
Managing Changeovers: A Strategic Imperative for Chemical Manufacturing IT Managers
In chemical manufacturing, operational efficiency often hinges on the delicate balance between maximizing production uptime and managing necessary changeovers. While essential for maintaining product quality and meeting diverse customer demands, changeovers are inherently disruptive. For Manufacturing IT Managers, the challenge lies in leveraging technology to streamline these transitions, ensuring minimal downtime while upholding safety and compliance standards.
In this blog, we explore how integrating advanced production scheduling tools like PlanetTogether with enterprise systems such as SAP, Oracle, Microsoft Dynamics, Kinaxis, or Aveva can revolutionize changeover management in chemical manufacturing facilities.
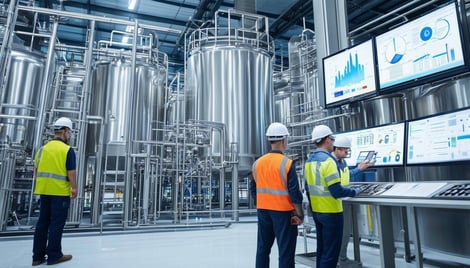
Understanding the Complexity of Changeovers
Chemical manufacturing processes are intricate, involving reactors, mixers, and other equipment that must be meticulously cleaned and reconfigured during changeovers. The complexity arises from:
Product Diversity: A wide range of chemicals, each with unique formulations and handling requirements.
Regulatory Compliance: Strict adherence to safety and environmental standards.
Batch Sensitivity: Ensuring no cross-contamination between products.
Resource Constraints: Limited availability of skilled personnel and equipment.
Poorly managed changeovers can lead to production delays, increased costs, and potential compliance violations, making it imperative to adopt a robust strategy.
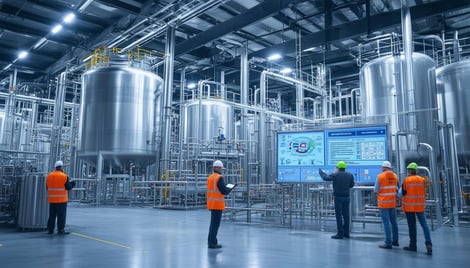
Challenges in Traditional Changeover Management
Traditional approaches to managing changeovers often rely on manual processes and disconnected systems. These methods are prone to:
Inefficiencies: Lack of synchronization between production schedules and resource availability.
Human Error: Increased risk of errors during planning and execution.
Limited Visibility: Difficulty in tracking progress and identifying bottlenecks in real-time.
Without the right tools, IT managers face an uphill battle in coordinating the complex interplay of variables that define successful changeovers.

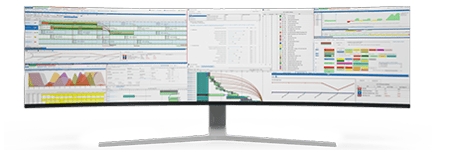
The Role of Integrated Production Scheduling
Integrating PlanetTogether’s advanced production scheduling capabilities with ERP and MES platforms like SAP, Oracle, Microsoft Dynamics, Kinaxis, or Aveva provides a holistic solution to these challenges. Here’s how:
Real-Time Visibility and Decision-Making
Integration enables real-time data exchange between systems, providing a unified view of production schedules, equipment status, and resource availability. This visibility allows IT managers to:
Identify optimal times for changeovers based on production demand.
Monitor progress in real-time to address issues proactively.
Evaluate the impact of changeovers on overall production efficiency.
For instance, syncing PlanetTogether with SAP’s ERP module ensures that material requirements planning (MRP) aligns seamlessly with production schedules, reducing idle time and resource waste.
Enhanced Planning and Optimization
Advanced algorithms in PlanetTogether optimize changeover sequencing, minimizing transitions between similar product types to reduce cleaning and reconfiguration time. When integrated with systems like Oracle or Kinaxis, this optimization extends to supply chain planning, ensuring raw material availability aligns with production needs.
Key benefits include:
Reduced downtime through efficient scheduling.
Lower risk of contamination by optimizing equipment usage.
Improved adherence to production timelines.
Resource Allocation and Workforce Management
Managing changeovers requires precise coordination of labor and equipment. Integration with workforce management tools in platforms like Microsoft Dynamics or Aveva ensures:
Automatic scheduling of skilled personnel for critical tasks.
Streamlined communication between teams.
Better utilization of resources, avoiding overloading or underutilization.
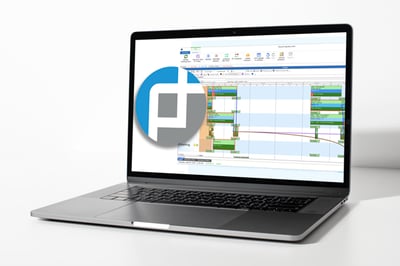
Streamlining Changeovers with PlanetTogether Integration
Here’s a look at how a Manufacturing IT Manager can implement and benefit from this integration:
Data Synchronization
Ensure seamless data flow between PlanetTogether and the chosen enterprise platform. For example:
Integrate SAP’s production planning module to align raw material supply with production schedules.
Use Aveva’s MES capabilities to track equipment status and readiness.
Changeover Sequencing
Utilize PlanetTogether’s scheduling engine to:
Prioritize changeovers based on production demand and equipment readiness.
Group similar products to minimize cleaning time.
Account for regulatory constraints during sequencing.
Real-Time Monitoring
Leverage the integration to monitor changeovers in real-time. For instance:
Use Microsoft Dynamics to track workforce allocation and performance.
Employ Oracle’s analytics tools to measure the efficiency of completed changeovers.
Continuous Improvement
Analyze data collected during changeovers to identify improvement opportunities. Tools like Kinaxis can model scenarios, helping IT managers test and refine strategies for better outcomes.
For Manufacturing IT Managers in chemical facilities, managing changeovers efficiently is critical to maintaining operational excellence. Integrating advanced scheduling tools like PlanetTogether with platforms such as SAP, Oracle, Microsoft Dynamics, Kinaxis, or Aveva provides a powerful framework to address this challenge. By enhancing visibility, optimizing planning, and streamlining execution, these integrations enable IT managers to transform changeovers from a bottleneck into a competitive advantage.
With the right technology and strategy, the path to seamless changeovers is within reach, driving efficiency, compliance, and profitability in chemical manufacturing. Are you ready to take your manufacturing operations to the next level? Contact us today to learn more about how PlanetTogether can help you achieve your goals and drive success in your industry.
LEAVE A COMMENT