Mastering Capacity Planning
Capacity planning emerges as a cornerstone for success in chemical manufacturing where precision and efficiency are essential. As an Operations Director in this industry, you're undoubtedly familiar with the challenges of orchestrating production amidst fluctuating demands, resource constraints, and market dynamics.
In this blog, we'll look deep into the art and science of capacity planning, exploring strategies, tools, and integrations that can empower your facility to optimize production, streamline processes, and stay ahead in a competitive market.
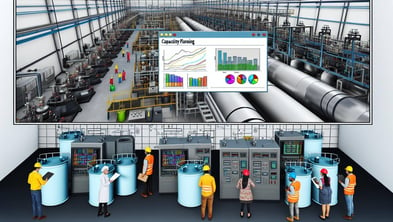
Capacity Planning
Capacity planning is the process of determining the production capacity needed by an organization to meet changing demands for its products. It involves forecasting future demand, evaluating existing resources, and aligning production capabilities to fulfill customer requirements efficiently. In the context of chemical manufacturing, where operations are often complex and multifaceted, effective capacity planning becomes even more critical.
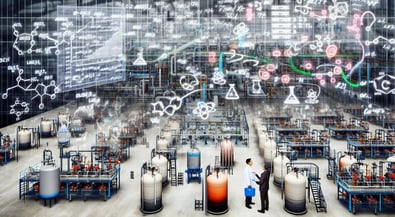
The Challenges of Capacity Planning in Chemical Manufacturing
Dynamic Demand Patterns: Chemical manufacturing is subject to volatile market demands influenced by factors such as seasonal variations, economic trends, and regulatory changes. Predicting and accommodating these fluctuations pose significant challenges for capacity planners.
Resource Constraints: From raw materials to equipment and manpower, chemical production relies on a myriad of resources. Balancing these resources to match demand while optimizing utilization requires meticulous planning and coordination.
Process Complexity: Chemical manufacturing processes are often intricate, involving precise formulations, stringent quality standards, and intricate supply chains. Coordinating these processes to maximize efficiency without compromising product integrity is a delicate balancing act.
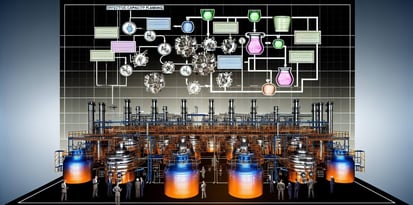
Strategies for Effective Capacity Planning
Data-Driven Forecasting: Leverage historical data, market insights, and advanced forecasting techniques to predict demand patterns accurately. Utilize predictive analytics tools to anticipate future demand fluctuations and adjust production plans accordingly.
Scenario Analysis: Conduct scenario-based planning to evaluate various production scenarios and their impact on capacity utilization, resource allocation, and profitability. This allows you to identify potential bottlenecks and devise contingency plans to mitigate risks.
Optimized Resource Allocation: Employ sophisticated scheduling algorithms to optimize resource allocation across different production lines, shifts, and processes. Consider factors such as equipment availability, skill requirements, and downtime to maximize operational efficiency.
Collaborative Planning: Foster collaboration between different departments, suppliers, and stakeholders involved in the production process. Establish clear communication channels and shared visibility into production schedules to enhance coordination and responsiveness.
The Role of Technology in Capacity Planning
In today's digital era, technology plays a pivotal role in enhancing capacity planning capabilities. Advanced software solutions, such as Enterprise Resource Planning (ERP), Supply Chain Management (SCM), and Manufacturing Execution Systems (MES), offer robust features for forecasting, scheduling, and resource optimization. Integration between these systems enables seamless data exchange and real-time decision-making, streamlining the entire capacity planning process.
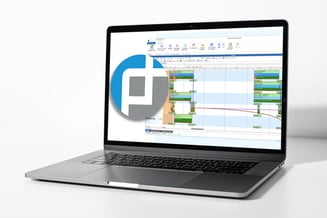
Integration with PlanetTogether: Unlocking Synergies
PlanetTogether is a leading provider of advanced production planning and scheduling software, renowned for its flexibility, scalability, and optimization capabilities. By integrating PlanetTogether with your existing ERP, SCM, and MES systems, you can harness the full potential of your manufacturing ecosystem, driving efficiency and agility across the board.
Benefits of Integration:
Real-Time Data Sync: Integration ensures seamless synchronization of data between PlanetTogether and your ERP, SCM, and MES systems, eliminating data silos and enabling real-time decision-making based on the latest information.
End-to-End Visibility: Gain comprehensive visibility into your manufacturing operations, from raw material procurement to finished product delivery. Monitor production schedules, resource utilization, and inventory levels across the entire supply chain with ease.
Optimized Production Scheduling: Leverage advanced scheduling algorithms within PlanetTogether to create optimized production schedules aligned with your capacity constraints, resource availability, and demand fluctuations.
Improved Collaboration: Facilitate collaboration between different departments and stakeholders by providing a unified platform for sharing production plans, schedules, and performance metrics.
In chemical manufacturing, effective capacity planning is the key to maintaining a competitive edge. By adopting data-driven strategies, leveraging advanced technologies, and embracing integration between systems like PlanetTogether and SAP, Oracle, Microsoft, Kinaxis, Aveva, and others, you can optimize production operations, minimize costs, and enhance customer satisfaction.
As an Operations Director, your role in championing these initiatives is crucial for driving organizational success in today's dynamic marketplace. Embrace the power of capacity planning and propel your chemical manufacturing facility towards excellence.
Are you ready to take your manufacturing operations to the next level? Contact us today to learn more about how PlanetTogether can help you achieve your goals and drive success in your industry.
LEAVE A COMMENT