Quality Function Deployment (QFD)
In the packaging business environment, where competition is fierce and consumer demands are constantly evolving, packaging manufacturers face the challenge of balancing quality, efficiency, and cost-effectiveness. As a Purchasing Manager in a packaging manufacturing facility, you understand the importance of streamlining operations and optimizing processes to stay ahead in the market. One powerful tool at your disposal for achieving these objectives is Quality Function Deployment (QFD).
In this blog, we'll look into the intricacies of Quality Function Deployment and explore how it can be seamlessly integrated with leading ERP, SCM, and MES systems like SAP, Oracle, Microsoft, Kinaxis, Aveva, and others through solutions such as PlanetTogether. By the end of this blog, you'll have a deeper understanding of how QFD can drive efficiency, enhance quality, and ultimately boost your packaging manufacturing facility's competitiveness.
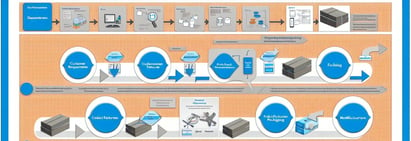
Quality Function Deployment (QFD)
Quality Function Deployment, often abbreviated as QFD, is a systematic methodology used to translate customer requirements into specific product characteristics and manufacturing processes. It originated in Japan in the late 1960s and has since become a widely adopted approach in various industries, including packaging manufacturing.
At its core, QFD aims to align the objectives of different departments within an organization, from design and engineering to production and marketing, with the needs and preferences of customers. By doing so, it ensures that every aspect of the product or service reflects the customer's voice, resulting in higher satisfaction levels and increased competitiveness.
Key Principles of QFD
Voice of the Customer (VOC) Analysis: QFD begins with a thorough analysis of the Voice of the Customer, which involves capturing and understanding customer needs, preferences, and expectations. This step is crucial for identifying the critical features and attributes that will drive customer satisfaction.
Cross-functional Collaboration: QFD encourages collaboration and communication across different departments within an organization. By involving stakeholders from various disciplines, such as design, engineering, manufacturing, and marketing, QFD ensures that all perspectives are considered during the product development process.
Structured Deployment: QFD follows a structured deployment process, typically represented in a matrix format known as the House of Quality. This matrix serves as a visual tool for mapping the relationship between customer requirements, product characteristics, and manufacturing processes, allowing teams to prioritize actions and make informed decisions.
Continuous Improvement: QFD is not a one-time exercise but rather a continuous improvement process. As market dynamics change and customer preferences evolve, organizations must continually revisit and refine their QFD matrices to stay aligned with shifting demands and maintain a competitive edge.

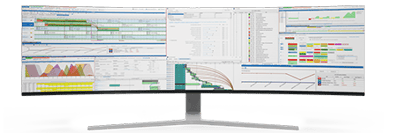
Integration of QFD with ERP, SCM, and MES Systems
In today's digitally driven landscape, the integration of QFD with Enterprise Resource Planning (ERP), Supply Chain Management (SCM), and Manufacturing Execution Systems (MES) is essential for maximizing its effectiveness. By leveraging advanced software solutions like PlanetTogether, which seamlessly integrate with leading ERP systems such as SAP, Oracle, Microsoft Dynamics, and others, packaging manufacturers can streamline their QFD processes and drive operational excellence.
Benefits of Integration
Real-time Data Synchronization: Integration between QFD and ERP, SCM, and MES systems enables real-time data synchronization, ensuring that all stakeholders have access to up-to-date information on customer requirements, inventory levels, production schedules, and quality metrics.
Enhanced Collaboration: By connecting QFD with other enterprise systems, teams can collaborate more effectively across different departments and locations. Whether it's sharing customer feedback, aligning production schedules, or monitoring quality control parameters, integrated systems facilitate seamless communication and collaboration.
Improved Decision-making: Integration empowers decision-makers with comprehensive insights and analytics derived from multiple data sources. Whether it's identifying opportunities for product innovation, optimizing supply chain logistics, or fine-tuning manufacturing processes, integrated systems provide the visibility and intelligence needed to make informed decisions quickly.
End-to-End Traceability: With integrated QFD and MES systems, packaging manufacturers can achieve end-to-end traceability, from raw materials to finished products. This traceability not only enhances quality control and regulatory compliance but also enables proactive risk management and timely issue resolution.
By integrating QFD with leading ERP, SCM, and MES systems through solutions like PlanetTogether, packaging manufacturers can unlock new levels of efficiency, collaboration, and innovation. Whether it's optimizing packaging design, improving supply chain visibility, or enhancing production processes, integrated systems empower organizations to meet the dynamic demands of the market while delivering superior value to customers.
As a Purchasing Manager, embracing QFD and leveraging integration with enterprise systems is not just a strategic choice but a pathway to sustainable growth and success in the packaging manufacturing industry.
Are you ready to take your manufacturing operations to the next level? Contact us today to learn more about how PlanetTogether and integrated scheduling solutions can help you achieve your sustainability goals and drive success in the packaging industry.
LEAVE A COMMENT