Material Shortage Management
Material shortage management stands as a critical aspect of operations, directly impacting production timelines, customer satisfaction, and ultimately, patient care. As an Operations Director, you bear the responsibility of overseeing this intricate process, requiring effective strategies and robust tools to navigate challenges efficiently.
In this blog, we look into the nuances of material shortage management in medical manufacturing facilities. We will explore the importance of integration between planning software like PlanetTogether and ERP, SCM, and MES systems such as SAP, Oracle, Microsoft, Kinaxis, and Aveva. Additionally, we'll provide actionable insights and best practices to optimize your material shortage management processes.

The Significance of Material Shortage Management
Material shortages can disrupt the entire manufacturing process, leading to delays, increased costs, and compromised quality. In the medical industry, where precision and timeliness are non-negotiable, effective management of material shortages is imperative.
Key challenges in material shortage management include:
Demand Variability: Fluctuating demand for medical products due to factors like seasonal illnesses or unexpected events can lead to unpredictable material requirements.
Supply Chain Disruptions: External factors such as natural disasters, geopolitical issues, or supplier constraints can cause disruptions in the supply chain, resulting in material shortages.
Inventory Visibility: Limited visibility into inventory levels across multiple locations can make it challenging to identify potential shortages in advance.
Communication Gaps: Inefficient communication between stakeholders, including suppliers, manufacturers, and distributors, can exacerbate material shortage issues.
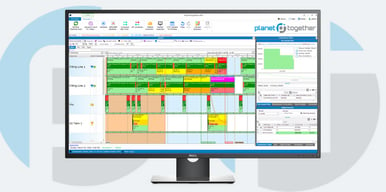
Integration Between PlanetTogether and ERP, SCM, and MES Systems
To effectively manage material shortages, seamless integration between planning software like PlanetTogether and ERP, SCM, and MES systems is essential. Here's how integration facilitates streamlined operations:
Real-Time Data Exchange: Integration allows for the seamless exchange of real-time data between planning and execution systems, providing accurate insights into material availability and demand fluctuations.
Enhanced Visibility: By integrating planning and execution systems, Operations Directors gain comprehensive visibility into inventory levels, production schedules, and supplier statuses, enabling proactive identification and mitigation of material shortages.
Automated Workflows: Integration enables the automation of workflows, such as purchase order generation and inventory replenishment, based on dynamic demand forecasts generated by planning software.
Collaborative Decision-Making: Integrated systems facilitate collaborative decision-making among cross-functional teams, enabling rapid response to material shortage challenges through data-driven insights.
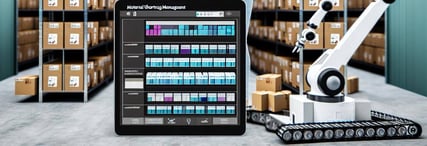
Best Practices for Optimizing Material Shortage Management
Demand Forecasting: Leverage advanced forecasting techniques and historical data analysis to accurately predict demand patterns and anticipate material requirements.
Supplier Relationship Management: Cultivate strong relationships with suppliers and implement risk mitigation strategies, such as dual sourcing and supplier diversification, to minimize the impact of potential disruptions.
Inventory Optimization: Implement inventory optimization strategies, such as just-in-time inventory management and safety stock buffers, to balance inventory levels while mitigating the risk of shortages.
Continuous Improvement: Establish a culture of continuous improvement by regularly reviewing and refining material shortage management processes based on performance metrics and feedback from stakeholders.
Technology Adoption: Embrace emerging technologies such as artificial intelligence and machine learning to enhance demand forecasting accuracy and optimize supply chain efficiency.
Effective material shortage management is essential for maintaining operational excellence and ensuring patient safety in medical manufacturing. By leveraging integration between planning software like PlanetTogether and ERP, SCM, and MES systems, Operations Directors can optimize their material shortage management processes, mitigate risks, and drive sustainable growth.
Implementing best practices such as demand forecasting, supplier relationship management, and continuous improvement will further enhance operational resilience and competitiveness in the evolving healthcare landscape. By embracing technology and fostering collaboration across functions, medical manufacturing facilities can navigate material shortage challenges with confidence, delivering high-quality products to those who need them most.
Are you ready to take your manufacturing operations to the next level? Contact us today to learn more about how PlanetTogether can help you achieve your goals and drive success in your industry.
LEAVE A COMMENT