With the rising costs of production, many manufacturers are looking for ways to increase efficiency in their production system to remain competitive in the market. One commonly used technique is lean manufacturing which aims to reduce waste from the production process to cut costs and increase efficiency.
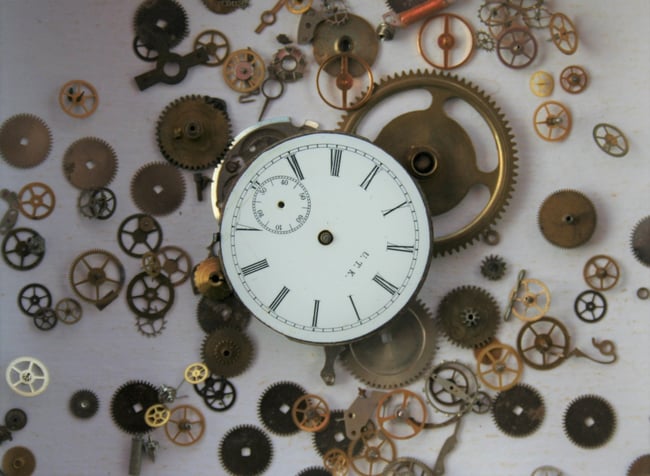
What is Lean Manufacturing?
Lean manufacturing processes were originally developed by Toyota and focus on eliminating any steps in the manufacturing process that do not ultimately satisfy the end consumer to increase efficiency.
The goal of lean production is to minimize all activities that are not valuable to the production process by reducing the time required for production while improving the quality of products and reducing the number of resources used in production. Removing waste from the system reduces the time required for production while improving the quality of the products and reducing the overall costs.
Just-In-Time production is one of the essential concepts employed in a lean manufacturing system.
What is Just-In-Time?
Just-in-Time's basic premise refers to the idea of producing items only as they are needed to eliminate waste of all types in the manufacturing process. JIT is also known as demand-pull production where production is triggered by customer orders. When used in conjunction with lean manufacturing methods, the total system increases profit for the manufacturer.
Just-In-Time scheduling can also:
- Make operations more efficient
- Boost product quality
- Reduce production and inventory costs
- Enable faster delivery
Just-In-Time production requires detailed planning and scheduling to ensure that the supplies are available on time so that production can begin as soon as possible. Advanced Planning and Scheduling softwares are helpful as they combine demand planning, production planning and scheduling, distribution planning, and transportation planning. This ensures that all parts of the manufacturing process are regulated and work in sync with each other.
Just-In-Time Purchasing
Just-in-Time purchasing is one of the most familiar lean manufacturing tools. This concept refers to the ability of a manufacturing facility to order whatever they need when they need it. For many years, keeping an extensive inventory of raw material and spare parts was considered a basic tenet of manufacturing. After all, why waste time waiting for parts and supplies to arrive from a dealer?
Today, these vast warehouses of supplies are no longer a hallmark of a well-run manufacturing facility. Manufacturing has shifted away from business models based on producing specialized products over the course of years, and toward a model of vast product diversification with short production runs. A plant with the ability to produce for months without reordering is now a thing of the past.
Facilities with the ability to quickly adapt to market changes without incurring high inventory costs now have a higher value. Fortunately, the modern supply chain makes it possible to order many materials that a factory needs and have them available within a matter of hours or days.
A modern manufacturer strives for ready access to material without the cost and liability of storing it in their facilities. Lean manufacturing now relies on advanced manufacturing software and can track the location and price of all available materials. The software acts as a communication tool, providing visibility to suppliers on material needs in advance, thus making it possible to get the best price and the fastest delivery times.
Just-In-Time Manufacturing and Inventory
Just-in-Time manufacturing focuses on reducing inventory. The goal is for a factory floor to produce only what is needed to fill orders by reducing production lead times to be less than the customer’s acceptable wait time. Whereas outdated processes would require a company to build a large stockpile of excess product for the quick shipment of product to the customer, Just-in-Time lean manufacturing tools focus on responsive production.
Whenever possible, product is made as orders come in, not in advance of anticipated (and often unpredictable) need. For a facility to meet the goal of eliminating surplus, however, it is necessary to have an agile system in place for scheduling production in small batch sizes without excessive setups. An effective system can control moving those orders through production and to the customer quickly and reliably.
Just-In-Time Distribution
Lean manufacturing tools are designed to facilitate the most efficient method of product shipment possible. Shipping orders efficiently while avoiding excess inventory stockpiles is the goal of Just-in-Time distribution. Traditional distribution methods require “back inventory” to meet peak periods of demand, but a shipping center using Just-in-Time principles can assign products to a destination with greater precision and less waste. Just as Just-in-Time manufacturing limits surplus production, Just-in-Time distribution will store minimal product to satisfy customer orders.
Advanced Planning and Scheduling (APS) Software
Advanced Planning and Scheduling Softwares have become a must for modern-day manufacturing operations as customer demand for increased product assortment, fast delivery, and downward cost pressures become prevalent. These systems help planners save time while providing greater agility in updating ever-changing priorities, production schedules, and inventory plans. APS Systems can be quickly integrated with an ERP/MRP software to fill the gaps where these systems lack planning and scheduling flexibility, accuracy, and efficiency.
With APS you can:
- Create optimized schedules that balance production efficiency and delivery performance
- Maximize throughput on bottleneck resources to increase revenue
- Synchronize supply with demand to reduce inventories
- Provide company-wide visibility to resource capacity
- Enable scenario data-driven decision making
The implementation of an Advanced Planning and Scheduling (APS) Software will take your manufacturing operations to the next level of production efficiency by taking advantage of the operational data you already possess in your ERP system. APS is a step in the right direction of efficiency and lean manufacturing production enhancement. Try out a free trial or demo!
Related Lean Manufacturing Video
APS Resources