Kaizen Practices for Efficiency Enhancement
The need for efficiency is vital in pharmaceutical manufacturing. With stringent regulations, tight deadlines, and ever-evolving market demands, production planners play a pivotal role in ensuring smooth operations.
In this blog, we will look into the concept of Kaizen and explore how its practices can be leveraged to enhance efficiency in pharmaceutical production planning. Additionally, we will discuss the integration of PlanetTogether, a leading production planning software, with various ERP, SCM, and MES systems like SAP, Oracle, Microsoft, Kinaxis, and Aveva, to streamline operations further.
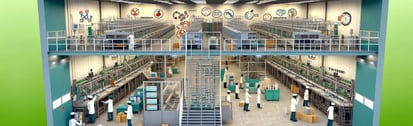
Understanding Kaizen
Kaizen, a Japanese term meaning "continuous improvement," is a philosophy that emphasizes making small, incremental changes to processes to improve efficiency and quality continually. It involves every employee, from top management to frontline workers, and fosters a culture of continuous learning and adaptation. Kaizen principles are highly applicable in pharmaceutical manufacturing, where even minor improvements can lead to significant enhancements in productivity, cost-effectiveness, and compliance.
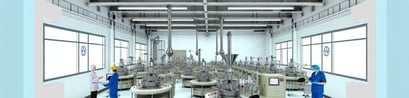
Key Kaizen Practices for Efficiency Enhancement
Gemba Walks: Encourage production planners to conduct Gemba walks, where they observe operations firsthand on the shop floor. This enables them to identify inefficiencies, bottlenecks, and opportunities for improvement. By being directly involved in the production environment, planners gain valuable insights that help optimize scheduling, resource allocation, and workflow management.
Standardized Work Procedures: Establish standardized work procedures for production planning tasks to ensure consistency and minimize errors. Documenting best practices and creating standardized templates for tasks such as batch scheduling, resource allocation, and capacity planning promotes efficiency and reduces variability in operations.
Continuous Training and Skill Development: Invest in training programs to enhance the skills and knowledge of production planners. Providing opportunities for continuous learning in areas such as lean principles, Six Sigma methodologies, and advanced software usage equips planners with the tools they need to identify and implement process improvements effectively.
Cross-Functional Collaboration: Foster collaboration between production planning, manufacturing, quality assurance, and supply chain teams to align goals and streamline processes. By breaking down silos and promoting cross-functional communication, organizations can identify and address issues holistically, leading to smoother operations and better decision-making.
Data-Driven Decision Making: Utilize data analytics and performance metrics to drive decision-making in production planning. By collecting and analyzing key performance indicators (KPIs) such as production throughput, cycle times, and inventory levels, planners can identify areas for improvement and make informed decisions to optimize efficiency and resource utilization.
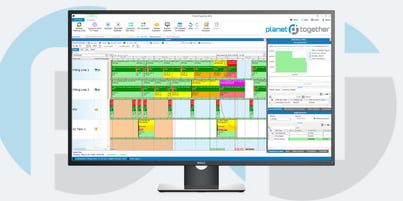
Integration of PlanetTogether with ERP, SCM, and MES Systems
Now, let's explore how the integration of PlanetTogether with leading ERP, SCM, and MES systems such as SAP, Oracle, Microsoft, Kinaxis, and Aveva can further enhance efficiency in pharmaceutical production planning:
Seamless Data Exchange: Integration between PlanetTogether and ERP systems enables seamless exchange of data related to production orders, inventory levels, and resource availability. This ensures that planners have real-time visibility into relevant information, allowing them to make informed decisions and adjust schedules accordingly.
Enhanced Planning Capabilities: By integrating with SCM systems, PlanetTogether gains access to supply chain data, including supplier lead times, material availability, and demand forecasts. This enables more accurate demand planning and inventory management, reducing the risk of stockouts and production delays.
Improved Execution Efficiency: Integration with MES systems facilitates real-time monitoring of production activities, including machine performance, labor utilization, and quality control metrics. This allows planners to proactively address issues as they arise, minimizing downtime and optimizing overall production efficiency.
Streamlined Communication: Integration with ERP, SCM, and MES systems streamlines communication between different departments and systems within the organization. This reduces manual data entry and ensures data accuracy, eliminating errors caused by duplicate data entry or miscommunication.
Holistic Decision Support: By consolidating data from multiple sources, the integrated system provides planners with a holistic view of production operations. This enables them to make data-driven decisions that take into account factors such as resource constraints, lead times, and regulatory requirements, optimizing efficiency while maintaining compliance.
Adopting Kaizen practices and leveraging advanced production planning software such as PlanetTogether, integrated with ERP, SCM, and MES systems, can significantly enhance efficiency in pharmaceutical manufacturing. By fostering a culture of continuous improvement, standardizing work procedures, promoting cross-functional collaboration, and harnessing the power of data analytics, organizations can optimize production planning processes and achieve their operational goals more effectively.
Embracing Kaizen principles and investing in the right tools and technologies will not only drive efficiency but also position pharmaceutical manufacturers for long-term success in a competitive industry landscape.