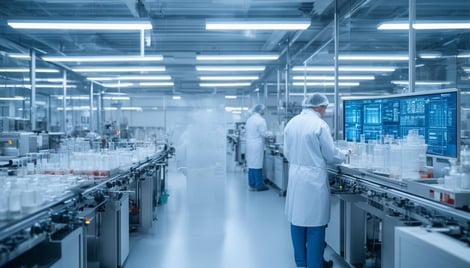
Mastering Batch Production Scheduling Techniques in Pharmaceutical Manufacturing
Effective batch production scheduling is a cornerstone of operational excellence in pharmaceutical manufacturing. The complexity of managing formulations, compliance requirements, and strict timelines makes the task uniquely challenging. For production schedulers, the ability to master batch production scheduling techniques is not only a professional advantage but also a necessity for ensuring product quality, safety, and on-time delivery.
This blog explores actionable techniques to master batch production scheduling and highlights how integrating advanced planning tools like PlanetTogether with enterprise systems such as SAP, Oracle, Microsoft Dynamics, Kinaxis, or Aveva can elevate efficiency and streamline operations.
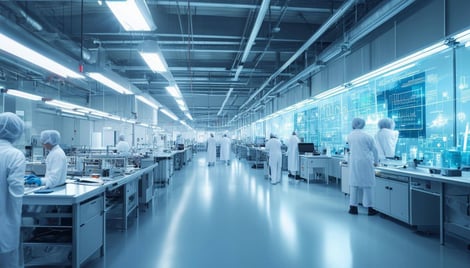
The Complex Nature of Pharmaceutical Batch Production Scheduling
Pharmaceutical manufacturing is characterized by:
Regulatory Compliance: Adhering to Good Manufacturing Practices (GMP) and stringent FDA regulations.
Product Complexity: Managing diverse formulations, some requiring multi-stage production.
Variable Demand: Adapting to demand shifts driven by market needs, pandemics, or supply disruptions.
Resource Constraints: Balancing limited equipment availability, cleanroom requirements, and workforce expertise.
Traceability: Ensuring end-to-end documentation for quality control and audits.
With these challenges, scheduling must be precise, agile, and data-driven.
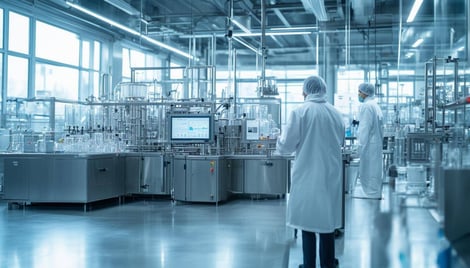
Techniques for Mastering Batch Production Scheduling
Prioritize Demand-driven Scheduling
Demand forecasting is critical in pharmaceutical production, where overproduction leads to wastage, and underproduction risks patient safety. Integrating sales and operations planning (S&OP) data into the scheduling process ensures that production aligns with real-time demand signals.
How Integration Helps: By connecting PlanetTogether with tools like SAP or Kinaxis, schedulers can automatically pull demand forecasts, update production priorities, and respond dynamically to market shifts.
Optimize Equipment Utilization
Pharmaceutical manufacturing often relies on specialized equipment. Ensuring optimal equipment utilization is critical, especially for high-value assets like reactors and granulators.
Technique:
Use capacity-constrained scheduling to balance workloads.
Sequence batches to minimize changeover times, reducing the need for extensive cleaning and validation.
How Integration Helps: Integrating Aveva’s asset performance management (APM) with PlanetTogether can provide real-time insights into equipment status, ensuring that scheduling accounts for maintenance or downtime.
Incorporate Predictive Maintenance
Unexpected equipment failure can derail schedules, especially in a cleanroom environment where downtime can extend due to decontamination protocols.
Technique:
Schedule preventive maintenance alongside production.
Use predictive analytics to anticipate potential failures.
How Integration Helps: The integration of predictive maintenance data from Microsoft Dynamics 365 or Oracle Cloud Maintenance into PlanetTogether allows schedulers to foresee potential disruptions and adjust production plans proactively.
Focus on Batch Size Optimization
Determining the optimal batch size is vital for cost efficiency and meeting demand without excess inventory.
Technique:
Analyze historical data for demand patterns.
Implement flexible batch sizing based on market and production constraints.
How Integration Helps: PlanetTogether’s integration with SAP Advanced Planning and Optimization (APO) enables real-time analysis of inventory levels and production capacities, ensuring batch sizes align with business goals.
Streamline Cleanroom Transitions
Cleanroom requirements demand strict adherence to contamination control protocols, often leading to bottlenecks in production.
Technique:
Sequence similar product batches together to minimize transitions.
Use real-time monitoring to track cleanroom readiness.
How Integration Helps: Connecting Aveva’s cleanroom monitoring systems with PlanetTogether ensures that scheduling decisions incorporate cleanroom availability, reducing idle time and ensuring compliance.
Leverage Real-time Visibility for Enhanced Collaboration
Pharmaceutical manufacturing involves multiple stakeholders, including quality assurance, supply chain, and production teams.
Technique:
Use centralized dashboards for transparency.
Enable cross-functional collaboration for decision-making.
How Integration Helps: By linking Kinaxis RapidResponse with PlanetTogether, organizations can create a unified planning ecosystem where stakeholders collaborate effectively on a single source of truth.
Scenario Planning for Risk Management
Scenario planning allows schedulers to anticipate disruptions, such as raw material shortages or regulatory changes.
Technique:
Develop contingency plans for key risk scenarios.
Use digital twins to simulate production adjustments.
How Integration Helps: PlanetTogether’s integration with Oracle Integrated Business Planning enables scenario modeling, helping schedulers evaluate the impact of different variables and choose the most resilient plan.
Why Integration is the Key to Mastery
Batch production scheduling is no longer a standalone task. It demands seamless integration of multiple systems for real-time data exchange, predictive analytics, and cross-functional collaboration. Tools like PlanetTogether, when integrated with enterprise solutions such as SAP, Oracle, Microsoft Dynamics, Kinaxis, or Aveva, empower schedulers to:
Increase Accuracy: Automatically update schedules based on live data.
Enhance Efficiency: Minimize manual effort and reduce errors.
Boost Agility: Respond swiftly to market or operational changes.
Ensure Compliance: Automate documentation and reporting for regulatory audits.
By mastering batch production scheduling techniques and leveraging the power of integration, production schedulers can become catalysts for efficiency, innovation, and growth in pharmaceutical manufacturing.
The future of pharmaceutical manufacturing hinges on precision, agility, and technology. For production schedulers, tools like PlanetTogether, integrated with ERP and supply chain platforms, are not just an advantage—they are essential for navigating complexity and driving success.
Are you ready to take your manufacturing operations to the next level? Contact us today to learn more about how PlanetTogether can help you achieve your goals and drive success in your industry.
LEAVE A COMMENT