Mastering Backward Scheduling
The pressure for precision, compliance, and efficiency is undeniable in pharmaceutical manufacturing. Production planners are the linchpins in ensuring these elements come together seamlessly, ensuring that products are delivered on time without sacrificing quality or increasing costs. A pivotal strategy in achieving this goal is backward scheduling. By planning production tasks in reverse—from the delivery date to the start of manufacturing—production planners can ensure that operations stay within strict timelines while minimizing downtime and inventory costs.
When integrated with sophisticated planning systems like PlanetTogether, as well as ERP solutions such as SAP, Oracle, Microsoft Dynamics, Kinaxis, or Aveva, backward scheduling becomes even more powerful. These integrations provide a comprehensive view of resources, materials, and timelines, allowing pharmaceutical production planners to optimize workflows and keep production running smoothly even in the face of unforeseen challenges.
This blog looks into the concept of backward scheduling, explores its significance in pharmaceutical manufacturing, and highlights how the integration of PlanetTogether with top ERP systems can transform your scheduling approach.
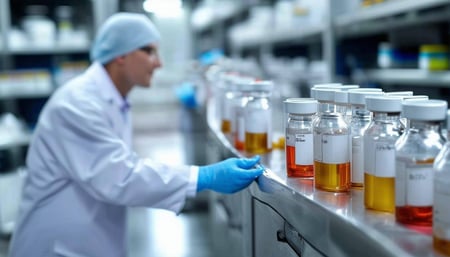
Backward Scheduling: A Key Concept in Pharmaceutical Production Planning
Backward scheduling is a planning approach that starts with the end goal—the product’s due date—and works backward through each step of the production process to determine the optimal start time for each task. In industries like pharmaceuticals, where precision and timing are crucial, this approach helps ensure that every step is completed within the necessary timeframe without creating bottlenecks or excess inventory.
Backward scheduling is particularly advantageous in pharmaceutical manufacturing due to:
Tight Regulatory Timelines: Many pharmaceutical products require stringent testing, approval processes, and compliance checks that dictate the manufacturing timeline. Backward scheduling ensures that these checkpoints are met on time.
Short Product Lifecycles: Pharmaceuticals often have short shelf lives. Backward scheduling minimizes the risk of producing excess inventory that could expire before reaching consumers.
High Cost of Materials: Managing inventory through backward scheduling helps prevent overstocking high-cost raw materials that can be sensitive to environmental factors or have limited shelf life.

Challenges of Backward Scheduling in Pharmaceutical Manufacturing
While backward scheduling is invaluable, it does come with unique challenges, particularly in the highly regulated pharmaceutical industry. Some common challenges include:
Complex Dependencies: Pharmaceutical production often involves multiple interdependent processes, each with specific timing requirements that must align perfectly for compliance and quality.
Material Constraints: Many pharmaceutical ingredients are sensitive to storage conditions or have strict expiration dates, making it critical to time their procurement and usage accurately.
Regulatory Compliance: Meeting Good Manufacturing Practice (GMP) guidelines and ensuring all documentation is up-to-date requires close coordination across all production stages.
Integrating PlanetTogether with ERP systems such as SAP, Oracle, Microsoft Dynamics, Kinaxis, or Aveva can help overcome these challenges by automating scheduling, optimizing resource allocation, and providing real-time insights into production progress.

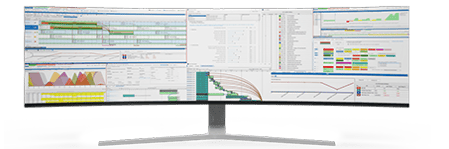
PlanetTogether in Backward Scheduling
PlanetTogether is a powerful Advanced Planning and Scheduling (APS) solution designed to streamline and optimize production planning. It offers features like real-time data visibility, resource scheduling, and constraint management, which are especially useful in backward scheduling for pharmaceutical manufacturing. By integrating PlanetTogether with an ERP system, production planners can achieve:
Real-Time Visibility: The integration enables live updates on resource availability, inventory levels, and production progress, providing production planners with the data they need to make informed decisions.
Automated Scheduling Adjustments: As changes occur in demand, inventory, or production capacity, PlanetTogether can adjust schedules automatically, maintaining adherence to timelines even when unforeseen changes arise.
Resource and Material Optimization: PlanetTogether, combined with ERP data, ensures that every resource is optimally allocated, minimizing idle times and reducing the risk of missing deadlines.
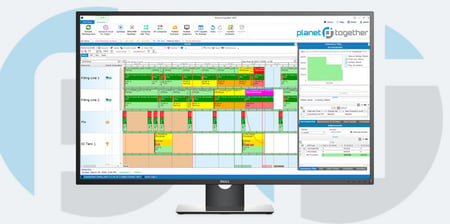
Integration with ERP Systems: Streamlining Pharmaceutical Production
When PlanetTogether is integrated with ERP systems such as SAP, Oracle, Microsoft Dynamics, Kinaxis, or Aveva, production planners gain access to a complete ecosystem of tools for efficient scheduling and resource management.
Here’s how these integrations enhance backward scheduling:
SAP Integration: SAP’s robust data management capabilities allow PlanetTogether to pull up-to-the-minute information on inventory, production orders, and resources. With this data, PlanetTogether can make real-time adjustments to schedules based on inventory levels or production needs, ensuring that every step of the production process aligns with deadlines.
