Mastering Multi-Criteria Decision Making in Scheduling
In industrial manufacturing, where time, resources, and efficiency are of the essence, scheduling plays a pivotal role. As a Purchasing Manager, you understand the criticality of optimizing production schedules to meet demands while minimizing costs and maximizing resource utilization. However, achieving such optimization isn't a straightforward task. It requires a sophisticated approach that considers multiple criteria simultaneously.
In this blog, we look into the realm of multi-criteria decision making in scheduling, exploring its significance, challenges, and the integration between PlanetTogether and leading ERP, SCM, and MES systems like SAP, Oracle, Microsoft, Kinaxis, Aveva, and others to streamline the process.
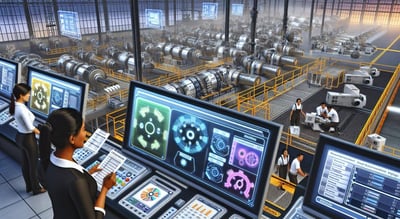
Multi-Criteria Decision Making
Traditional scheduling approaches often prioritize a single criterion, such as minimizing makespan or maximizing resource utilization. While effective in certain scenarios, these approaches may overlook other crucial factors like cost, flexibility, and customer satisfaction. Multi-criteria decision making (MCDM) acknowledges the complexity of scheduling by considering multiple objectives simultaneously. It involves evaluating and comparing various schedules based on a set of criteria to identify the optimal solution that best balances these objectives.
The Significance of MCDM in Industrial Manufacturing
In industrial manufacturing, where operations are intricate and interconnected, the significance of MCDM in scheduling cannot be overstated. By accounting for diverse criteria such as production costs, lead times, machine utilization, inventory levels, and customer deadlines, MCDM enables Purchasing Managers to make informed decisions that align with organizational goals. Whether it's accommodating rush orders, optimizing resource allocation, or mitigating bottlenecks, MCDM empowers manufacturers to enhance efficiency, productivity, and profitability.
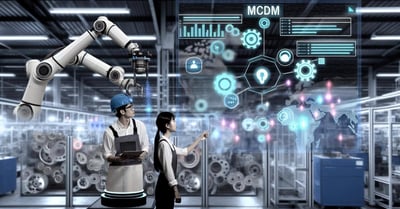
Challenges in MCDM Scheduling
Implementing MCDM in scheduling poses several challenges, including:
Complexity: Evaluating schedules based on multiple criteria increases the complexity of decision-making processes.
Conflicting Objectives: Different stakeholders may prioritize conflicting objectives, necessitating trade-offs and compromises.
Data Availability and Accuracy: MCDM relies on accurate and timely data from various sources, which may be challenging to obtain and validate.
Computational Intensity: Analyzing numerous scheduling alternatives requires sophisticated algorithms and computational resources.
Dynamic Environment: Manufacturing environments are often dynamic, with demand fluctuations, machine breakdowns, and other unforeseen events impacting scheduling decisions.

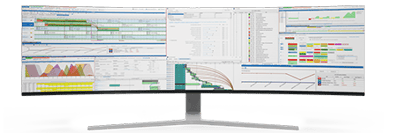
Integration of PlanetTogether with ERP, SCM, and MES Systems
To address these challenges and streamline MCDM scheduling, integration between advanced scheduling software like PlanetTogether and leading ERP, SCM, and MES systems is crucial. These integrations enable seamless data exchange, real-time synchronization, and enhanced visibility across the manufacturing ecosystem.
Here's how integration with platforms such as SAP, Oracle, Microsoft, Kinaxis, Aveva, and others facilitates MCDM scheduling:
Data Integration: Integration allows for the automatic exchange of data between scheduling software and ERP, SCM, and MES systems, ensuring consistency and accuracy in information.
Real-Time Updates: By synchronizing data in real-time, integration enables decision-makers to access up-to-date information, facilitating agile and informed decision-making.
Comprehensive Insights: Integration provides comprehensive insights into production processes, inventory levels, resource availability, and order status, empowering Purchasing Managers to evaluate scheduling alternatives based on multiple criteria.
Scenario Analysis: Advanced scheduling software integrated with ERP, SCM, and MES systems facilitates scenario analysis, allowing users to simulate different scheduling scenarios and assess their impact on various criteria.
Optimization Capabilities: Integration enables the application of optimization algorithms to generate schedules that maximize efficiency, minimize costs, and meet organizational objectives.
Best Practices for Leveraging MCDM in Scheduling
To harness the full potential of MCDM in scheduling, Purchasing Managers can adopt the following best practices:
Define Clear Objectives: Identify and prioritize the key objectives and criteria relevant to your manufacturing operations, considering factors such as cost, time, quality, and customer satisfaction.
Collaborative Decision-Making: Involve stakeholders from different departments in the decision-making process to ensure alignment and consensus on scheduling priorities.
Utilize Advanced Tools: Leverage advanced scheduling software equipped with MCDM capabilities and integration with ERP, SCM, and MES systems to automate and streamline scheduling processes.
Monitor and Adapt: Continuously monitor performance metrics and KPIs to assess the effectiveness of scheduling decisions, and be prepared to adapt strategies based on changing conditions.
Invest in Training and Education: Provide training and education to personnel involved in scheduling to enhance their understanding of MCDM principles and tools, fostering a culture of continuous improvement.
In the competitive landscape of industrial manufacturing, mastering multi-criteria decision making in scheduling is imperative for achieving operational excellence. By considering diverse objectives and leveraging advanced scheduling software integrated with ERP, SCM, and MES systems, Purchasing Managers can optimize schedules to maximize efficiency, minimize costs, and enhance customer satisfaction.
Embracing MCDM principles and best practices empowers manufacturers to navigate complexities, adapt to dynamic environments, and stay ahead of the curve in today's rapidly evolving market.
Incorporating MCDM into scheduling processes isn't just a strategic advantage—it's a necessity for manufacturers striving to thrive in an increasingly competitive and demanding industry. With the right approach and tools, Purchasing Managers can unlock new levels of efficiency, agility, and profitability, positioning their organizations for sustained success in the digital era of manufacturing.
Are you ready to take your manufacturing operations to the next level? Contact us today to learn more about how PlanetTogether can help you achieve your goals and drive success in your industry.
LEAVE A COMMENT