Setup Time Optimization
From sourcing ingredients to delivering the final product, every step must be meticulously planned and executed to ensure maximum output with minimal waste in food and beverage manufacturing. At the heart of this complex operation lies production scheduling – the process of determining what to produce, when to produce it, and how to allocate resources effectively. And when it comes to optimizing production scheduling, one key factor that cannot be overlooked is setup times.
Setup times refer to the time it takes to prepare a machine or production line for a new task or product. These setup times can vary significantly depending on factors such as equipment type, product complexity, and production volume. Inefficient setup times can lead to costly delays, increased downtime, and reduced overall productivity. However, with the right approach and technology integration, production planners can effectively manage setup times and streamline their scheduling processes for optimal performance.
In this blog, we'll explore the importance of setup times in production scheduling and discuss how integration between advanced planning and enterprise resource planning (ERP), supply chain management (SCM), and manufacturing execution systems (MES) software, such as PlanetTogether and leading platforms like SAP, Oracle, Microsoft, Kinaxis, and Aveva, can help food and beverage manufacturers achieve greater efficiency and profitability.
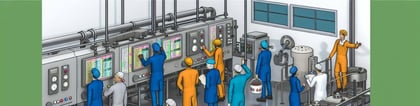
Setup Times in Production Scheduling
Setup times play a crucial role in determining the overall efficiency of manufacturing operations. They encompass activities such as equipment cleaning, changeovers, calibration, and adjustments necessary to switch from one production run to another. Efficient setup times enable manufacturers to quickly transition between different products or batches, thereby reducing idle time and increasing throughput.
However, without proper management, setup times can become a major bottleneck in the production process. Long setup times can lead to excessive downtime, increased labor costs, and missed production targets. Additionally, frequent changeovers may result in product quality issues and waste.
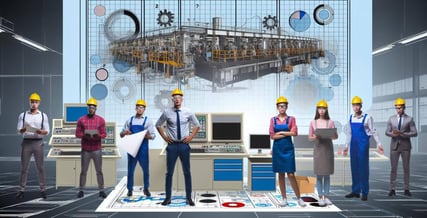
Challenges Faced by Production Planners
Production planners often encounter several challenges when dealing with setup times:
- Complexity: Managing setup times for multiple products, production lines, and resources can be highly complex, especially in a dynamic manufacturing environment.
- Variability: Setup times are not fixed and can vary based on factors such as product specifications, equipment condition, and operator skill level.
- Synchronization: Coordinating setup activities with production schedules and resource availability requires precise planning and coordination.
- Optimization: Identifying opportunities to minimize setup times while maximizing production efficiency requires sophisticated analysis and decision-making.
To address these challenges effectively, production planners need advanced tools and strategies that enable them to optimize setup times and integrate them seamlessly into the scheduling process.
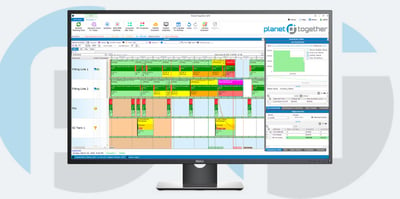
The Role of Integration in Setup Time Optimization
Integration between production scheduling software like PlanetTogether and ERP, SCM, and MES systems such as SAP, Oracle, Microsoft, Kinaxis, and Aveva is essential for achieving setup time optimization. By connecting these systems, manufacturers can streamline data exchange, improve visibility, and facilitate real-time decision-making across the entire production ecosystem.
Here's how integration can enhance setup time optimization:
Real-Time Data Exchange: Integration enables seamless communication between production scheduling software and ERP, SCM, and MES systems, allowing for real-time updates on inventory levels, order status, and resource availability. This visibility ensures that production schedules are always based on the latest information, reducing the risk of disruptions due to inaccurate data.
Advanced Planning Algorithms: Modern production scheduling software, such as PlanetTogether, utilizes advanced algorithms to optimize production schedules based on factors like setup times, production constraints, and customer demand. Integration with ERP and SCM systems provides these algorithms with access to critical data, enabling more accurate and efficient scheduling decisions.
Automated Workflow: Integration allows for the automation of routine tasks such as order processing, inventory management, and production planning. By eliminating manual data entry and streamlining workflows, manufacturers can reduce errors, improve efficiency, and free up valuable time for production planners to focus on strategic tasks.
Predictive Analytics: Integration enables the use of predictive analytics and machine learning algorithms to anticipate production challenges, such as equipment breakdowns or supply chain disruptions, before they occur. By analyzing historical data and identifying patterns, manufacturers can proactively adjust production schedules to mitigate risks and optimize resource utilization.
Best Practices for Setup Time Optimization
To harness the full potential of setup time optimization, food and beverage manufacturers should adopt the following best practices:
Standardize Setup Procedures: Develop standardized procedures for equipment setup and changeovers to minimize variability and reduce setup times. Train operators on best practices and ensure compliance with established protocols.
Invest in Technology: Leverage advanced production scheduling software like PlanetTogether and integrate it with ERP, SCM, and MES systems for seamless data exchange and workflow automation. Explore additional features such as predictive analytics and optimization algorithms to further enhance scheduling efficiency.
Collaborate Across Departments: Foster collaboration between production, maintenance, procurement, and other departments to align objectives and share insights. By breaking down silos and promoting cross-functional teamwork, manufacturers can identify opportunities for improvement and implement solutions collaboratively.
Continuously Monitor and Adapt: Regularly monitor key performance indicators (KPIs) related to setup times, production efficiency, and resource utilization. Use this data to identify areas for improvement and adjust production schedules accordingly. Continuously iterate on scheduling strategies based on real-time feedback and evolving business needs.
Optimizing production scheduling with setup times integration is essential for food and beverage manufacturers looking to stay competitive in today's fast-paced market. By leveraging advanced planning software like PlanetTogether and integrating it with ERP, SCM, and MES systems, manufacturers can streamline operations, minimize setup times, and maximize efficiency across the entire production ecosystem.
With seamless data exchange, real-time visibility, and advanced analytics capabilities, manufacturers can make informed decisions, adapt to changing demand patterns, and deliver high-quality products to customers on time, every time. By embracing integration and adopting best practices for setup time optimization, food and beverage manufacturers can unlock new levels of productivity and profitability in their operations.
In the dynamic world of manufacturing, the journey towards production scheduling excellence never ends. By continually striving for improvement and embracing innovation, manufacturers can position themselves for long-term success in the ever-evolving food and beverage industry.
Are you ready to take your manufacturing operations to the next level? Contact us today to learn more about how PlanetTogether can help you achieve your goals and drive success in your industry.