Oracle Integration: Oracle’s flexible ERP suite provides data on materials, workflows, and compliance standards, which can be synchronized with PlanetTogether’s APS capabilities. This integration supports accurate backward scheduling by automating adjustments to ensure that the production process meets regulatory standards and avoids costly delays.
Microsoft Dynamics Integration: Microsoft Dynamics is known for its ease of use and adaptability, making it an ideal ERP for pharmaceutical companies that need fast data access and intuitive reporting. By integrating with PlanetTogether, production planners can leverage backward scheduling with up-to-date information on resource availability and project timelines, keeping operations smooth and aligned with delivery dates.
Kinaxis Integration: Kinaxis specializes in rapid response planning and supply chain optimization. Integrated with PlanetTogether, it enables production planners to react to supply chain disruptions immediately, automatically adjusting the backward schedule to accommodate delays or shortages and maintaining production continuity.
Aveva Integration: Aveva’s expertise in industrial information management enhances backward scheduling by providing critical insights into asset performance, ensuring production resources are used effectively. Integration with PlanetTogether allows pharmaceutical production planners to align asset usage with scheduled tasks, improving efficiency and meeting production timelines.
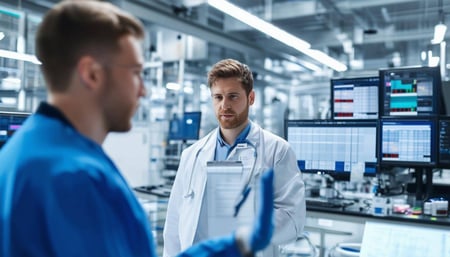
Key Benefits of Integrating PlanetTogether with ERP Systems for Backward Scheduling
Integrating PlanetTogether with ERP systems for backward scheduling offers pharmaceutical production planners several key benefits:
Enhanced Compliance: Backward scheduling integrated with ERP data ensures that each stage of production meets regulatory requirements without unexpected delays. Automatic scheduling adjustments ensure compliance documentation is always current and accurate.
Inventory Optimization: Pharmaceutical manufacturing often requires precise inventory management due to the perishability of raw materials. PlanetTogether’s backward scheduling, enhanced with ERP inventory data, ensures that materials are ordered and used just in time, reducing waste and controlling costs.
Improved Capacity Planning: With real-time resource and capacity data from ERP systems, PlanetTogether can allocate resources more effectively. This ensures that each production phase is completed on time, reducing the risk of bottlenecks and minimizing downtime.
Reduced Costs: By optimizing the use of resources and inventory, PlanetTogether helps reduce the overall cost of production. Additionally, backward scheduling minimizes the likelihood of rush orders or last-minute adjustments, which can be costly.
Increased Agility: The pharmaceutical market can be unpredictable, with shifts in demand and regulatory changes. PlanetTogether, integrated with ERP data, allows production planners to adapt quickly to these changes, ensuring that timelines remain on track without compromising quality or compliance.
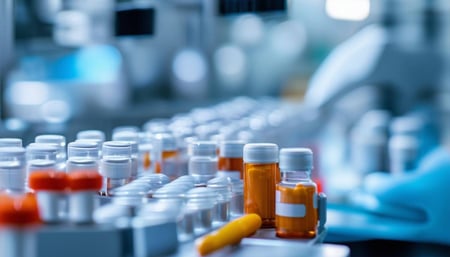
Practical Steps for Implementing Backward Scheduling with PlanetTogether and ERP Systems
For production planners looking to leverage the power of backward scheduling, here are some steps to consider when implementing PlanetTogether with your ERP system:
Assess Your Current Scheduling Process: Start by understanding how your current scheduling approach functions. Identify any areas where delays or bottlenecks occur and evaluate how backward scheduling could help mitigate these issues.
Identify Key Data Points: Integrating PlanetTogether with an ERP system requires accurate data. Work with your IT and production teams to identify key data points such as inventory levels, resource availability, and task dependencies, and ensure these are updated in real-time.
Set Up Automated Scheduling Rules: Once your data is integrated, configure PlanetTogether to automatically adjust schedules based on real-time updates from your ERP. For instance, if a key ingredient is delayed, the system should automatically adjust the schedule to account for this.
Monitor and Adjust: Implementing backward scheduling is not a one-time setup. Continuously monitor the process, making adjustments as needed to ensure schedules remain accurate and resources are optimized.
Invest in Training: Ensure that all stakeholders are trained to use both PlanetTogether and the integrated ERP system effectively. Understanding how to interpret and act on scheduling data is essential for maximizing the benefits of backward scheduling.
Backward scheduling is an invaluable tool for pharmaceutical production planners, offering a structured approach to meeting strict production deadlines while optimizing resources. When combined with PlanetTogether’s scheduling capabilities and integrated with powerful ERP systems like SAP, Oracle, Microsoft Dynamics, Kinaxis, or Aveva, it becomes even more effective. This integration provides production planners with real-time insights and automated adjustments, enabling them to navigate the complexities of pharmaceutical manufacturing with confidence and efficiency.
For production planners in the pharmaceutical industry, the integration of backward scheduling and ERP systems isn’t just about meeting timelines—it’s about achieving the precision and compliance that are essential in bringing safe, effective medications to market. By leveraging the power of PlanetTogether and a robust ERP system, production planners can transform their scheduling practices, delivering results that align with business goals and regulatory demands alike.
Are you ready to take your manufacturing operations to the next level? Contact us today to learn more about how PlanetTogether can help you achieve your goals and drive success in your industry.