogether can help you achieve your goals and drive success in your industry.
LEAVE A COMMENT