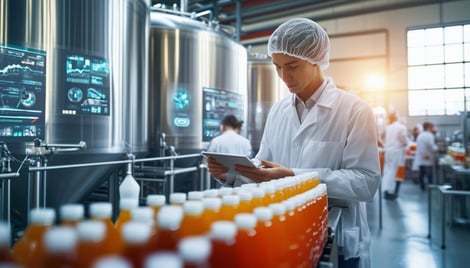
Managing Capacity Peaks in High-Demand Scenarios in Food and Beverage Manufacturing
In food and beverage manufacturing, production schedulers play a pivotal role in ensuring smooth operations, especially during high-demand periods. Peaks in capacity usage can result in strain on resources, production delays, and increased operational costs if not managed effectively.
Leveraging advanced scheduling systems, such as PlanetTogether integrated with ERP solutions like SAP, Oracle, Microsoft, Kinaxis, or Aveva, can significantly enhance your ability to navigate these challenging scenarios.
This blog explores strategies, tools, and best practices to manage capacity peaks and ensure consistent delivery, quality, and profitability.
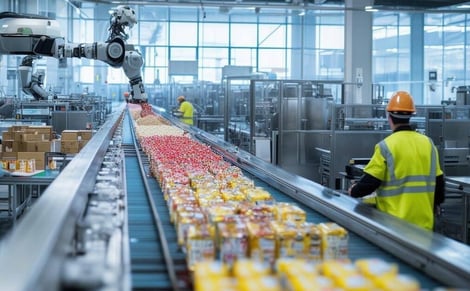
Capacity Peaks in Food and Beverage Manufacturing
Capacity peaks occur when demand outpaces the production facility's baseline capability, often due to seasonal trends, promotional campaigns, or unexpected surges in customer orders. In food and beverage manufacturing, where perishable goods and stringent quality standards are the norm, these peaks present unique challenges:
Short shelf life: Products must be produced and shipped within tight timelines to maintain freshness.
Compliance requirements: Regulatory standards demand meticulous tracking and quality assurance.
Complex supply chains: Ingredients often come from multiple suppliers with varying lead times.
These factors necessitate precise planning, real-time visibility, and dynamic scheduling adjustments.
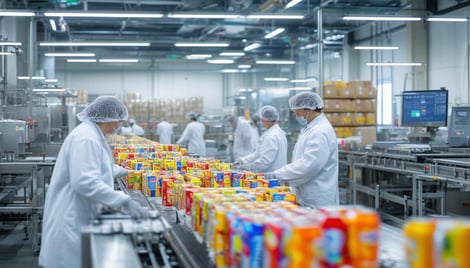
Challenges Faced by Production Schedulers
During high-demand periods, production schedulers grapple with several challenges:
Balancing Resource Utilization: Overburdened resources can lead to breakdowns, while underutilized ones waste capacity.
Supply Chain Disruptions: Increased demand can strain suppliers, leading to delayed or incomplete deliveries.
Order Prioritization: Deciding which orders to prioritize without upsetting customers or exceeding capacity constraints is complex.
Quality Assurance: Scaling production without compromising quality is non-negotiable in food and beverage manufacturing.
To address these challenges, modern schedulers must adopt a proactive approach backed by technology.

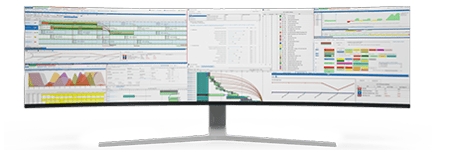
Role of Integrated Scheduling Solutions
Advanced scheduling solutions like PlanetTogether offer robust capabilities to handle capacity management during demand peaks. When integrated with leading ERP systems such as SAP, Oracle, Microsoft, Kinaxis, or Aveva, these tools provide:
Real-Time Visibility
Integration enables a unified view of production schedules, inventory levels, and supplier timelines. Real-time data ensures that schedulers can anticipate bottlenecks and make informed decisions promptly.
Dynamic Rescheduling
PlanetTogether's dynamic rescheduling capabilities, coupled with ERP data, allow schedulers to adapt to changing priorities or unforeseen disruptions. For example, if a supplier delay occurs, the system can automatically adjust the production sequence to minimize downtime.
Advanced Analytics
Integrated analytics help identify patterns in demand surges and resource utilization. This predictive insight allows schedulers to prepare for future capacity peaks with confidence.
Improved Collaboration
With seamless communication between PlanetTogether and ERP platforms, production, procurement, and sales teams can work collaboratively. This alignment ensures that all departments are informed and synchronized during high-demand scenarios.
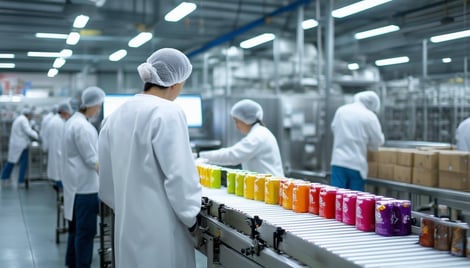
Strategies for Managing Capacity Peaks
Forecasting and Demand Planning
Accurate forecasting is the foundation of effective capacity management. By leveraging integrated tools, production schedulers can analyze historical data, market trends, and seasonal patterns to predict demand surges.
Example: Using PlanetTogether integrated with SAP's forecasting module, schedulers can create detailed demand plans that align with production capabilities.
Resource Optimization
Maximizing the utilization of existing resources is critical. Strategies include:
Cross-training staff to handle multiple roles during demand peaks.
Staggering shifts to ensure continuous operation without overburdening employees.
Optimizing machine schedules to reduce changeover times and increase throughput.
PlanetTogether's resource optimization feature can simulate various scenarios to identify the most efficient production plan.
Prioritization of Orders
During high-demand periods, not all orders can be fulfilled simultaneously. Using PlanetTogether's integration with ERP systems like Microsoft Dynamics, schedulers can prioritize orders based on profitability, customer importance, and deadlines.
Buffer Inventory Management
While lean manufacturing emphasizes minimal inventory, maintaining strategic buffers for critical ingredients can mitigate supply chain risks during demand surges. Integrated systems ensure these buffers are tracked and replenished efficiently.
Scenario Planning
What-if scenario planning allows schedulers to evaluate different strategies for managing capacity peaks. For example, PlanetTogether's scenario analysis feature can simulate the impact of adding a temporary production line or outsourcing certain processes.
The Benefits of Integrated Solutions
By integrating PlanetTogether with ERP systems like SAP, Oracle, Microsoft, Kinaxis, or Aveva, food and beverage manufacturers can unlock several benefits:
Reduced Downtime: Real-time adjustments prevent delays caused by resource bottlenecks.
Enhanced Agility: Dynamic rescheduling ensures that production plans adapt to changing circumstances.
Cost Savings: Optimized resource utilization and reduced waste translate to lower operational costs.
Improved Customer Satisfaction: On-time delivery and consistent quality foster customer loyalty.
Managing capacity peaks in high-demand scenarios is a complex but achievable goal for production schedulers in food and beverage manufacturing. The key lies in combining proactive strategies with advanced technology. Integrated solutions like PlanetTogether and leading ERP systems empower schedulers to maintain operational efficiency, meet customer expectations, and achieve business goals during the most challenging times.
Investing in such technologies will be essential for staying ahead in the competitive food and beverage industry. By implementing these practices and leveraging the right tools, production schedulers can transform capacity peaks from potential disruptions into opportunities for growth and efficiency.
Are you ready to take your manufacturing operations to the next level? Contact us today to learn more about how PlanetTogether can help you achieve your goals and drive success in your industry.