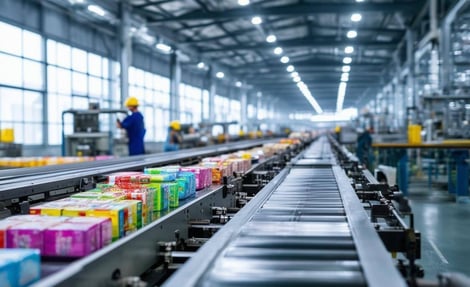
Managing Complex Projects in Production Scheduling for Packaging Manufacturing
In the packaging manufacturing landscape, managing production schedules has grown increasingly complex. Manufacturers face challenges like fluctuating demand, limited resources, and the integration of advanced digital technologies. For Manufacturing IT Managers, the task of optimizing production scheduling is critical, especially when managing complex projects with overlapping dependencies and tight timelines.
One solution that stands out is integrating advanced scheduling platforms, such as PlanetTogether, with Enterprise Resource Planning (ERP) systems like SAP, Oracle, Microsoft Dynamics, Kinaxis, or Aveva.
This blog will explore strategies to manage complex production scheduling projects effectively and how leveraging such integrations can streamline processes, enhance visibility, and ensure success.
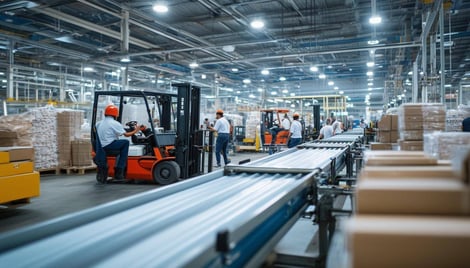
The Challenges of Complex Production Scheduling in Packaging Manufacturing
Complex production scheduling involves coordinating multiple variables: raw materials, production lines, labor availability, and shipping deadlines. These factors become more challenging when managing overlapping projects or dealing with:
High Product Variability: Packaging manufacturers often produce a wide range of products in varying volumes, requiring intricate planning.
Stringent Deadlines: Clients expect quick turnarounds without compromising quality.
Resource Constraints: Limited machine availability or labor shortages can lead to delays.
Regulatory Compliance: Packaging for industries like food, pharmaceuticals, or chemicals requires adherence to strict standards.
For IT Managers, addressing these challenges demands robust systems that facilitate seamless data flow and real-time decision-making.
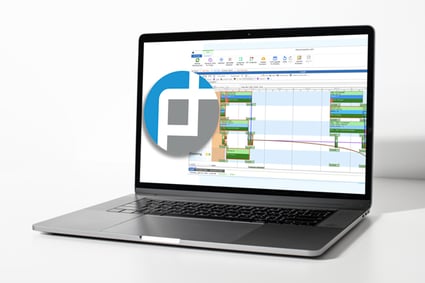
Why Integration Matters: PlanetTogether with ERP Systems
Standalone tools for scheduling or ERP systems often fall short in addressing the nuanced demands of complex scheduling. Integrating a production scheduling tool like PlanetTogether with ERP platforms (SAP, Oracle, Microsoft Dynamics, Kinaxis, or Aveva) can resolve these gaps. Here's how:
Enhanced Data Synchronization
Integration ensures that production schedules are continuously updated with the latest data from the ERP system, including inventory levels, sales orders, and capacity planning.
Improved Resource Allocation
PlanetTogether can utilize ERP data to allocate resources optimally, ensuring machines and labor are used efficiently across projects.
Scenario Planning and Optimization
The combined power of PlanetTogether and ERP systems allows IT Managers to simulate various scenarios, adjusting schedules dynamically based on real-time data.
End-to-End Visibility
Integration provides a unified view of operations, enabling IT Managers to monitor production progress, identify bottlenecks, and make informed decisions.
Regulatory Compliance
Synchronization ensures that the production process adheres to all required certifications and standards, reducing the risk of non-compliance.
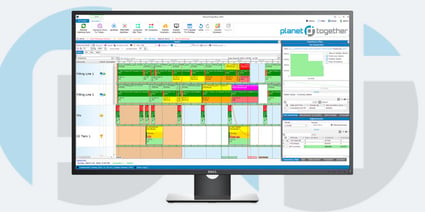
Key Strategies for Managing Complex Projects in Production Scheduling
Prioritize Real-Time Visibility
Integrating PlanetTogether with an ERP system offers a centralized platform to track production schedules in real time. Visibility into each production stage helps identify and resolve issues promptly, minimizing delays.
Leverage Advanced Analytics
Advanced analytics within PlanetTogether, combined with ERP data, can provide actionable insights. For example, analyzing historical performance data to predict machine downtime or labor shortages enables proactive planning.
Implement Agile Scheduling Practices
Use PlanetTogether’s capabilities to create flexible schedules that adapt to changes. Agile scheduling ensures production can pivot quickly in response to urgent orders or unexpected disruptions.
Focus on Collaboration
Integration fosters better collaboration between teams, as everyone—from production to procurement—accesses the same data. For IT Managers, ensuring smooth data sharing between PlanetTogether and ERP systems is key to breaking down silos.
Scenario Testing and Risk Management
The ability to simulate scenarios in PlanetTogether empowers IT Managers to foresee potential risks. For instance, testing the impact of machine maintenance on production deadlines allows for preemptive adjustments.
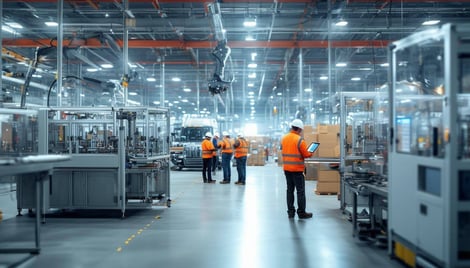
The Role of IT Managers in Successful Integration
The success of integrating PlanetTogether with ERP systems hinges on the expertise of IT Managers. Here’s how IT Managers can drive these projects:
Assess Compatibility
Evaluate the existing ERP system and ensure it can seamlessly interface with PlanetTogether.
For instance, systems like SAP and Microsoft Dynamics often have pre-built connectors to simplify integration.
Ensure Data Integrity
Establish protocols for accurate data exchange between systems to avoid errors in production scheduling.
Facilitate Change Management
Guide teams in adopting new workflows enabled by the integration. Provide training to ensure smooth transition and long-term success.
Monitor Performance
Continuously track the performance of the integrated system to identify areas for improvement.
Align with Strategic Goals
Ensure that integration aligns with the broader goals of the organization, such as cost reduction, sustainability, or customer satisfaction.
Managing complex projects in production scheduling is a demanding task, especially in packaging manufacturing. For Manufacturing IT Managers, the key to success lies in leveraging robust tools like PlanetTogether and integrating them with ERP systems like SAP, Oracle, Microsoft Dynamics, Kinaxis, or Aveva. This integration fosters efficiency, visibility, and agility—essential qualities for navigating the challenges of modern manufacturing.
By prioritizing real-time data, collaboration, and advanced analytics, IT Managers can transform production scheduling into a streamlined, value-driven process. Are you ready to take your manufacturing operations to the next level? Contact us today to learn more about how PlanetTogether can help you achieve your goals and drive success in your industry.