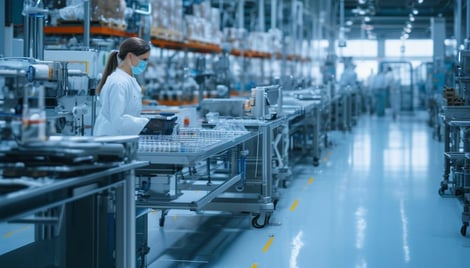
Lifecycle Impact Assessments in Supply Chain Planning: A Strategic Advantage for Medical Manufacturing
The importance of sustainable and efficient supply chain planning cannot be overstated. As global regulatory frameworks tighten, customer expectations shift toward sustainability, and the industry contends with resource constraints, lifecycle impact assessments (LCA) emerge as a critical tool for supply chain managers.
Leveraging technology, particularly the integration of advanced systems like PlanetTogether with enterprise resource planning platforms such as SAP, Oracle, Microsoft, Kinaxis, or Aveva, can revolutionize how LCAs are conducted, leading to smarter, greener, and more cost-effective decisions.
What is a Lifecycle Impact Assessment (LCA)?
A lifecycle impact assessment evaluates the environmental effects of a product throughout its entire lifecycle—from raw material extraction and production to transportation, usage, and disposal. LCAs enable supply chain managers to identify inefficiencies, reduce carbon footprints, and align operations with sustainability goals.
For medical manufacturing, the stakes are particularly high. Medical products must meet stringent quality and safety standards, making it imperative to balance sustainability initiatives with operational efficiency. Integrating LCA into supply chain planning not only satisfies regulatory requirements but also demonstrates a commitment to corporate social responsibility, enhancing brand reputation.
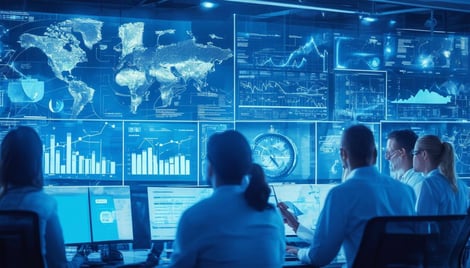
The Challenges of Lifecycle Impact Assessment in Medical Manufacturing
While the benefits of LCAs are evident, their implementation within a medical manufacturing context poses several challenges:
Complex Regulatory Requirements
Medical products are subject to strict regulations, such as FDA guidelines in the United States and MDR in the European Union. These frameworks demand precise documentation and thorough validation, complicating the incorporation of LCAs.
Data Silos
Medical manufacturing supply chains often operate in silos, with fragmented data stored across multiple systems. This lack of integration hinders the comprehensive analysis required for accurate LCAs.
Dynamic Supply Chains
With global supply networks and fluctuating demand, medical manufacturers must remain agile. Ensuring that LCAs account for these dynamics adds complexity to the process.
Technology Gaps
Many organizations lack the advanced tools necessary to conduct LCAs effectively, relying on manual methods that are time-consuming and prone to errors.
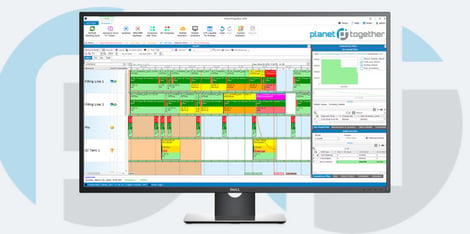
The Role of Technology in Streamlining LCAs
The integration of tools like PlanetTogether with ERP systems such as SAP, Oracle, Microsoft Dynamics, Kinaxis, or Aveva can address these challenges head-on. Here’s how:
Data Unification
Integrating PlanetTogether with an ERP system consolidates data from procurement, production, logistics, and inventory into a single platform. This holistic view ensures that LCAs are based on accurate, real-time information.
Scenario Planning and Optimization
PlanetTogether’s advanced scheduling capabilities enable supply chain managers to simulate various scenarios, evaluating the lifecycle impacts of different strategies. For example, managers can compare the environmental effects of sourcing materials locally versus internationally, or assess the carbon footprint of alternative transportation routes.
Regulatory Compliance
By automating documentation and analysis, integrated systems simplify compliance with regulatory standards. Audit trails and reporting features ensure that all LCA-related activities are transparent and easily accessible.
Dynamic Adjustments
Integrated platforms can dynamically adjust plans based on real-time data, such as shifts in demand or disruptions in the supply chain. This agility is critical in ensuring that LCAs remain relevant and actionable.
Cost Savings
Beyond environmental benefits, LCAs supported by integrated systems can uncover opportunities for cost savings. For instance, reducing waste in production or optimizing transportation routes can lower expenses while also minimizing environmental impacts.
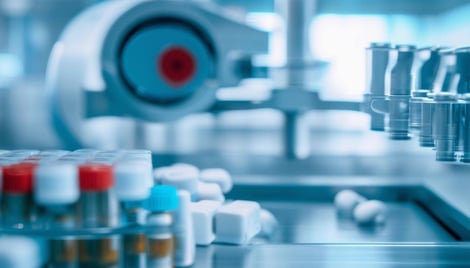
Practical Applications of LCA in Medical Manufacturing Supply Chains
Raw Material Sourcing
LCAs can help identify sustainable suppliers who prioritize ethical practices and lower environmental impacts. With tools like PlanetTogether integrated with SAP or Oracle, supply chain managers can analyze supplier performance, trace material origins, and assess the lifecycle impact of procurement decisions.
Production Efficiency
In medical manufacturing, reducing energy consumption and waste in production processes is critical. Integrated systems allow managers to pinpoint inefficiencies, model improvements, and measure their lifecycle impacts. For example, switching to renewable energy sources or optimizing machine utilization can significantly reduce carbon emissions.
Transportation and Logistics
Transportation often represents a significant portion of a product’s environmental footprint. By leveraging integration between PlanetTogether and platforms like Kinaxis, supply chain managers can simulate and select eco-friendly transportation options. This might involve consolidating shipments, prioritizing fuel-efficient carriers, or leveraging local suppliers.
End-of-Life Management
Medical products often require specialized disposal methods due to their hazardous nature. LCAs can guide decisions on recycling or disposal strategies, ensuring compliance with regulations while minimizing environmental harm. Systems like Aveva, when integrated with PlanetTogether, can offer predictive analytics to manage product end-of-life stages effectively.
Lifecycle impact assessments are no longer optional in medical manufacturing; they are a strategic imperative. By leveraging the integration of PlanetTogether with platforms like SAP, Oracle, Microsoft, Kinaxis, or Aveva, supply chain managers can transform LCAs from a regulatory requirement into a competitive advantage. These tools not only simplify the complex process of conducting LCAs but also unlock new opportunities for sustainability, efficiency, and cost savings.
The journey toward sustainable supply chain planning begins with a commitment to innovation. By embracing advanced technologies and integrating LCAs into their strategies, medical manufacturers can achieve their dual goals of operational excellence and environmental stewardship, setting a new standard for the industry.
Are you ready to take your manufacturing operations to the next level? Contact us today to learn more about how PlanetTogether and integrated scheduling solutions can help you achieve your sustainability goals and drive success in the medical industry.