Production Planning for Chemical Manufacturing Operations Directors
In chemical manufacturing, the introduction of new products is both an exciting opportunity and a significant challenge. As an Operations Director, you understand the crucial role that effective production planning plays in the success of new product launches. With the ever-increasing complexity of supply chains and the need for seamless integration between various systems, it's imperative to adopt advanced planning solutions that can streamline the process and ensure optimal outcomes.
In this comprehensive guide, we will look into the intricacies of production planning for new product introductions in the chemical manufacturing industry. We'll explore the challenges faced, best practices to overcome them, and the role of integrated planning solutions like PlanetTogether in conjunction with leading ERP, SCM, and MES systems such as SAP, Oracle, Microsoft, Kinaxis, and Aveva.
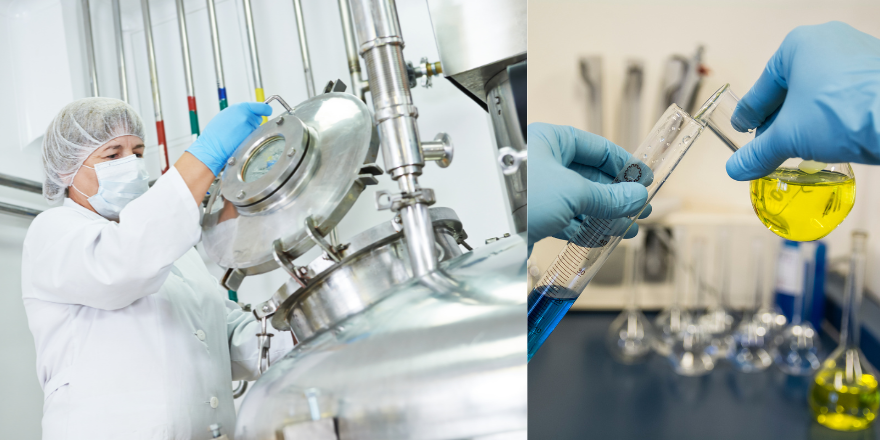
Challenges in New Product Introductions
Launching a new product in the chemical manufacturing sector involves navigating through numerous challenges, including:
Complexity in Formulation: Chemical formulations can be intricate, requiring precise measurements and ingredients. Introducing a new product often involves extensive research and development to ensure the formulation meets regulatory standards and customer requirements.
Regulatory Compliance: Chemical manufacturing is heavily regulated, with stringent standards governing product safety, environmental impact, and labeling requirements. Compliance with regulations such as REACH, GHS, and FDA regulations adds complexity to the product introduction process.
Supply Chain Complexity: Chemical manufacturing supply chains are often global and involve multiple suppliers, distributors, and logistics partners. Coordinating the flow of raw materials, intermediates, and finished products across various geographies poses challenges in inventory management and logistics planning.
Production Capacity and Resource Allocation: Introducing a new product may require adjustments to production capacity and resource allocation. Balancing the demand for existing products with the production needs of the new product while optimizing resource utilization is a critical aspect of production planning.
Time-to-Market Pressure: In today's competitive landscape, speed is of the essence. Minimizing time-to-market for new products is essential to capitalize on market opportunities and gain a competitive edge. Efficient production planning is vital to accelerate the product development and launch process.
Best Practices in Production Planning for New Product Introductions
To effectively address the challenges associated with new product introductions, Operations Directors can implement the following best practices:
Cross-Functional Collaboration: Foster collaboration between R&D, marketing, operations, and supply chain teams to ensure alignment throughout the product development and launch process. Clear communication and collaboration are essential for identifying potential bottlenecks and addressing them proactively.
Data-Driven Decision Making: Leverage data analytics and business intelligence tools to gain insights into market demand, raw material availability, production capacity, and resource utilization. Data-driven decision-making enables Operations Directors to make informed choices and optimize production planning processes.
Scenario Analysis and Simulation: Utilize scenario analysis and simulation tools to assess the impact of different production scenarios on costs, lead times, and resource utilization. By simulating various what-if scenarios, Operations Directors can identify the most efficient production plans and mitigate risks associated with new product introductions.
Continuous Improvement: Implement a culture of continuous improvement within the organization, focusing on optimizing production processes, reducing waste, and enhancing operational efficiency. Regularly review and refine production plans based on feedback, performance metrics, and lessons learned from previous launches.
Integration of PlanetTogether with ERP, SCM, and MES Systems
Integrated planning solutions such as PlanetTogether offer Operations Directors a comprehensive platform to streamline production planning for new product introductions. By integrating with leading ERP, SCM, and MES systems such as SAP, Oracle, Microsoft, Kinaxis, and Aveva, PlanetTogether provides seamless connectivity across the entire supply chain ecosystem.
Here's how the integration between PlanetTogether and these systems enhances production planning for new product introductions:
Real-Time Data Synchronization
Integration with ERP systems ensures real-time synchronization of master data, including product specifications, bill of materials (BOM), and production schedules. This enables Operations Directors to access accurate and up-to-date information for effective planning and decision-making.
Optimized Inventory Management
Integration with SCM systems enables better inventory visibility and control throughout the supply chain. Operations Directors can optimize inventory levels, reduce stockouts, and minimize excess inventory by synchronizing demand forecasts with production schedules.
Shop Floor Visibility
Integration with MES systems provides real-time visibility into shop floor operations, including machine status, production progress, and quality control data. This allows Operations Directors to monitor production performance, identify bottlenecks, and take corrective actions to ensure on-time delivery of new products.
Enhanced Collaboration
Integration with collaboration platforms such as Microsoft Teams or Slack facilitates communication and collaboration across cross-functional teams involved in new product introductions. Operations Directors can coordinate tasks, share updates, and resolve issues in real-time, improving overall project efficiency.
Streamlined Workflows
Integration between PlanetTogether and ERP, SCM, and MES systems streamlines end-to-end production workflows, from demand planning and procurement to manufacturing and distribution. By automating repetitive tasks and eliminating manual data entry, Operations Directors can optimize process efficiency and reduce lead times.
Mastering production planning for new product introductions in the chemical manufacturing industry requires a combination of strategic foresight, cross-functional collaboration, and advanced planning solutions.
By adopting best practices and leveraging integrated planning solutions like PlanetTogether in conjunction with leading ERP, SCM, and MES systems, Operations Directors can streamline production processes, accelerate time-to-market, and drive business growth in today's competitive marketplace.
Remember, the key to success lies in embracing innovation, harnessing the power of data, and continuously optimizing production planning processes to stay ahead of the curve. With the right tools and strategies in place, your organization can navigate the complexities of new product introductions with confidence and achieve sustainable success in the dynamic world of chemical manufacturing.
LEAVE A COMMENT